bluthermal
1 W
- Joined
- Feb 24, 2008
- Messages
- 58
D-man,
If you or someone can point out to me exactly how to post the pictures, and the requirements like max size, I'll try to post a picture at some point. I tried to do it a long time ago and was unsuccessful. The motor has been removed from the bike, but the fan is still mounted.
As a related note, my forced air cooled 24V 450W motor running at 36V died two weeks ago, after about 6 months and about 1000 miles use. It's possible my air filter was neglected and the air flow had degraded, but I'm not sure.
So, since I knew the system was stressed as it was, I opted for two 24V 450W motors (from TNC scooters) running at 36V, and completed the installation this last weekend. Since Monday and Tuesday I've put 33 miles on the system during commutes. It's working great so far. I was planning on using passive air cooling (drilling all the holes, but no forced air system) because I figured the heat loading would be less with the two motors splitting the load.
It took me a lot longer than I expected to hand make my motor bracket, and I ran out of time to drill out the motors for cooling. The pleasant surprise is that I may not need to ventilate the motors after all. So far, they have not got too hot to the touch. I know that the ambient temps are still mild (around 60 degrees F mornings and 70 degrees F afternoons), but I suspect that for now the motors will be OK. When it gets up to the 80s, 90s and 100s it may be a different story.
I gained at least 2-3 mph top end with the same stock gearing, above the single motor setup.
A separate observation is that at my 200lb weight, I get around 1000 miles per rear wheel spoke breakage incident (2000+ miles now on the bike in about a year). I have no idea if that is normal or not. I have decided to make conscious efforts to avoid high speed bumps and transitions at this point, in an attempt to get more life from the spokes/wheels. If anyone has some suggestions on a good source of specific better/best quality spokes that will fit correctly on the Currie rim and hub combo (gauge and length), I'd like to know what they are, and where/how to get them cheap. Where I live the going rate is $20 to true a wheel, $2 per spoke, and $40 to build a wheel (plus $2 per spoke) at the bike shops. I've been to 4 local shops now and none have had (or said they could/would get) spokes the right size for the Currie wheels.
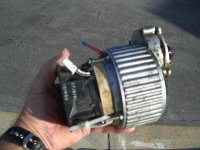
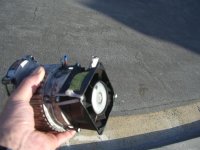
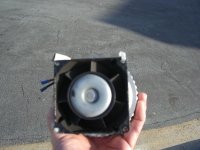
View attachment 4View attachment 3
If you or someone can point out to me exactly how to post the pictures, and the requirements like max size, I'll try to post a picture at some point. I tried to do it a long time ago and was unsuccessful. The motor has been removed from the bike, but the fan is still mounted.
As a related note, my forced air cooled 24V 450W motor running at 36V died two weeks ago, after about 6 months and about 1000 miles use. It's possible my air filter was neglected and the air flow had degraded, but I'm not sure.
So, since I knew the system was stressed as it was, I opted for two 24V 450W motors (from TNC scooters) running at 36V, and completed the installation this last weekend. Since Monday and Tuesday I've put 33 miles on the system during commutes. It's working great so far. I was planning on using passive air cooling (drilling all the holes, but no forced air system) because I figured the heat loading would be less with the two motors splitting the load.
It took me a lot longer than I expected to hand make my motor bracket, and I ran out of time to drill out the motors for cooling. The pleasant surprise is that I may not need to ventilate the motors after all. So far, they have not got too hot to the touch. I know that the ambient temps are still mild (around 60 degrees F mornings and 70 degrees F afternoons), but I suspect that for now the motors will be OK. When it gets up to the 80s, 90s and 100s it may be a different story.
I gained at least 2-3 mph top end with the same stock gearing, above the single motor setup.
A separate observation is that at my 200lb weight, I get around 1000 miles per rear wheel spoke breakage incident (2000+ miles now on the bike in about a year). I have no idea if that is normal or not. I have decided to make conscious efforts to avoid high speed bumps and transitions at this point, in an attempt to get more life from the spokes/wheels. If anyone has some suggestions on a good source of specific better/best quality spokes that will fit correctly on the Currie rim and hub combo (gauge and length), I'd like to know what they are, and where/how to get them cheap. Where I live the going rate is $20 to true a wheel, $2 per spoke, and $40 to build a wheel (plus $2 per spoke) at the bike shops. I've been to 4 local shops now and none have had (or said they could/would get) spokes the right size for the Currie wheels.

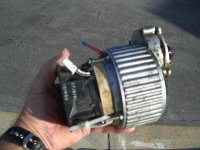
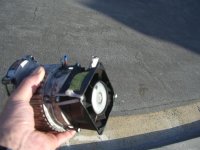
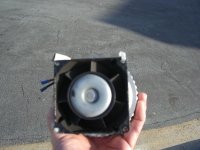

