I am hoping that most of the people who have glued between the magnets of their RC motor will post what they have tried here, what worked, what didn't work. Super-glue gel, Devcon, JB-Weld? Pics would be great, too. Thanks in advance!
From reading at the DIY wind-generator website (otherpower.com), I already knew that adding epoxy between the magnets was common. I have been given the impression (unverified yet) that the purpose is to prevent side-to-side vibration of the magnets, which can lead to them coming loose (rather than the holding effect of a glue..). The energized stator tooth pushes the magnet on one side, and also pulls the magnet on its other side at the same time...then after some rotor movement, the forces the magnets feel are reversed.
It may also be valuable for the substance to have some 'give' so it doesn't crack. But what are the limits between too soft (flexible) and too hard (brittle) ? These motors also sometimes get pretty hot, some methods may have better hot characteristics that others.
Here are 3 pics from otherpower.com, and a pic of a stock factory-glue RC-motor from swbluto
From reading at the DIY wind-generator website (otherpower.com), I already knew that adding epoxy between the magnets was common. I have been given the impression (unverified yet) that the purpose is to prevent side-to-side vibration of the magnets, which can lead to them coming loose (rather than the holding effect of a glue..). The energized stator tooth pushes the magnet on one side, and also pulls the magnet on its other side at the same time...then after some rotor movement, the forces the magnets feel are reversed.
It may also be valuable for the substance to have some 'give' so it doesn't crack. But what are the limits between too soft (flexible) and too hard (brittle) ? These motors also sometimes get pretty hot, some methods may have better hot characteristics that others.
Here are 3 pics from otherpower.com, and a pic of a stock factory-glue RC-motor from swbluto
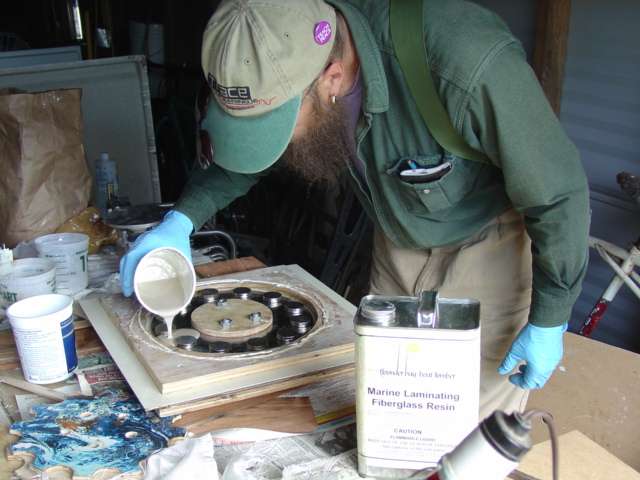
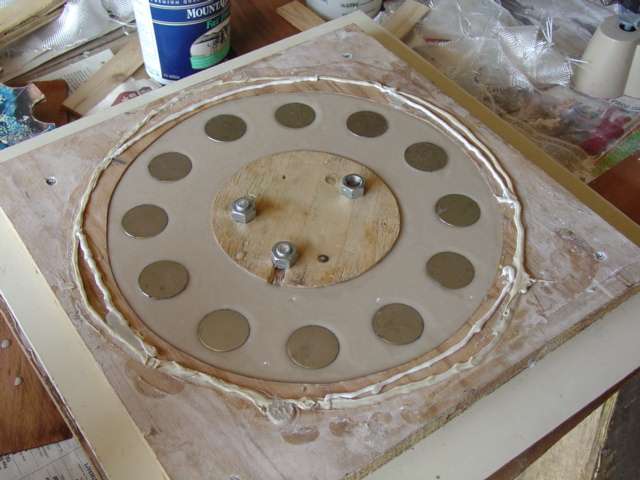