DTBAKER61
1 mW
I am working on an old Prodeco with a 4-wire twist throttle. throttle failed..... return spring, switch, and signal all trash. I ordered a new one that had the same body, but it turns out to be 7-wire with different connectors than the original wich was just 4-wire with a single 4-pin connector. I was able (with some suggestions from @amberwolf ) to jigger up the new 7-wire throttle to work with the old controller which had the 4-wire connection ..... schematic and example in post #7.
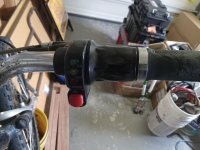
simple old twist throttle. No PAS on this old beast. the old throttle had 4-wire flat connector running to controller
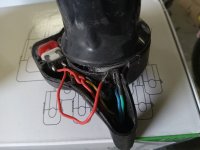
with internal jumpers between PAS/TAG button and HAL transducer... kinda hard to tell what was going on
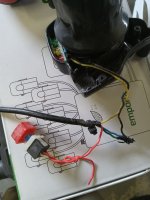
the old transducer was so messed up I could really tell what was going on at first.
new one has 3 connectors and 7 wires to controller....
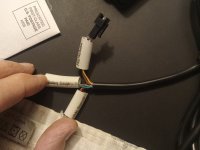
so...... is it possible to connect the new 7-wire throttle to the old 4-wire controller? The colors are all different, so I am unsure.....
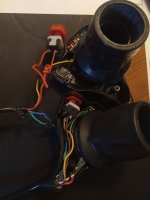
should I toss is the towel and buy a new controller ? (36v, 500watt)
this old bike does not have PAS, just twist throttle..... motor is a pin type connector.
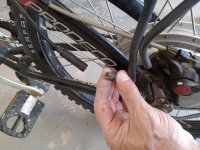
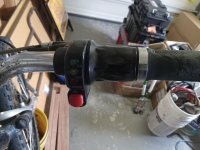
simple old twist throttle. No PAS on this old beast. the old throttle had 4-wire flat connector running to controller
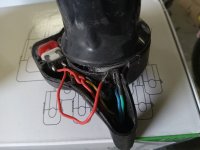
with internal jumpers between PAS/TAG button and HAL transducer... kinda hard to tell what was going on
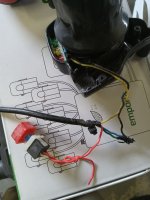
the old transducer was so messed up I could really tell what was going on at first.
new one has 3 connectors and 7 wires to controller....
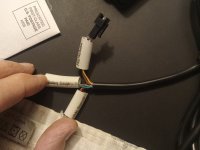
so...... is it possible to connect the new 7-wire throttle to the old 4-wire controller? The colors are all different, so I am unsure.....
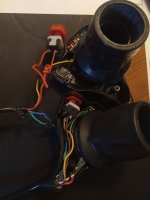
should I toss is the towel and buy a new controller ? (36v, 500watt)
this old bike does not have PAS, just twist throttle..... motor is a pin type connector.
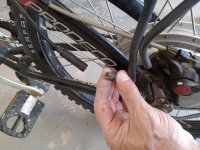
Attachments
Last edited: