harrisonpatm
10 kW
- Joined
- Aug 8, 2022
- Messages
- 824
Alright, why not add another concurrent build to my project list? My EX500 is in good shape mechanically, but to finish it, it needs a motor, controller, and battery, all the expensive junk, and I don't have that budget. It's either going to wait for a great deal for those parts, or I'm going to steal the parts from my current e-moto, next year.
Until then, I had mentioned in my EX500 thread that I got lucky and found some awesome-looking motors at the scrapyard for $6USD each. It turns out they were rated for about 2500w @48v, not enough for a full-sized motorcycle, but plenty for a little scooter or moped that doesn't need to go fast. So I started keeping an eye out on my local classifieds. In the meantime, I found a dirt-cheap 3000w BLDC controller from AliExpress for bench testing, and I confirmed that the first two motors I tried worked great, both at 48 and 72v. Not bad for a scrapyard find.
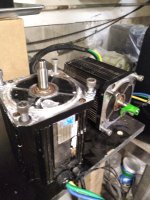
Then I got lucky again and found a suitable moped on my locals for $50, another steal. Sorry I don't have a picture of what I got before I started taking it apart (i was exciting and wanting to get into it right away), but here's someone else's photo of the same model.
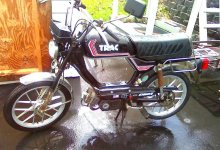
Weighs less than 110 pounds, so I think 2500-3000w will do the trick for 35ish mph. So, $50 for the bike, $6 for the motor, and $45 shipped for the controller (I know it's aliexpress garbage and isn't going to last, I can always upgrade later, and it works for bench testing at least). Now I just need to keep an eye on BatteryHookup for a good deal on cells to build a (relatively) small battery. There's a couple options on there now that look good, but I'll probably keep checking for a week or two in case something better comes up. I want to overvolt the motor to 72v, because then I can use the same direct-DC-from-solar charging that I have already setup for my current ride. So, assuming 3000w max output limited by both the motor and the controller, 72V nominal, I'll be looking for a pack that only needs to output 45ish amps max. Call it 60 amps max to make it easy on the cells. That will also be nice in that it means the battery itself won't be heavy, so won't add bike weight, and I can make it removable. That way, in the winter months I can use this as an occasional short commuter or errand runner, by charging the battery indoors. My style is rather cramped by not having my e-moto available 3-4 months a year.
So, mid drive, which is something I've never done from scratch before. Good learning experience, and I'll certainly use this build to make a ton of mistakes and do it the wrong way first, so I can learn. I got some good guidance on my other post, and with that I was able to find a company online that should be able to cut sprockets customs. If we assume 5000 max RPM at the shaft (which I'm not totally sure about, because it didn't come with a spec sheet), and 20-inch wheels, to get to 40MPH I need a 7:1 ratio. So I got a type B hub sprocket on order, 14T based on the advice to not go lower that 14 on the motor shaft, and I have two inquires out to see if someone can cut me a 98T rear sprocket that will fit.
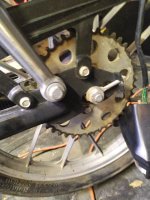
In the meantime, I used my CAD skills (cardboard-aided design) to start working on a motor mount. It's gonna get in the way of my right foot, so I might have to make new footrests, but it's not awful. Plus I basically have the motor sort of resting on the peg mounting bars themselves, meaning the face-type mount that I'll have to make for it won't have to carry the whole 20 pounds of motor against gravity. That's the downside of using a generic, non-specific-to-vehicle motor in the project, but I can't beat the price.
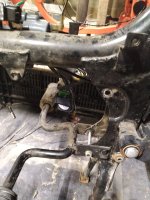
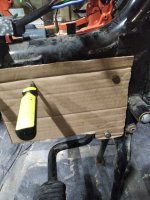
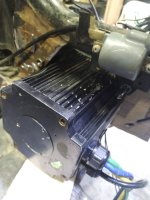
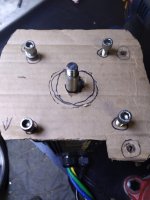
Also I have varnish leftover from detailing my QS273, so might as well get the interior of the motor water resistant. I was very surprised, as dinged up as the exterior of all the motors was, the interior was practically spotless. Couldn't hurt to varnish though.
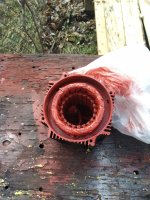
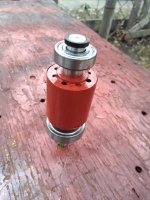
Next up is taking my cardboard stencil and drawing a draft of the motor mount for 3d printing, so I can check the fit. Then I'll cut it out of aluminum: also from the scrapyard I got offcut sheets for a couple bucks each, in 6mm, 8mm, and 11mm thicknesses. The 8mil seems strong enough to me, but I can always go up to the 11mil if I think it won't cut it.
One question I have: what tires are these, for replacement?
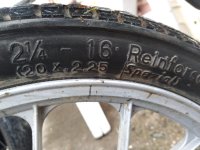
The rim is 16in. Can someone suggest what I can get to replace them? They're in bad shape. Tube or tubeless would be fine, I don't have enough experience to know just from looking at the rims whether they'll take tubeless.
I'll post again after I cut a motor mount from a 3d-printed stencil, because if that works out alright, I can start getting the rest of my components together.
