adrian_sm
1 MW
Okay, here is my submission for "Worlds Worst Dyno". :lol:
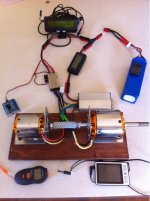
Mechanical Setup is:
- two angle brackets and a bit of scrap wood to mount the motors
- a small section of pressure hose and hose clamps to couple the motors
Electical Drive setup:
- left motor is the motor under test (C6364-230kv)
- right motor is the load (C8085-250kv)
- left controller is currently a Turnigy 85A ESC with a servo tester to control speed
- right controller is a Xiechang 6 fet, with regen capability, to supply the load
Measurement:
- no torque sensing
- RPM sensing via oscilloscope across two phase wire
- Cycle analyst for one motor
- Watt Meter for the other (note: watt meter and CA current reading don't match )
- IR thermometer for motor temps
- LiPo buzzer to make sure I don't kill the batteries
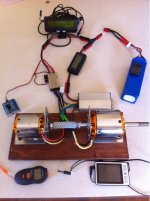
Mechanical Setup is:
- two angle brackets and a bit of scrap wood to mount the motors
- a small section of pressure hose and hose clamps to couple the motors
Electical Drive setup:
- left motor is the motor under test (C6364-230kv)
- right motor is the load (C8085-250kv)
- left controller is currently a Turnigy 85A ESC with a servo tester to control speed
- right controller is a Xiechang 6 fet, with regen capability, to supply the load
Measurement:
- no torque sensing
- RPM sensing via oscilloscope across two phase wire
- Cycle analyst for one motor
- Watt Meter for the other (note: watt meter and CA current reading don't match )
- IR thermometer for motor temps
- LiPo buzzer to make sure I don't kill the batteries