i have a question pertaining to axels of hub motors for ebikes. i have a typical generic 750w hub motor kit from amazon: ( https://www.amazon.com/ZeHuoGe-Electric-Brushless-Front-Delivery/dp/B07L88F7L2/ref=sr_1_13?crid=2EZL9RKK7VMJT&keywords=750w+motor+kit&qid=1671465207&sprefix=750w+motor+kit%2Caps%2C75&sr=8-13) , the hub motor is a direct drive with 2 axels meant for a front drive set up, my question is as follows:
can i cut the axel on one side, effectively turning it into a single axle mount?
i plan to modify my razor pocket mod frame to a delta trike with independent suspension, at current my set ups is 2 hoverboard motors converted to air tires, mounted on a mountain board truck, thats tilted at an angle and can lean: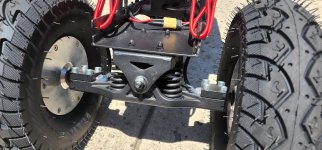
i plan to replace the truck with atv suspension arms ill be welding to the frame. i already have one of these motors and cost wise buying another is the most economical route as opus to getting a specific single axel motor x2, i plan, if mechanically feasible, to cut the axle off of one side and mounting it as a single axle motor, but im not sure if thats mechanically strong enuff, worse case scenario would be just outright pressing out the current axel and just replacing it with a purpose built single axel instead.
the reason im doing this is to add more height for better visibility when i have ot be in the streets, and to have the ability to properly lean the trike. thanks to anyone that has some cents to share on this.
can i cut the axel on one side, effectively turning it into a single axle mount?
i plan to modify my razor pocket mod frame to a delta trike with independent suspension, at current my set ups is 2 hoverboard motors converted to air tires, mounted on a mountain board truck, thats tilted at an angle and can lean:
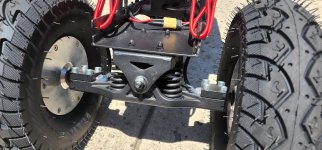
i plan to replace the truck with atv suspension arms ill be welding to the frame. i already have one of these motors and cost wise buying another is the most economical route as opus to getting a specific single axel motor x2, i plan, if mechanically feasible, to cut the axle off of one side and mounting it as a single axle motor, but im not sure if thats mechanically strong enuff, worse case scenario would be just outright pressing out the current axel and just replacing it with a purpose built single axel instead.
the reason im doing this is to add more height for better visibility when i have ot be in the streets, and to have the ability to properly lean the trike. thanks to anyone that has some cents to share on this.