ChubbyQuark
1 mW
Hi everyone,
First post here but long time learner from the great knowledge available. I've searched other threads but can't find any symptons that match what is described below.
This build started about 6 years ago, with the following components:
Cromotor (I believe it's a v3)
Battery - Wallen power 72v 20AH, 60A continuous discharge current
Greyborg frame (concentric bottom bracket)
Twist throttle
Controller 01 (Currently on the bike. 18 Fet, I think it's an Infineon, see pic. below)
Controller 02 (I think it's a Lyen 18 Fet 4115, this has connectors for a cycle analyst and programming and 3 speed setting)
So the bike has been tested with both controllers, controller 01 gives plenty of torque, but hesitates slightly at low throttle(around a third)/RPM. Controller 02 spins the wheel very slowly but also pulses like controller 01. Controller 02 is programable but I'm not sure if the software and cable required for this are available anymore?
Strangely when the bike gets up to speed the pulsing seems to fade away, do you think this is because the controller needs programming to match the battery and motor?
I've checked the hall wires all read voltage of 0.4-4.9 when tested to ground when the wheel is spun backwards, so they seem good.
Any advice on what these controller are would be greatly appreciated, and if it's possible to program controller 02? Perhaps I'd be better off buying a more update controller to math the system?
Thanks in advance!
Controller 01
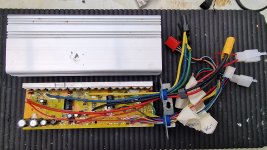
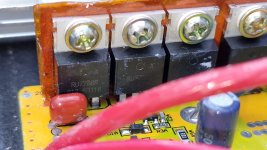
Controller 02
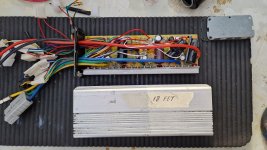
First post here but long time learner from the great knowledge available. I've searched other threads but can't find any symptons that match what is described below.
This build started about 6 years ago, with the following components:
Cromotor (I believe it's a v3)
Battery - Wallen power 72v 20AH, 60A continuous discharge current
Greyborg frame (concentric bottom bracket)
Twist throttle
Controller 01 (Currently on the bike. 18 Fet, I think it's an Infineon, see pic. below)
Controller 02 (I think it's a Lyen 18 Fet 4115, this has connectors for a cycle analyst and programming and 3 speed setting)
So the bike has been tested with both controllers, controller 01 gives plenty of torque, but hesitates slightly at low throttle(around a third)/RPM. Controller 02 spins the wheel very slowly but also pulses like controller 01. Controller 02 is programable but I'm not sure if the software and cable required for this are available anymore?
Strangely when the bike gets up to speed the pulsing seems to fade away, do you think this is because the controller needs programming to match the battery and motor?
I've checked the hall wires all read voltage of 0.4-4.9 when tested to ground when the wheel is spun backwards, so they seem good.
Any advice on what these controller are would be greatly appreciated, and if it's possible to program controller 02? Perhaps I'd be better off buying a more update controller to math the system?
Thanks in advance!
Controller 01
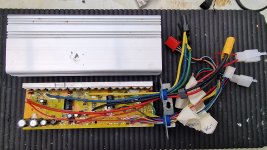
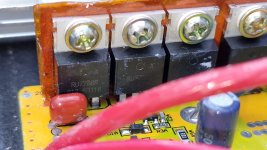
Controller 02
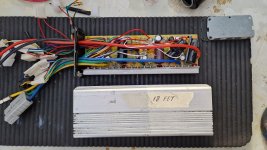