pianoman
10 mW
- Joined
- May 29, 2011
- Messages
- 29
Cromotor with temp probe from Methods, laced in 17 inch steel moped rim, front wheel 17 inch moped rim as well, rims and spokes from JRHolmes, dmr revolver 36h front hub
Tires: Michelin Pilot Street 60/90x17 (2.25 equivalent) front, 70/90x17 (2.5 equivalent) rear, thick tubes and Slime just in case
CA V3
Cell man a123 24s6p split pack with 80a continuous bms, half in triangle, half over top tube
3 speed switch
Atomlab pimp 2 cromoly dirt jump frame with 5mm thick rear horizontal tight dropouts
9mm stainless steel custom cut torque arm on one side, 5mm on the other
Rockshox domain u-turn suspension fork set at aprox. 120mm travel, thru axle, strong single crowne, thick and firm 35mm steel stanchions,link to specs: http://www.sram.com/rockshox/products/domain-r
Avid bb7 203mm front 203 and rear 160mm rear disk brakes
Zombiess 24fet 4110 controller, programmed to 135a battery 200a phase (80v A123 battery)
Zombiess throttle tamer
Led headlights 1 high 1000lum, 1 low 1000lum, taillight with brake signal, front and rear turn signals, motorcycle horn, all works from main battery, connected to CA outlet using AC to DC converter which was power supply for external hard drive
Heavy duty double leg stand
Bag over triangle, can hold additional 9ah a123 battery or can be used for storage
Converted to single speed, 38 tooth chainring 16t sprocket, uses chain tensioner, larger surface pedals and Redline Microline 135mm crankarms for better ground clearance
Very quick acceleration, Zombiess throttle tamer very usefull for smooth takoffs
Top speed 65 km/h on fresh charge
Runs much cooler then previous modified 9c, small wheel make huge difference aside from cromotor being much stronger. In summer temps 70-80 degrees celcius in normal use, only in long and climbs can go over 100
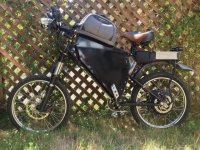
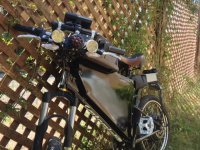
Here is built history:
I have done 3 ebike projects so far, first 2 were 9c 9x7 48v kits on 14ah sla and 33a controller, one front with thick steel fork and other rear drive, both on xc entry level aluminium mountain bikes, by then didn’t know almost anything about ebikes. Then modified the rear drive one to 72v setup on 6 14ah sla and lyen 12fet, but bike was far too heavy, had poor handling and simply didn’t feel strong enough at 60kmh. Finally upgraded front 9x7 bike to higher voltage with lyen12fet at 30a and changed sla to 24s4p a123 from cell man, so that’s a fast but not very powerfull commuter. Then I decided to build a 3rd bike which would be higher power setup with good front suspension for fast rides on pavement and some moderate hill climb capability. This one is my latest build and has the following setup:
HS3540 motor air cooled in 26 inch wheel, 8 20mm holes on each side, actually on freewheel side 4 20mm and 4 14mm holes, was afraid to drill all 8 at 20mm thinking the cover could become too weak
Stock phase wires, but with 8awg extension from axle to controller
Lyen 24fet 4110 controller
Cell man a123 24s6p split pack with 80a continuous bms, half in triangle, half over top tube
large screen CA
Temp sensor
3 speed switch
Atomlab pimp 2 cromoly dirt jump frame with 5mm rear horizontal tight dropouts, here's link to specs http://www.atomlab.com/mtbframep2.html
9mm stainless steel custom cut torque arm on one side, 5mm on the other
Rockshox domain u-turn suspension fork set at aprox. 120mm travel, thru axle, strong single crowne, thick and firm 32mm steel stanchions,link to specs: http://www.sram.com/rockshox/products/domain-r
Avid bb7 203mm front and bb5 160mm rear disk brakes
Atomlab pimp rim, sapim 12g spokes on rear wheel
maxxis hookworm tires with downhill tubes and slime
11-32 7 speed freewheel
65tooth chainring (for pedalling at 70 kmh!)
Lights, air horn, etc.
