TheWelshGuy
100 µW
Hi Folks, new member here...
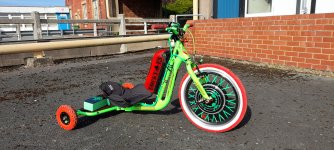
Recently finished building an E-Drift trike but on 3rd good ride out I've thrown some error codes and just wanted some advice. Already done some research but I've not got any of the common symptoms others are mentioning.
Worth noting that I'm a relative novice when it comes to electrics too so please bear with me.
Specs are:
Golden Motor pro 901 hub 1000w (will take up to 1700w apparently)
48v 20.4ah battery
1500w dcmoto controller
Sw900 display
Thumb throttle.
When I first got it put together it was throwing error 8 (throttle) connector was loose on fem side so took to bits, re shaped everything so it goes together nice and snug - problem sorted. Been perfect since.
Yesterday after a bit of a ride on the drift wheels (lots of vibration from them) it suddenly stopped responding and threw error 8, figured no biggie, pulled the lid off the enclosure and fiddled about with connector and now my error code seems to alternate between 8 and 9.
Seems like most error 9's online act like a shorted phase wire and prevent the hub turning freely or causing resistance... I've got none of that, hub turns freely, heard no pops, nothing got hot etc etc...
Obvs error 9 is listed as communication error between controller and display, could that be triggered by an error 8 problem? - I.e- loss of signal from throttle etc?
Just seems strange that its alternating between 2 codes.
It seems to favour 9 at the minute, but if I fiddle with throttle connector it switches to 8, fiddle again, back to 9 etc etc.
At a bit of a loss where to go from here in terms if testing process, or even how to test to be truthful.
I do have access to a multi meter although I wouldn't know how to use it on an e bike controller.
Thanks in advance.
Tom
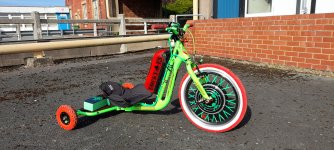
Recently finished building an E-Drift trike but on 3rd good ride out I've thrown some error codes and just wanted some advice. Already done some research but I've not got any of the common symptoms others are mentioning.
Worth noting that I'm a relative novice when it comes to electrics too so please bear with me.
Specs are:
Golden Motor pro 901 hub 1000w (will take up to 1700w apparently)
48v 20.4ah battery
1500w dcmoto controller
Sw900 display
Thumb throttle.
When I first got it put together it was throwing error 8 (throttle) connector was loose on fem side so took to bits, re shaped everything so it goes together nice and snug - problem sorted. Been perfect since.
Yesterday after a bit of a ride on the drift wheels (lots of vibration from them) it suddenly stopped responding and threw error 8, figured no biggie, pulled the lid off the enclosure and fiddled about with connector and now my error code seems to alternate between 8 and 9.
Seems like most error 9's online act like a shorted phase wire and prevent the hub turning freely or causing resistance... I've got none of that, hub turns freely, heard no pops, nothing got hot etc etc...
Obvs error 9 is listed as communication error between controller and display, could that be triggered by an error 8 problem? - I.e- loss of signal from throttle etc?
Just seems strange that its alternating between 2 codes.
It seems to favour 9 at the minute, but if I fiddle with throttle connector it switches to 8, fiddle again, back to 9 etc etc.
At a bit of a loss where to go from here in terms if testing process, or even how to test to be truthful.
I do have access to a multi meter although I wouldn't know how to use it on an e bike controller.
Thanks in advance.
Tom