Hi Guys,
I'm planning to make my first 18650 battery pack for a portable raspberry pi, and have been doing some research. So far here's my progress:
Power calculations of setup:
Raspberry Pi 4
Voltage range: 4.7V - 5.25V
Peak: 3A @ 5V = 15W
Typical: 0.6A @ 5V = 3W
Speaker amp board
Voltage range: 2.5V - 5.5V
Peak: 1.2A @ 5V = 6W
Typical: 0.4A @ 5W = 2W
Screen driver board
Voltage range: (Only specifies 12V and I can't find the specs sheet for this)
Typical: 0.3A @ 12V = 3.7W
Fan
Voltage range: 10.8V - 13.2V
Typical: 0.1A @ 12V = 1.2W
I'd like to run this whole setup for around 6-8 hours, that's a total of 9.9W typical load, which is 59.4Wh - 79.2Wh. So I decided to go with a 3S setup, with 2 of those in parallel, giving ~12V with 75.6Wh using Sony VTC6 18650s:
https://cdn.shopify.com/s/files/1/0697/3395/files/Sony_VTC6_specification.pdf?5816251569019225974
I'd also use a XL4015 DC-DC Buck Converter buck converter to step down the voltage to 5V. http://www.xlsemi.com/datasheet/XL4015 datasheet.pdf
The spec sheet says it can do 5A, which is over my peak requirement of 4.2A, assuming 85% efficiency.
1. I understand that batteries in parallel may cause battery to battery discharge due to differing voltages.
I plan to circumvent this by using a 2A fuse wire to connect the cells, similar to how Tesla wires up their batteries.
2. I need a BMS to take care of over-charging, over-discharge and over-current.
Plan to purchase this https://www.banggood.com/Seiko-Prot...-p-1107660.html?rmmds=search&cur_warehouse=CN, because it's over-voltage protection is listed to kick in at 4.22V, which is a safe margin as most 18650s recommend going up to 4.25V.
Here's a drawing of my design for the battery pack..
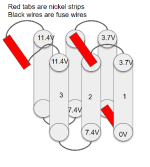
My problem is mainly with balancing, I understand that since I have batteries in series, it's necessary ensure that cell 2 isn't charged anymore if it has hit ~4.3V even though cell 1 may not be at full capacity since I1=I2. In that case, does anyone know of a 3S BMS that can do balancing?
I've found the HX 3S FL25A-A, that some users mention as able to do balancing, but it's over-voltage protection is 4.35±0.05V, which is pretty high for 18650s based on my research:
LG F1L cutoff voltage: 4.3V
Panasonic cutoff voltage: 4.3V
Sony VTC6 cutoff voltage: 4.25V
HX 3S FL25A-A
https://www.aliexpress.com/item/32817897264.html?af=303127
This reddit thread mentions that it can do balancing:https://www.reddit.com/r/Dynavap/comments/cy8lkn/ih_build_question_accu_bms/
I'm planning to make my first 18650 battery pack for a portable raspberry pi, and have been doing some research. So far here's my progress:
Power calculations of setup:
Raspberry Pi 4
Voltage range: 4.7V - 5.25V
Peak: 3A @ 5V = 15W
Typical: 0.6A @ 5V = 3W
Speaker amp board
Voltage range: 2.5V - 5.5V
Peak: 1.2A @ 5V = 6W
Typical: 0.4A @ 5W = 2W
Screen driver board
Voltage range: (Only specifies 12V and I can't find the specs sheet for this)
Typical: 0.3A @ 12V = 3.7W
Fan
Voltage range: 10.8V - 13.2V
Typical: 0.1A @ 12V = 1.2W
I'd like to run this whole setup for around 6-8 hours, that's a total of 9.9W typical load, which is 59.4Wh - 79.2Wh. So I decided to go with a 3S setup, with 2 of those in parallel, giving ~12V with 75.6Wh using Sony VTC6 18650s:
https://cdn.shopify.com/s/files/1/0697/3395/files/Sony_VTC6_specification.pdf?5816251569019225974
I'd also use a XL4015 DC-DC Buck Converter buck converter to step down the voltage to 5V. http://www.xlsemi.com/datasheet/XL4015 datasheet.pdf
The spec sheet says it can do 5A, which is over my peak requirement of 4.2A, assuming 85% efficiency.
1. I understand that batteries in parallel may cause battery to battery discharge due to differing voltages.
I plan to circumvent this by using a 2A fuse wire to connect the cells, similar to how Tesla wires up their batteries.
2. I need a BMS to take care of over-charging, over-discharge and over-current.
Plan to purchase this https://www.banggood.com/Seiko-Prot...-p-1107660.html?rmmds=search&cur_warehouse=CN, because it's over-voltage protection is listed to kick in at 4.22V, which is a safe margin as most 18650s recommend going up to 4.25V.
Here's a drawing of my design for the battery pack..
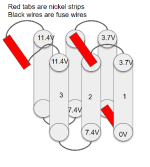
My problem is mainly with balancing, I understand that since I have batteries in series, it's necessary ensure that cell 2 isn't charged anymore if it has hit ~4.3V even though cell 1 may not be at full capacity since I1=I2. In that case, does anyone know of a 3S BMS that can do balancing?
I've found the HX 3S FL25A-A, that some users mention as able to do balancing, but it's over-voltage protection is 4.35±0.05V, which is pretty high for 18650s based on my research:
LG F1L cutoff voltage: 4.3V
Panasonic cutoff voltage: 4.3V
Sony VTC6 cutoff voltage: 4.25V
HX 3S FL25A-A
https://www.aliexpress.com/item/32817897264.html?af=303127
This reddit thread mentions that it can do balancing:https://www.reddit.com/r/Dynavap/comments/cy8lkn/ih_build_question_accu_bms/