I have a good battery spot welder, and .2mm nickel strip, and then I also have a bunch of 3.5 inch long 1/8 of an inch copper bar that I will solder to the nickel strip first, then spot weld the nickel to the cells.
I ordered some copper/nickel solder paste, and I'm hoping to clean the strips well then place small balls of the solder on the nickel strip then weigh down that on a silicon mat and oven heat the whole thing to the flash temp of the solder.
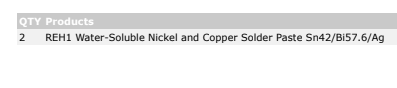
The cells are;
Molicel P45B 21700 4500mAh 45A Battery
40s5p... 168 volt 22.5ah.
Ive got the cell holders, fish paper, and heatshrink. I'll be splitting the battery int he center to load it into the bike, then hard attaching it with either a welder quick disconnect or more copper strip bent and bolted to some sort of busbar attachment.
BMS is a DALY 200 amp 40s, so it will be protected and balanced and also monitorable via bluetooth.
One thing i need to finalise is the way it will anchor in the bike. Maybe straps, maybe solid mounting point in the fiberglass isolator board, maybe wedged with solidcore foam?
I want to be able to jump/lay down this thing so it cant be loose in there. Most companies would latch a hardcase somehow.