View attachment 10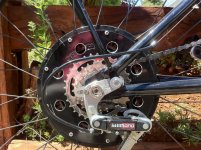
View attachment 7View attachment 5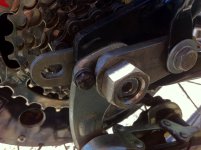
First when bought the motor, I thought I have a 5304 winding and stupidly enough on first test gave it WOT acceleration from still going uphill, as a result in a minute lyen 18fet failed on 60a 150a phase settings, melted phase wires (had not extensions from axle to controller then), overheated motor as well. Then opened and checked the motor, fortunately no damage within it, just some rubbed wires because of axle and side cover design, fixed that removing rubber seal, did phase extensions, drilled holes, upgraded to 24fet and installed temp sensor. After doing some research I now accelerate very gently off line, but give some strong power bursts after reaching about 35kmh and it feels very powerfull at 60a battery, left phase at 115a for now.
I started to suspect the motor not being a 5304 as known from 1st generation, it looks like HS3540 which is between 5304 and 5303 rpmwise, being a bit less hard on controller I guess, at least compared to 5303, that’s a good thing, but maybe HT would have been better eventhough it is a bit too slow at 80v, but closer to my needs then HS. The good thing about it is an excellent mechanical fit, no dishing what makes a stronger wheel, easy disk brake and freewheel fit and less weight.
Would you recommend to swap for HT3540 to have less overheat? 60 kmh top speed is my target, with HT it would be slightly less, but I can live with that if it would have much less overheat issues compared to HS.
Update:
Just drilled some more holes on disk rotor side for air output, it proved to cool much better this way, only thing is that temp reading now is not so precise as cooling affects it directly, according to temp probe temp rises about 10-15 degrees Celsius when I stop (I guess that's because temp sensor is on windings but close to cooling holes, so I normally add 10-15 degrees to the reading I see when in movement), but anyway now I can go 63 kmh constant (about 2200-2500w) with some 3000-4000w on short uphills and temp stays around 100 degrees or less, before it didn't stabilize around 100 and was slowly rising when 63kmh, hottest I let it get was 125. Tests are done with 27 degrees ambient, dry, almost no wind. Controller settings are 65a battery 115a phase, speed 3 (fastest) set to 57 %. Controller temp gets to 50 celcius aprox.
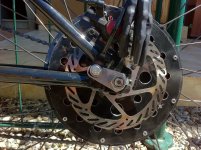
Tires: Michelin Pilot Street 60/90x17 (2.25 equivalent) front, 70/90x17 (2.5 equivalent) rear, thick tubes and Slime just in case
CA V3
Cell man a123 24s6p split pack with 80a continuous bms, half in triangle, half over top tube
3 speed switch
Atomlab pimp 2 cromoly dirt jump frame with 5mm thick rear horizontal tight dropouts
9mm stainless steel custom cut torque arm on one side, 5mm on the other
Rockshox domain u-turn suspension fork set at aprox. 120mm travel, thru axle, strong single crowne, thick and firm 35mm steel stanchions,link to specs: http://www.sram.com/rockshox/products/domain-r
Avid bb7 203mm front 203 and rear 160mm rear disk brakes
Zombiess 24fet 4110 controller, programmed to 135a battery 200a phase (80v A123 battery)
Zombiess throttle tamer
Led headlights 1 high 1000lum, 1 low 1000lum, taillight with brake signal, front and rear turn signals, motorcycle horn, all works from main battery, connected to CA outlet using AC to DC converter which was power supply for external hard drive
Heavy duty double leg stand
Bag over triangle, can hold additional 9ah a123 battery or can be used for storage
Converted to single speed, 38 tooth chainring 16t sprocket, uses chain tensioner, larger surface pedals and Redline Microline 135mm crankarms for better ground clearance
Very quick acceleration, Zombiess throttle tamer very usefull for smooth takoffs
Top speed 65 km/h on fresh charge
Runs much cooler then previous modified 9c, small wheel make huge difference aside from cromotor being much stronger. In summer temps 70-80 degrees celcius in normal use, only in long and climbs can go over 100
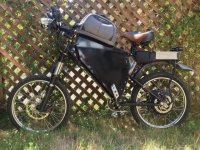
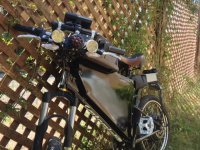
Here is built history:
I have done 3 ebike projects so far, first 2 were 9c 9x7 48v kits on 14ah sla and 33a controller, one front with thick steel fork and other rear drive, both on xc entry level aluminium mountain bikes, by then didn’t know almost anything about ebikes. Then modified the rear drive one to 72v setup on 6 14ah sla and lyen 12fet, but bike was far too heavy, had poor handling and simply didn’t feel strong enough at 60kmh. Finally upgraded front 9x7 bike to higher voltage with lyen12fet at 30a and changed sla to 24s4p a123 from cell man, so that’s a fast but not very powerfull commuter. Then I decided to build a 3rd bike which would be higher power setup with good front suspension for fast rides on pavement and some moderate hill climb capability. This one is my latest build and has the following setup:
HS3540 motor air cooled in 26 inch wheel, 8 20mm holes on each side, actually on freewheel side 4 20mm and 4 14mm holes, was afraid to drill all 8 at 20mm thinking the cover could become too weak
Stock phase wires, but with 8awg extension from axle to controller
Lyen 24fet 4110 controller
Cell man a123 24s6p split pack with 80a continuous bms, half in triangle, half over top tube
large screen CA
Temp sensor
3 speed switch
Atomlab pimp 2 cromoly dirt jump frame with 5mm rear horizontal tight dropouts, here's link to specs http://www.atomlab.com/mtbframep2.html
9mm stainless steel custom cut torque arm on one side, 5mm on the other
Rockshox domain u-turn suspension fork set at aprox. 120mm travel, thru axle, strong single crowne, thick and firm 32mm steel stanchions,link to specs: http://www.sram.com/rockshox/products/domain-r
Avid bb7 203mm front and bb5 160mm rear disk brakes
Atomlab pimp rim, sapim 12g spokes on rear wheel
maxxis hookworm tires with downhill tubes and slime
11-32 7 speed freewheel
65tooth chainring (for pedalling at 70 kmh!)
Lights, air horn, etc.
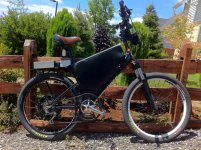
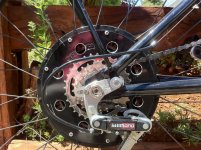
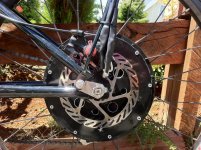
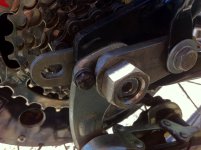
First when bought the motor, I thought I have a 5304 winding and stupidly enough on first test gave it WOT acceleration from still going uphill, as a result in a minute lyen 18fet failed on 60a 150a phase settings, melted phase wires (had not extensions from axle to controller then), overheated motor as well. Then opened and checked the motor, fortunately no damage within it, just some rubbed wires because of axle and side cover design, fixed that removing rubber seal, did phase extensions, drilled holes, upgraded to 24fet and installed temp sensor. After doing some research I now accelerate very gently off line, but give some strong power bursts after reaching about 35kmh and it feels very powerfull at 60a battery, left phase at 115a for now.
I started to suspect the motor not being a 5304 as known from 1st generation, it looks like HS3540 which is between 5304 and 5303 rpmwise, being a bit less hard on controller I guess, at least compared to 5303, that’s a good thing, but maybe HT would have been better eventhough it is a bit too slow at 80v, but closer to my needs then HS. The good thing about it is an excellent mechanical fit, no dishing what makes a stronger wheel, easy disk brake and freewheel fit and less weight.
Would you recommend to swap for HT3540 to have less overheat? 60 kmh top speed is my target, with HT it would be slightly less, but I can live with that if it would have much less overheat issues compared to HS.
Update:
Just drilled some more holes on disk rotor side for air output, it proved to cool much better this way, only thing is that temp reading now is not so precise as cooling affects it directly, according to temp probe temp rises about 10-15 degrees Celsius when I stop (I guess that's because temp sensor is on windings but close to cooling holes, so I normally add 10-15 degrees to the reading I see when in movement), but anyway now I can go 63 kmh constant (about 2200-2500w) with some 3000-4000w on short uphills and temp stays around 100 degrees or less, before it didn't stabilize around 100 and was slowly rising when 63kmh, hottest I let it get was 125. Tests are done with 27 degrees ambient, dry, almost no wind. Controller settings are 65a battery 115a phase, speed 3 (fastest) set to 57 %. Controller temp gets to 50 celcius aprox.
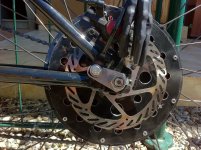