It would be easier if they just used old-fashioned screws instead of using stupid ideas from smartphone industry.
I believe CYC is using threaded fasteners in some places - a single screw holds the controller into the motor casing, as well as four holding the controller and motor core together (with a paper or rubber gasket in between). For the secondary gear, it appears there's a threaded pin wrench ring holding the assembly together, similar to the one holding the chainring assembly in place.
CYC might also be using liquid gasket(s), similar to what's used in other industries (automotive and marine engines, for example), that do a better job on complex and/or narrow-edged component joints.
I wish I could attach the leaked FCC Bluetooth certification PDFs that have internal and external photos, so you could judge for yourself how the motor is assembled. I can't remember where I found them - a forum post somewhere ...
Here are a few photos I snipped from the PDFs, that might help clarify things - the first is of the right side of the motor, showing the outer secondary gear pin ring, as well as the inner chainring pin ring (without the chainring). Below is the single controller screw hole:

The next is with the chainring pin ring removed (and shown upper-right (reversed)), as well as some of the mechanicals within. Notice that there's an inner bearing (or clutch?) that's removable without unthreading the outer pin ring:

Seeing this level of disassembly makes me hope that at least some D.I.Y. regreasing is not out of the question. Here's a side view of the controller/motor core junction, showing some form of gasket material:
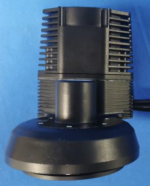
Here's one more photo, showing more of the innards and screw locations:

The controller is, I think, normally potted but isn't in this case - possibly related to the certification process. Within the secondary gear casing (shown on the left) there appears to be a sealed outer bearing that probably doesn't require greasing. Nothing magical, and to me vaguely similar to the Bafang BBS series - just more compact and refined.
One component I've not been able to decypher is the primary gear (equivalent to Bafang's clutched nylon gear). I see the pinion shaft (shown lower left) and maybe the outer ring (shown upper center), but where's the clutch? Maybe the one-way clutch requirement is being done by that other, bigger (sprag?) bearing in the second photo.
I may take a crack at disassembling my second motor before it's installed - for curiosity's sake.
"Because its glued shut" may be a misleading choice of words from the pedelecs poster, and not the impression I get from the above photos, but I have yet to personally disassemble one of these motors.