Grinhill
10 kW
I came up with an improvement for the belt-slip issue a few weeks back, and it's working well (yes, I know it's a bit "ghetto"
).
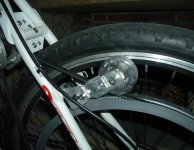
I have seen power up to 3200W on one occasion! It's an old skate wheel (actually came from a suitcase) and the bearings are rubbish, but still works. It's fixed, no spring.
Some further info on the belt - I have observed a clicking noise when running the motor at low revs, which turns out to be twice per revolution. This appears to be the source of my slipping problem as well - the large pulley, not the small one! Because of the pulley design, not using a proper HTD profile for the teeth, and having two quarters of the pulley smooth, the following happens:
There must be a slight mismatch in the alignment of the belt teeth to the pulley teeth, for whatever reason. After the smooth section, the belt rides on the ridges for a while instead of seating down to engage the pulley. This will cause a momentary increase in tension due to the increased diameter. The belt then engages with a snapping noise, slipping back to where it should be for a while until the next section with no teeth.
This means that it is my large pulley slipping, not the small one. And it's worse at high speed because the belt is travelling at higher speed. It also means that there are some fundamental design issues with the pulley. One possible solution would be to use a longer belt to increase wrap around the large pulley by using an idler. This will keep the belt engaged with the pulley for almost the whole way around, not giving the opportunity for a mismatch to occur.

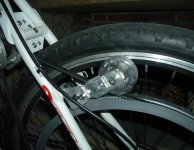
I have seen power up to 3200W on one occasion! It's an old skate wheel (actually came from a suitcase) and the bearings are rubbish, but still works. It's fixed, no spring.
Some further info on the belt - I have observed a clicking noise when running the motor at low revs, which turns out to be twice per revolution. This appears to be the source of my slipping problem as well - the large pulley, not the small one! Because of the pulley design, not using a proper HTD profile for the teeth, and having two quarters of the pulley smooth, the following happens:
There must be a slight mismatch in the alignment of the belt teeth to the pulley teeth, for whatever reason. After the smooth section, the belt rides on the ridges for a while instead of seating down to engage the pulley. This will cause a momentary increase in tension due to the increased diameter. The belt then engages with a snapping noise, slipping back to where it should be for a while until the next section with no teeth.
This means that it is my large pulley slipping, not the small one. And it's worse at high speed because the belt is travelling at higher speed. It also means that there are some fundamental design issues with the pulley. One possible solution would be to use a longer belt to increase wrap around the large pulley by using an idler. This will keep the belt engaged with the pulley for almost the whole way around, not giving the opportunity for a mismatch to occur.