fatty said:
BobBob said:
That was one of my first questions "is the 4504 the right model of the 3 KV V3 MXUS"
The smartest guys here aren't going to do your homework for you. But
yes. Model the higher turn count versions to see why the 4T is incorrect.
Thanks.
I did model all of the motors and the 4T appears the best as far as I can tell
For example with an 87V batt and 70A controller the top speed on the flat is 45 for the 4T rather than 39 for the 5T
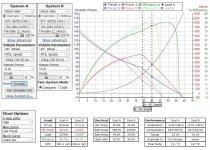
The 5T peaks at 30 MPH compared to 40 MPH for the 4T.
The 6T is even worse.
At high loads and slow speeds, the 5T is 1% more efficient but it's so marginal as to make no difference as far as I can see
https://ebikes.ca/tools/simulator.html?motor=MX4504&batt=cust_87_.0875_24&cont=cust_70_200_0.03_V&grade=0&axis=mph&throt=100&hp=0&mass=150&bopen=true&cont_b=cust_70_200_0.03_V&motor_b=MX4505&batt_b=cust_87_.0875_24&mass_b=150&hp_b=0&grade_b=0&autothrot_b=false&autothrot=false&throt_b=100&frame=mountain&frame_b=mountain&add=false&blue=Lbs
fatty said:
BobBob said:
Why should I be able to explain why the Grin Simulator is wrong and why shouldn't I need help and advice?
The motor is bought so the choice is for the battery, IE the quesion is "for a 4T what is the best controller and battery?"
The Simulator isn't wrong; you programmed it wrong. Why are the 4p and 6p packs supplying the same (impossible) battery current?
How could I program it wrong? It's a mathematical model of the parts
Grin programmed the simulation. I just selected the parts. Either the resulting answer is correct or it is not
How can the battery current be impossible? I didn't hack the software, so doesn't that mean you are saying that Grin got it wrong?
Confused as to what you mean but the sim seems ok to me
I'll go back and have a look at that in a sec
fatty said:
The motor choice is wrong, because your design flow was wrong. I'm not picking on you -- I suspect that you're smarter than most of the posters here, and can figure this out.
LMFAO: my motor choice is wrong, my (alleged) design flow was wrong and backwards and I picked a dangerous battery to bodge it, 150V is ludicrous, the concept is silly, PowerVelocity provide exotic hacked controllers, the values that the Grin simulator give are impossible and you're not picking on me.
You're helping me, I asked for people to throw rocks at my design. you're spending your time doing so. Thanks
fatty said:
Your design flow was backwards. You picked out a motor first and are trying to bodge a dangerous battery to fix it. You should have (iteratively) modeled your entire system before you bought the wrong motor.
Nope, I did try lots of iterations and lit on the PowerVelocity controller first, Motor second and battery to suit.
I do tend to think of the higher voltage as an advantage though and am debating that with myself. Still like it ATM
fatty said:
The proper design flow is to define your constraints and goals first. This isn't rocket surgery -- as I've posted, performance ebikes coalesce around very common, almost singular solutions, because they make the most sense:
0) performance controllers max at 90V = 21s. This is already exceeding the safety envelope. This should be your max voltage, so you're not stuck with an exotic hacked controller from a single seller.
Right, so PowerVelocity in your opinion is an "exotic hacked controller". That seems a bit harsh, they seem fairly popular here.
You're worried that I won't be able to change suppliers, that makes sense but I could go for a lower performance controller later if this fails
I was originally planning to use the 70A 100V 7Kw version but am tending toward its big brother.
I can always break down the battery and rebuild if I really need to or fix the controller.
fatty said:
1) define your desired no-load speed and work backwards to kV, as described above. You want kV to be as low as possible. Why? What is the relationship between kV and kT?
I'm not even sure I have a desired top speed though around 40 is probably sensible
The power curve, torque accross the speed range under a wide range of loads and battery charge states seems more important.
I therefore tried lots of combinations and the PowerVelocity seemed to win due to higher available voltage and current.
I should try your method but if it tells me I can do 146 Mph I'm not going to believe it
fatty said:
2) size the controller current for desired torque. You want to have sufficient torque to be control-limited (lifting the front) for as much of the speed range as possible, without burning up the motor. 8kW will burn up a MXUS 3k. How can you get more torque from the same current? See hint above.
More voltage
fatty said:
3) size your battery current to meet controller current.
Yup did that
fatty said:
Learn from the motor mistake -- don't let it define the rest of your build. You'll spend much more on crazy battery and charger than you would redesigning correctly.
Battery can be rebuilt and charger is $130 and adjustable for different voltages if I can be botherd.
BMS might get binned but it's $50 so who cares, Battery may have gone up in flames by then anyway, motor will be toast etc
I think you are suggesting a low Kv, High Kt lower voltage system.
With the battery and controller I'm planning I could always turn the power down