ichiban
100 W
"My kWeld's Mod "
This post is about how to make kWeld to work with 0.15mm Ni(Fe) + 0.20mm Cu sandwich reliably at ≈1,7xx Amps @140Joules. If your stock kWeld can do that already, that's perfect. Mine had some problems so I need to fix/modify it. Whole mods cost mostly from material (cables & Cu rod, Cu bar, lugs, etc. ), labor and time. This post is like my own memo for my mods and share to you guys for the possibilities to improve your already high potential kWeld. This is rather a story telling style, bare with me - you might get something useful. Some members struggling with this, please read on.
I am building a pack of 20S3P of Samsung 21700-40T for my new DH e-bike (long delayed for years). Though this pack is far from high power, Cu is still preferable than Nickel for its ≈4X better conductivity and if I can weld Cu, it enables me to leap a step toward making big & high current pack. Given that using Cu is as cheap as Nickel but with much better performance. The 0.2-mm minimum thickness Cu is my choice because some ES members used kWeld to weld it before. I thought 0.2mm Cu is almost the limit of current kWeld with regular sandwiching technique, where both probes are on top of Ni(Fe), Cu in the middle, and cell cap at the lowest.
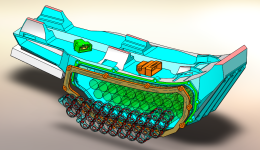
This post is about how to make kWeld to work with 0.15mm Ni(Fe) + 0.20mm Cu sandwich reliably at ≈1,7xx Amps @140Joules. If your stock kWeld can do that already, that's perfect. Mine had some problems so I need to fix/modify it. Whole mods cost mostly from material (cables & Cu rod, Cu bar, lugs, etc. ), labor and time. This post is like my own memo for my mods and share to you guys for the possibilities to improve your already high potential kWeld. This is rather a story telling style, bare with me - you might get something useful. Some members struggling with this, please read on.
I am building a pack of 20S3P of Samsung 21700-40T for my new DH e-bike (long delayed for years). Though this pack is far from high power, Cu is still preferable than Nickel for its ≈4X better conductivity and if I can weld Cu, it enables me to leap a step toward making big & high current pack. Given that using Cu is as cheap as Nickel but with much better performance. The 0.2-mm minimum thickness Cu is my choice because some ES members used kWeld to weld it before. I thought 0.2mm Cu is almost the limit of current kWeld with regular sandwiching technique, where both probes are on top of Ni(Fe), Cu in the middle, and cell cap at the lowest.
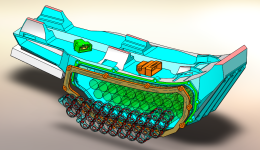