My name is Bjorn and I am new to forums.
I have been searching this forum for the last 3 months for similar projects and solutions.
I have already done two electric bike projects.
They were not documented and both had issues.
1) Test Build under $300
Santa Cruz Bullit rear triangle and 2009 fox van r (old DH bike)
Homemade custom front triangle (low carbon steel)
600 watt motor (got for $30)
Navatis 100A 24/36V Controller
Magura twist throttle
2X Lead acid batteries 12V / 12A (slightly used but free)
2X 5A chargers
Twist key kill switch
Problems: as there was little money I only used motor power (no pedaling), there wasn't enough power and since it was a test it was never meant to stay together forever.
Lasted: 10 days & about 20 charges before taking apart.
2) 1969? Kawasaki RT90 conversion
Perm 132 motor ($1000)
16X lithium iron phosphate 3.2V / 40A (slightly used at $1600)
Alltrax controller 24-48V / 300A
Battery balancer (BMS without running power through 40A limiter)
12A charger (5 hour charge time off 110V outlet)
Parts from project #1
about 1 year of researching and 1 year of building slowly during school
Problems: the battery pack was funded by my Dad. My Dad was anxious to buy batteries to start the project (he didn't understand the ordering of assembly: motor install then batteries). We bought used cells from an electric trials rider (claimed only discharged a couple of times). These batteries have a max continuous discharge of 120A or 3C, and the guy had discharged them at 300A (7.5C). I told my Dad that the cells where wasted, but he did not listen.
A full charge from a cell voltage of 2.7V to about 3.4V with a balancer only took 1 hour and a couple of minutes. I charged and discharged the batteries checking the cell voltages periodically; which means that the pack was not out of balance. I looked up charging algorithms for the charger (emailed company) and found out initially the charger charges at between 11 and 12 amperes.
This means that the battery pack which was supposed to be about 2.05 kW was only about 0.614 kW.
Due to the battery pack limits the peak current was limited to 120A… 6.1kW
Range was only 12 miles riding half on and half off-road.
I ran out of enthusiasm and money for the project and I stripped the electronics off to save for a future project.
Lasted: 2 weeks and about 30 charges
New Project (will be worked on over the next year and documented on this thread):
I am now ready for a no bars hold build:
Mix between MTB and motorcycle parts
try to keep it under 50 kg
7.5 kW < Continuos Power < 15 kW
15 kW < Peak Power < 25kW
I want a peak power over 20 hp.
Brushless (probably going to add delta to wey switching capabilities later)
Geometry similar to a size large DH bike (Add adjustable chain stay length rear mounts).
I want to run hall sensors to allow for smoother low end operation.
Burtie makes a variable timer and optical sensor board that I am vary set on buying.
I have about $1000 currently for the first parts buy.
I would like to get recommendations on a controller that can power one of these motors past the 100,000 erpm limitations of the kelly controller.
To start the project I am going to need a motor:
Could someone help me with a colossus out-runner or something that is a in-runner in a similar power range (a in-runner is preferred due to it being easier to seal).
Design:
4" X 6" 6061 tubing 1/4" wall machined to make the head tube, shock mount and pivot locations perfect.
It acts as its own frame jig.
The motors (may be C80100-B motors or something similar) and controller will be mounted in the tubing and a fan near the head tube will keep them cool.
Pivot will have a tube with bearings that will keep chain tension constant due to zero chain growth.
Pictures:

View attachment 1
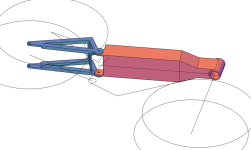
PDF:
View attachment bike project front.pdf
View attachment bike project left back.pdf
View attachment bike project right bottom.pdf
I have been searching this forum for the last 3 months for similar projects and solutions.
I have already done two electric bike projects.
They were not documented and both had issues.
1) Test Build under $300
Santa Cruz Bullit rear triangle and 2009 fox van r (old DH bike)
Homemade custom front triangle (low carbon steel)
600 watt motor (got for $30)
Navatis 100A 24/36V Controller
Magura twist throttle
2X Lead acid batteries 12V / 12A (slightly used but free)
2X 5A chargers
Twist key kill switch
Problems: as there was little money I only used motor power (no pedaling), there wasn't enough power and since it was a test it was never meant to stay together forever.
Lasted: 10 days & about 20 charges before taking apart.
2) 1969? Kawasaki RT90 conversion
Perm 132 motor ($1000)
16X lithium iron phosphate 3.2V / 40A (slightly used at $1600)
Alltrax controller 24-48V / 300A
Battery balancer (BMS without running power through 40A limiter)
12A charger (5 hour charge time off 110V outlet)
Parts from project #1
about 1 year of researching and 1 year of building slowly during school
Problems: the battery pack was funded by my Dad. My Dad was anxious to buy batteries to start the project (he didn't understand the ordering of assembly: motor install then batteries). We bought used cells from an electric trials rider (claimed only discharged a couple of times). These batteries have a max continuous discharge of 120A or 3C, and the guy had discharged them at 300A (7.5C). I told my Dad that the cells where wasted, but he did not listen.
A full charge from a cell voltage of 2.7V to about 3.4V with a balancer only took 1 hour and a couple of minutes. I charged and discharged the batteries checking the cell voltages periodically; which means that the pack was not out of balance. I looked up charging algorithms for the charger (emailed company) and found out initially the charger charges at between 11 and 12 amperes.
This means that the battery pack which was supposed to be about 2.05 kW was only about 0.614 kW.
Due to the battery pack limits the peak current was limited to 120A… 6.1kW
Range was only 12 miles riding half on and half off-road.
I ran out of enthusiasm and money for the project and I stripped the electronics off to save for a future project.
Lasted: 2 weeks and about 30 charges
New Project (will be worked on over the next year and documented on this thread):
I am now ready for a no bars hold build:
Mix between MTB and motorcycle parts
try to keep it under 50 kg
7.5 kW < Continuos Power < 15 kW
15 kW < Peak Power < 25kW
I want a peak power over 20 hp.
Brushless (probably going to add delta to wey switching capabilities later)
Geometry similar to a size large DH bike (Add adjustable chain stay length rear mounts).
I want to run hall sensors to allow for smoother low end operation.
Burtie makes a variable timer and optical sensor board that I am vary set on buying.
I have about $1000 currently for the first parts buy.
I would like to get recommendations on a controller that can power one of these motors past the 100,000 erpm limitations of the kelly controller.
To start the project I am going to need a motor:
Could someone help me with a colossus out-runner or something that is a in-runner in a similar power range (a in-runner is preferred due to it being easier to seal).
Design:
4" X 6" 6061 tubing 1/4" wall machined to make the head tube, shock mount and pivot locations perfect.
It acts as its own frame jig.
The motors (may be C80100-B motors or something similar) and controller will be mounted in the tubing and a fan near the head tube will keep them cool.
Pivot will have a tube with bearings that will keep chain tension constant due to zero chain growth.
Pictures:

View attachment 1
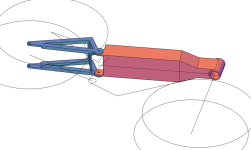
PDF:
View attachment bike project front.pdf
View attachment bike project left back.pdf
View attachment bike project right bottom.pdf