Hi Guys,
I want to build a 18650 batterypack of 403VDC of an Electric vehicle. The battery has 5 Segments of 19s8p. The connections are done via copper-nickel(0.1mm copper and 0.1mm Pure nickel) sandwich method. I have built my own spotwelder using MOT. i have used 35mm2 copper wire for secondary with 2 turns. Pure copper electrodes. Output Voltage is 1.8 volts and current is >400A (Maximum i could read via my clampmeter).Theoratically it should be >1200A.i am using arduino and a relay for control. The pulse is set for 220ms through Trial and error. If the pulse is set for less than 100ms, it doesnt weld properly.
I am getting consistent welds, but the cell is heating up considerably. Now i do not know that it is normal or not but i can feel the heat with my bare hands throughout the cell. Its not too hot but one can easily feel it.
I do not want to damage cells, so i am considering using a thinner wire and more turns on the secondary winding to increase the voltage to around 12V so that the heating issue is resolved.
What are the other ways i can do to prevent this.
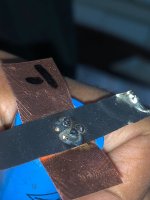
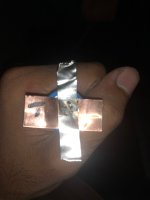
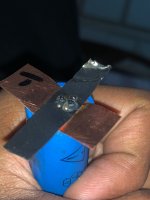
I want to build a 18650 batterypack of 403VDC of an Electric vehicle. The battery has 5 Segments of 19s8p. The connections are done via copper-nickel(0.1mm copper and 0.1mm Pure nickel) sandwich method. I have built my own spotwelder using MOT. i have used 35mm2 copper wire for secondary with 2 turns. Pure copper electrodes. Output Voltage is 1.8 volts and current is >400A (Maximum i could read via my clampmeter).Theoratically it should be >1200A.i am using arduino and a relay for control. The pulse is set for 220ms through Trial and error. If the pulse is set for less than 100ms, it doesnt weld properly.
I am getting consistent welds, but the cell is heating up considerably. Now i do not know that it is normal or not but i can feel the heat with my bare hands throughout the cell. Its not too hot but one can easily feel it.
I do not want to damage cells, so i am considering using a thinner wire and more turns on the secondary winding to increase the voltage to around 12V so that the heating issue is resolved.
What are the other ways i can do to prevent this.
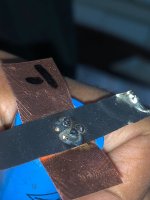
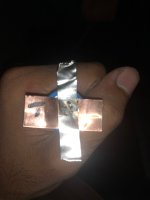
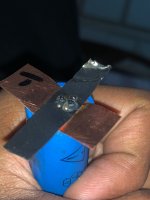