Hi all,
I read this topic with much interest, and I plan to use the information I found to update my Tidal Force IO Step Through.
As removing the main, original NiMH battery is above my current skills, I will use a 48V, 10 Ah, LiFePO4 battery simultaneously
with the 36V hub battery. In order to not damage the lower voltage battery, I will use a double rectifier, 30Amp, 60V: namely the MBR3060
This will prevent the 48V source to try charging the hub battery and conversely, the 36 V to charge the 48V (if discharged).
Then there's the motor;
I read that the TF motor will not work above 47.5 V and a few volts before that (from 44V and up) you fry the "logic supply".
So I want to include a PWM regulator before the double-diode to set the voltage coming from the LiFePO battery to around 42 V to be safe. Any extra voltage above 36V will boost
the motor and thus the bike speed (work around the crippling to 250W on my french tidalforce).
I will do my best to keep the delphi MetriPack 480 cabling even though the Anderson connectors are ubuquitous here (but not watertight).
So far, the schematic I want to use is the following:
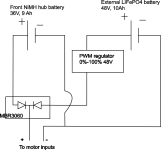
If you see any problem with this, do not hesitate to comment !
I ordered most of the components I need during the week-end, and I'm eager to get them to start work on my TF
Thanks to all contributors of this thread and especially Ambrose Liao and miro for their enthusiasm and lots of info provided for the TidalForce !
EDIT: Using PWM to reduce voltage doesn't work and the motor will still see some voltages superior to 48V, which is not good at all. I need to find a better way.