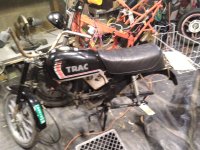
Until then, I had mentioned in my EX500 thread that I got lucky and found some awesome-looking motors at the scrapyard for $6USD each. It turns out they were rated for about 2500w @48v, not enough for a full-sized motorcycle, but plenty for a little scooter or moped that doesn't need to go fast. So I started keeping an eye out on my local classifieds. In the meantime, I found a dirt-cheap 3000w BLDC controller from AliExpress for bench testing, and I confirmed that the first two motors I tried worked great, both at 48 and 72v. Not bad for a scrapyard find.
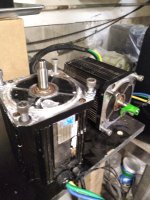
Then I got lucky again and found a suitable moped on my locals for $50, another steal. Sorry I don't have a picture of what I got before I started taking it apart (i was exciting and wanting to get into it right away), but here's someone else's photo of the same model.
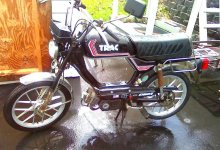
Weighs less than 110 pounds, so I think 2500-3000w will do the trick for 35ish mph. So, $50 for the bike, $6 for the motor, and $45 shipped for the controller (I know it's aliexpress garbage and isn't going to last, I can always upgrade later, and it works for bench testing at least). Now I just need to keep an eye on BatteryHookup for a good deal on cells to build a (relatively) small battery. There's a couple options on there now that look good, but I'll probably keep checking for a week or two in case something better comes up. I want to overvolt the motor to 72v, because then I can use the same direct-DC-from-solar charging that I have already setup for my current ride. So, assuming 3000w max output limited by both the motor and the controller, 72V nominal, I'll be looking for a pack that only needs to output 45ish amps max. Call it 60 amps max to make it easy on the cells. That will also be nice in that it means the battery itself won't be heavy, so won't add bike weight, and I can make it removable. That way, in the winter months I can use this as an occasional short commuter or errand runner, by charging the battery indoors. My style is rather cramped by not having my e-moto available 3-4 months a year.
So, mid drive, which is something I've never done from scratch before. Good learning experience, and I'll certainly use this build to make a ton of mistakes and do it the wrong way first, so I can learn. I got some good guidance on my other post, and with that I was able to find a company online that should be able to cut sprockets customs. If we assume 5000 max RPM at the shaft (which I'm not totally sure about, because it didn't come with a spec sheet), and 20-inch wheels, to get to 40MPH I need a 7:1 ratio. So I got a type B hub sprocket on order, 14T based on the advice to not go lower that 14 on the motor shaft, and I have two inquires out to see if someone can cut me a 98T rear sprocket that will fit.
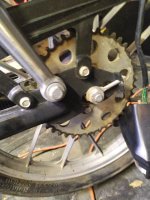
In the meantime, I used my CAD skills (cardboard-aided design) to start working on a motor mount. It's gonna get in the way of my right foot, so I might have to make new footrests, but it's not awful. Plus I basically have the motor sort of resting on the peg mounting bars themselves, meaning the face-type mount that I'll have to make for it won't have to carry the whole 20 pounds of motor against gravity. That's the downside of using a generic, non-specific-to-vehicle motor in the project, but I can't beat the price.
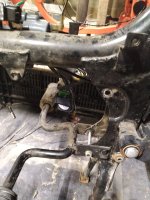
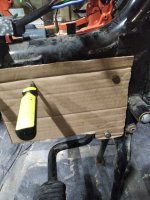
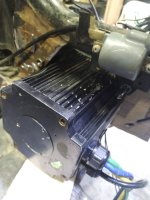
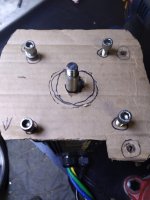
Also I have varnish leftover from detailing my QS273, so might as well get the interior of the motor water resistant. I was very surprised, as dinged up as the exterior of all the motors was, the interior was practically spotless. Couldn't hurt to varnish though.
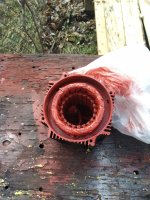
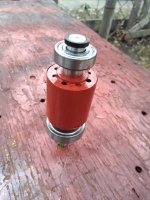
Next up is taking my cardboard stencil and drawing a draft of the motor mount for 3d printing, so I can check the fit. Then I'll cut it out of aluminum: also from the scrapyard I got offcut sheets for a couple bucks each, in 6mm, 8mm, and 11mm thicknesses. The 8mil seems strong enough to me, but I can always go up to the 11mil if I think it won't cut it.
One question I have: what tires are these, for replacement?
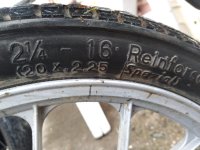
The rim is 16in. Can someone suggest what I can get to replace them? They're in bad shape. Tube or tubeless would be fine, I don't have enough experience to know just from looking at the rims whether they'll take tubeless.
I'll post again after I cut a motor mount from a 3d-printed stencil, because if that works out alright, I can start getting the rest of my components together.
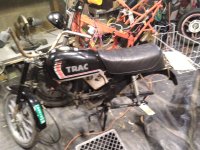