Hello,
I have used two 12v packs, of 4 Serial connected 32700 3.2v LifePo4 6000mAh cells, connected in parallel (2P4S) to give theoretical capacity of 12Ah. I am using 14AWG wire for the battery connections. Each 12v pack is protected by 30amp 4S LifePo4 balanced BMS. This battery has been used to replace 7.5Ah SLA battery in a computer UPS. So far it is working very good and providing longer backup than SLA battery.
I have a few questions that I am still confused about and seeking input from everyone to figure out the answers.
1) Should I place a 30amp fuse on P+ port of the both BMS(s) or a 20amp fuse will be just fine?
2)Since the UPS is designed to work with 7.5Ah Sealed Lead Acid (SLA) battery, the charging voltage is set to 13.46volts(3.36v per cell) and can not be changed. I was doing some math, and figured, that at this voltage my LifePo4 cells will be 90% charged and therefore the Battery system will have actual capacity of 10.8Ah instead of the theoretical 12Ah that fully charged cells should have, since 90% of 12 is 10.8. Am I correct in my calculation?
3) When there is a long power outage and the battery gets fully drained, UPS does not automatically start recharging the batteries when the power resumes as the BMS isolates the batteries to prevent complete discharge. I have added a manual momentary switch between B- and P- port of each BMS to manually restart the charging process if the batteries are in over-discharge-protected mode due to a long power outage. How can I automate this process? I am thinking of using a 12v Relay, with High level trigger, and connecting B- of BMS to COMMON port of Relay and P- of BMS to (NC) Normally Closed Port of the Relay. Trigger pin will be connected to 12v charging voltage coming from the UPS. So when there is 12v Power in the system the relay will be in "triggered" state and "(NO)" port will be in "closed" state and "(NC)" Port will be in open state. This way I think B- and P- will always be in shorted state as long as there is no power in the system as soon as there is 12v power in the system P- and B- will get disconnected. Will this setup work to automate recharge reset or can it damage the BMS?
Thanks in advance for your time.
Parts Used:
HX-4S-F30A (LifePo4 Balanced BMS/Blue PCB version) x2
LifePo4 Cells, 32700, 6000mAh, 3C, x8
14 AWG wire and XT-60 Connectors. x6 (3Male, 3Female)
Plastic Battrey case(150x98x94)mm
JST-XH 2 Pin connectors with wire x4 (2Male, 2Female)
Momentary push button switch x2
Here are some photographs:
Current Setup:
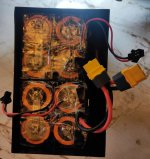
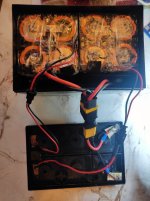
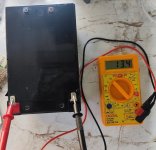
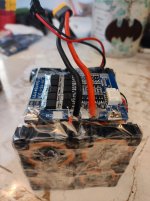
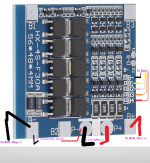
Proposed automation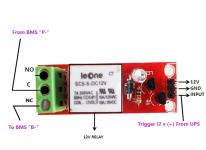
I have used two 12v packs, of 4 Serial connected 32700 3.2v LifePo4 6000mAh cells, connected in parallel (2P4S) to give theoretical capacity of 12Ah. I am using 14AWG wire for the battery connections. Each 12v pack is protected by 30amp 4S LifePo4 balanced BMS. This battery has been used to replace 7.5Ah SLA battery in a computer UPS. So far it is working very good and providing longer backup than SLA battery.
I have a few questions that I am still confused about and seeking input from everyone to figure out the answers.
1) Should I place a 30amp fuse on P+ port of the both BMS(s) or a 20amp fuse will be just fine?
2)Since the UPS is designed to work with 7.5Ah Sealed Lead Acid (SLA) battery, the charging voltage is set to 13.46volts(3.36v per cell) and can not be changed. I was doing some math, and figured, that at this voltage my LifePo4 cells will be 90% charged and therefore the Battery system will have actual capacity of 10.8Ah instead of the theoretical 12Ah that fully charged cells should have, since 90% of 12 is 10.8. Am I correct in my calculation?
3) When there is a long power outage and the battery gets fully drained, UPS does not automatically start recharging the batteries when the power resumes as the BMS isolates the batteries to prevent complete discharge. I have added a manual momentary switch between B- and P- port of each BMS to manually restart the charging process if the batteries are in over-discharge-protected mode due to a long power outage. How can I automate this process? I am thinking of using a 12v Relay, with High level trigger, and connecting B- of BMS to COMMON port of Relay and P- of BMS to (NC) Normally Closed Port of the Relay. Trigger pin will be connected to 12v charging voltage coming from the UPS. So when there is 12v Power in the system the relay will be in "triggered" state and "(NO)" port will be in "closed" state and "(NC)" Port will be in open state. This way I think B- and P- will always be in shorted state as long as there is no power in the system as soon as there is 12v power in the system P- and B- will get disconnected. Will this setup work to automate recharge reset or can it damage the BMS?
Thanks in advance for your time.
Parts Used:
HX-4S-F30A (LifePo4 Balanced BMS/Blue PCB version) x2
LifePo4 Cells, 32700, 6000mAh, 3C, x8
14 AWG wire and XT-60 Connectors. x6 (3Male, 3Female)
Plastic Battrey case(150x98x94)mm
JST-XH 2 Pin connectors with wire x4 (2Male, 2Female)
Momentary push button switch x2
Here are some photographs:
Current Setup:
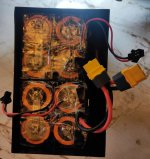
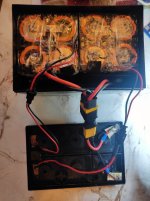
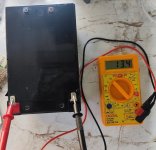
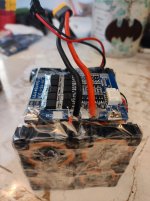
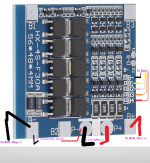
Proposed automation
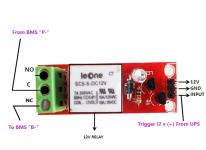