avada
1 mW
- Joined
- Sep 19, 2014
- Messages
- 18
Hello!
Everywhere efficiency is elaborated they always mention that electric motors have low efficiency at low revolutions or power. For example Tesla announced that they added a second motor to the model S which improved it's efficiency.
I was wondering what are the root causes of this apparently general inefficiency. Is it the inverters or other driver electronics? Or the motors themselves?
Here are two examples:
http://www.yasamotors.com/wp-content/uploads/2014/07/Datasheet-YASA-750_en-ID-15637.pdf
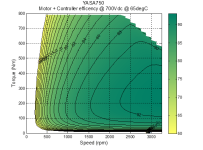
http://www.neweagle.net/support/wiki/docs/Datasheets/UQM/PP150.pdf
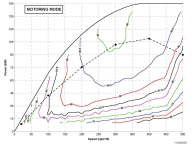
The YASA motor is less than 60% efficient under 250 RPM compared to 92%+ near its peak.
Everywhere efficiency is elaborated they always mention that electric motors have low efficiency at low revolutions or power. For example Tesla announced that they added a second motor to the model S which improved it's efficiency.
I was wondering what are the root causes of this apparently general inefficiency. Is it the inverters or other driver electronics? Or the motors themselves?
Here are two examples:
http://www.yasamotors.com/wp-content/uploads/2014/07/Datasheet-YASA-750_en-ID-15637.pdf
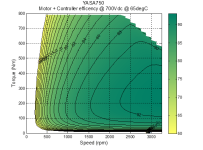
http://www.neweagle.net/support/wiki/docs/Datasheets/UQM/PP150.pdf
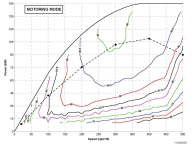
The YASA motor is less than 60% efficient under 250 RPM compared to 92%+ near its peak.