Now that it has a smart-ass moniker better than the last bike, lets see about getting the design together.
It's based partly on Lee's most recent trike from The Packrat Workshop, after some conversations with him about what might be best adaptable to the parts I have on hand. So it likely won't have suspension, at least in front, for this version.
It'll be a single-tube main frame, probably made from a 2.5" fencepost I have.
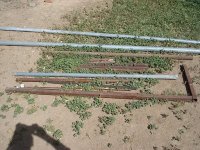
That galvanized post with the mangled right end, within the L of square tubing, is the one.
One possible way it could be configured, but probably won't be:
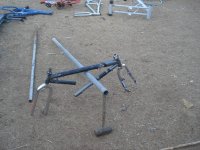
Depending on length of things I might use this instead:
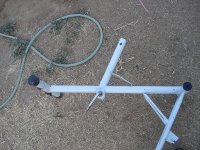
with the load-wheel tubing cut off, at the far right, and most of the mast up top cut off.
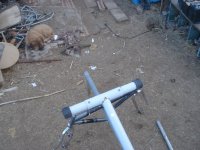
That will go back to a bottom bracket pivot point for any rear suspension. I will probably not have a spring/shock for it by the time I need to ride it, so it will end up with just a solid tube bolted in place of whatever shock I would have used. I still want to build the pivot into it now, though, so it can be much more easily suspended later.
The rear triangle will be a modified one off of a 24 bike, probably off the old Roadmaster frame I originally started to use for CrazyBike2's rear end, but swapped out for the much lighter and slightly longer Schwinn frame instead. The main modification will be to make it vertically shorter, by cutting the seat tube down and bending the seatstays to meet it at the much shorter location. Rather like the back end of CB2 already is. This is mainly so that the entire triangle will be "below the deck" of the cargo pods that will run alongside it. Probably a 24" wheel, too, since the best slick tire I have is for that size.
Those pods will be the pods off CB2, mounted on a frame very like the one CB2 has, except that it will all be hanging from the back of the main tube, not connected to the rear triangle. Thus all the cargo pods will be suspended with the rest of the bike frame.
The seat will need to be built from scratch, and will be a lot like the one on CB2, but more form-fitting, if i can bend the tubing this time. I'll be again using tubing off an old bedside potty chair, same as on CB2, since it is small-diameter and extremely strong. The webbing will probably be the same green stuff I used on CB2's seat, simply because I have more of it and it's lasted just fine for more than half a year so far. It'll be tensioned using the same parachute cord lacing I used for CB2.
Like Lee's trike, I'll use tank-style steering, as it's mechanically simple and easy to build. It also doesn't take much space for it's movements, and won't get in the way of getting up and out of it like handlebars would, nor will it get in the way of my leg strokes for pedalling while turning, as can occasionally happen with CB2's bars at extreme turns with my kneecaps.
Pedals will be over the main tube and out beyond the front wheel axle, though probably not beyond the whole front wheel. Not completely sure until I finish the 3D sketches of it how the alignment works out.
The front end is where things get different. Because I am going to be forced onto sidewalks sometimes by either traffic or ignorant law-enforcement personnel, I can't make it wider than the sidewalk. Since a number of bike paths have protection poles across them to prevent cars from driving onto them, and those are generally spaced wide enough for wheelchairs, the front end will be no wider than a wheelchair.
Some of the parts I am considering for it:
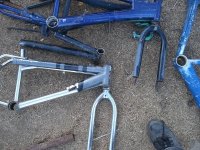
Each front wheel will have it's own non-hub motor, most likely a wheelchair motor with it's reduction gearbox, with a V-pulley on the output shaft and another V-pulley on the wheel hub. The gearboxes have a tubular indentation in the top of the mounting plate, which happens to be the same as the steering tubes on a couple of the 26" forks I have.
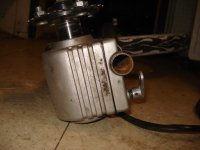
So one idea is to clamp the motor to the steering tube, and setup the pulley on the hub and shaft so that they'll line up just outside the tire's sidewall.
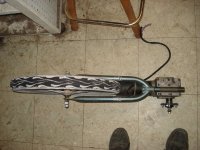
The motor would then stick out to the rear of the wheel, parallel to the ground.
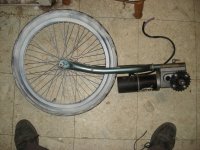
It is just one mounting idea, but one that happens to involve the least modification to the fork to do it. There are some serious disadvantages to it, too.
Then another steering tube is welded to the inside-leg of the fork down nearer to the dropout on the side opposite the pulley, at an angle that gives me whatever camber/caster turns out best for this thing (I still have to work out enough of it to then be able to figure out how to calculate that out).
That steering tube will then go into the headstock off a Razor kick scooter. Those things are meant to fold, so a few inches away from the headtube is a pivot point in the square tubing. That headstock is then bolted thru it's original folding pivot point to the end of a square tube welded at a forward/sideways angle out from the main tube, like a very wide Y. Another pivot point is welded to the headtube above that, which will go at first just to another tube welded to a vertical mast on the main tube.
View attachment 1
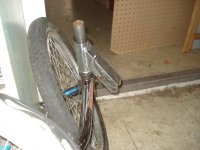
Later, part of that horizontal tube will probably be replaced with a suspension of some sort, which is why I want the pivot point there now. If I don't end up putting suspension there, I would like to still end up making some sort of four-bar-linkage so I can make this a tilting trike, to improve stability in tighter turns at speed.
As heavy as each wheel will be, that means that the front end should be fairly stable in turns anyway.
To add to that stability, the SLA batteries (probably 4x 12V 17Ah) will be slung underneath the front end and the seat. That should help keep the weight to 1/3 on each wheel of the trike, but I will need to actually measure everything once I get it mostly designed, to make proper placements for things.
There will be cargo pods up front, too; I don't know what their shape is yet as I am not certain what spacing I will have up there.
Behind the seat on it's rear brace will be a vertical post sticking up to windshield level on the average car. A box will be mounted atop that with front, rear, and side lighting appropriate to the direction it faces. There will also be separate lights at the outermost corners of the cargo pods in the rear and the forks up front, for markers, signals, and emergency flashers. I don't yet have a set of lights to put on here, so I will probably be custom-building them. The lenses will likely be made from various bike reflectors glued together, with LED (for any flashing lights) and CFL (for any steady lights) lighting behind them.
Brakes will probably be disk brakes, donated by the very generous AussieJester. I have to fabricate adapters for them, and thus will probably be using some 48-spoke rear hubs I have on some 48-spoke 20-inch rims. The rear hubs are freewheel threaded on the right, but I will flip them over to put that on the left side, and make disc adapters out of something already threaded to that. I might be able to use the bottom bracket tube from an old cottered-crank frame I have, if the threads are the same pitch and the correct handedness. Then weld the tube to plates, face them on the lathe, and drill boltholes to match the disks. Basically they would do the same thing as these:
http://www.choppersus.com/store/product/308/Disc-Brake-Rotor-Converter/
If I can come up with the cash, I'd rather order a couple of these from Choppers US, as they'd also make mounting the pulleys much easier, too, since they're made for dual-disk, one on each side:
http://www.choppersus.com/store/product/874/Front-Hub---Dual-Disc-CP/
It would also mean I could have both discs on the inside or both on the outside of the wheels, rather than both on the left side, which results in the left wheel's brake on the outside and the right wheel's on the inside. I don't imagine it would make a difference in performance to be the latter way, but it might make fabricating the forks a little harder since they won't be identical nor mirror images.
The catch is those dual-disk hubs are 36-hole, and I really want to use the 48-spoke wheels to help more with the side-loads and weight on this thing.
That's it for the moment, until I can get some pics of parts I have and some 3D sketches done up. Or at least some pencil versions scanned in.
Now, hopefully this little guy won't get shot in the head when I do the trench run.
