Buk___ said:
If you put two identical motors on a bike, presumably, you gain in torque; thus climbing and/or load carrying ability, but you are stuck with the same top speed as with a single motor.
Assuming identical controllers, wheels, tires, and throttles that's pretty much true. There is a small top speed increase but generally not a lot on the flat. Clearly when the bike is under load (e.g. hill climbing) the terminal speed will be improved because you are not voltage and Kv limited. (Kv reflects the 'wind' or unloaded rpm of the motor)
Buk___ said:
What happens if you combine two differently wound motors, say a "201 wind" and a "328 wind"?
Ie. Does the slower motor hold the faster motor back; or does the faster motor carry the slower motor up with it?
You will generally compromise performance and efficiency under most if not all conditions. You do not want to mix motors with different Kv in the "everything equal" conditions set out above.
There are two critical factors in play here
- While the motor is controller limited (i.e. under load like accelerating or climbing hills) the Kv or wind of the motor doesn't matter - the 201rpm and 328rpm versions of the same motor will perform virtually identically. (This is always a major point of argument, but it's true. Read this for the why: http://www.ebikes.ca/learn/hub-motors.html)
- While the motor is not controller limited, the Kv serves primarily to limit the top speed. Efficiency, etc are not effected.
So the short form is that for hill climbing the two different rpm versions operate the same, but when running on the flat, the lower rpm version will just go slower with no particular advantage. There are some lesser effects from the controller and battery, but from the motor perspective picking the low rpm wind just means you go slower.
So - re-phrasing your question: "What happens if I mix two motors that perform the same climbing hills, but one is a dog on the flat?". The answer: you throw away speed and introduce control problems because of the different performance ranges. Generally a Bad Plan (see battery current remarks below).
I strongly recommend you play with the
ebikes.ca simulator which got a recent upgrade to allow it to do 2WD simulations and adjust the Kv to be able to simulate similar motors even if one isn't in the database.
Here's some sample plots to show you what's up. Here I selected the Q100 328r from the database for motor A and adjusted the Kv down by 0.613 for motor B to simulate a 201rpm version. If we look at the 328+201 combination on the flat we get a terminal speed of 27.3mph @ 21.3A (sum the A+B "Battery Amps" values):
(I didn't bother to resize the images - just hold SHIFT when you click so they will open in separate windows for comparison...)
View attachment 5
The same scenario with two 328rpm motors gives a terminal speed of 30.8mph @ 28A
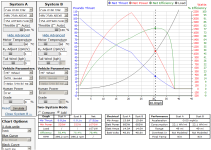
So what about that huge current increase for the dual 328rpm case?
Well - that comes from the higher speed. If we back off on the throttle to 86% for the dual 328rpm case we get the same 27.3mph of the mixed motor build but at about 20A (i.e. same speed, less power)... hmmmm.
So, the whole hill-climbing thing is the next question.
Doing the same runs on an 8% grade we see:
Mixed motor on 8% grade:
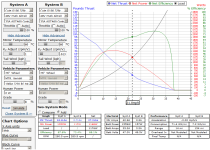
Same 328rpm motor on 8% grade:
View attachment 1
And finally same 328rpm motor on 8% grade with throttle adjusted to 81% to match lower speed of mixed motor case:

Again the dual high rpm motor case outperforms the mixed motor case by using less power to achieve the same speed on the hill climb at only 81% throttle - and there's still more speed to be had if you want to open it up.... hmmmm again.
So one big difference here is in the total amps each system will draw at max speed - the matched motor case consistently out-performs the mixed motor case but the particular high rpm wind that was chosen will draw more current to achieve the higher possible speeds. Choosing matched motors with a lower rpm wind will show similar comparative performance but with a reduced top speed and at lower current. The second big difference in motor temperatures. The thermal performance for this particular motor isn't modeled in the simulator, but if you perform similar experiments with something like a 9C 2705 + 2707 you can see the dramatic heat differences that can crop up in the mixed motor cases because of the unequal load sharing. These problems are very much mitigated in the matched-motor case because of equal load sharing under all conditions.
Like a single motor bike, you need to look at the whole system to make a balanced selection of components. Best to start with the battery and work back to the motors that it can support. The simulator will help clear up a lot of questions. For instance, in the example above, if your battery can't support the 45A of the matched-motor 8%grade case, then those motors may not be the best choice if you need to do that more than occasionally. That said, they are not a Bad Choice, since you can crank down the controller current limiting and just force things into an extended current-limited region where that wind will perform the same as any other wind...
There are many schools of thought for controls and controllers...
If you stick with the "everything equal" strategy" (same tires/wheels/controllers) then you can use inexpensive trap or sine controllers and get perfectly matched motor performance in all conditions without any extra electronics or fuss. Unless you are dirt riding or using really powerful motors where the front wheel might spin out, a 50/50 power split works well (I have 14000mi on such a rig - no washouts, no spinouts, no handling issues). There are lots of options, but I prefer a single throttle for easy riding and a CA3 with a single battery and external shunt so I have unified monitoring and can have PAS that runs both motors optimally. There are few circumstances where running a single motor is more efficient than running both even for easy cruising - so there's really no need to go after complicated controls. I set my bike up so I could run FWD/RWD/2WD with various current limits, etc and in the end the simulator was pretty much spot on and now I just ride 2WD, but I have a bunch of pretty controls that seldom get used....
(Thanks go out to Justin for adding the 2WD and Kv features to the simulator - makes this stuff so much easier....

)