Okay, you're actually right, when it comes to most of the power band. Especially peak.
My knowledge was based on the 0.35mm version of the motor. If you're using the GMAC, then you're probably simulating the 0.27mm lam version. So, i was off when it comes to that factor too.
However, if we take an equivalent winding GMAC and Cromotor, you'll see that the big DD can make more torque in the mid-upper part of the powerband.. and this is totally expected, because a geared motor begins to lose power and efficiency to gearing and stator losses at that point..
Here's an equivalent winding ( kv adjusted, battery voltage drop & controller power isolated ) comparison..
https://www.ebikes.ca/tools/simulat..._tuck&axis=mph&blue=Lbs&wheel=26i&wheel_b=26i
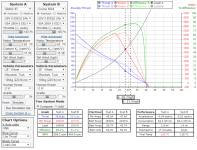
..i'd still want a DD for heat reasons and efficiency under cruising.. only because i have high speeds to go, long distances to cover, and very steep hills to climb.... but a modern MAC is very compelling, i get it
My knowledge was based on the 0.35mm version of the motor. If you're using the GMAC, then you're probably simulating the 0.27mm lam version. So, i was off when it comes to that factor too.
However, if we take an equivalent winding GMAC and Cromotor, you'll see that the big DD can make more torque in the mid-upper part of the powerband.. and this is totally expected, because a geared motor begins to lose power and efficiency to gearing and stator losses at that point..
Here's an equivalent winding ( kv adjusted, battery voltage drop & controller power isolated ) comparison..
https://www.ebikes.ca/tools/simulat..._tuck&axis=mph&blue=Lbs&wheel=26i&wheel_b=26i
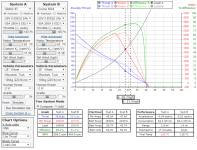
..i'd still want a DD for heat reasons and efficiency under cruising.. only because i have high speeds to go, long distances to cover, and very steep hills to climb.... but a modern MAC is very compelling, i get it