Hi,
I'm interesting in connecting 2 36V Li-ion ebike batteries in parallel using ideal diodes (e.g. mosfets) for reverse current protection. I know that (in principle) ideal diodes are not needed if the two batteries are connected with the same state of charge. However I have to use diodes in my application because each battery is protected with its own BMS and both BMS don't let any charging current run from the discharge wires. Additionally, I'd like to use the batteries with slightly different state of charges so (ideal) diodes are required.
My question regards what happens in terms of inductance in the wiring when the motor is stopped and each battery is protected with its own ideal diode? My understanding is that, without the diodes, wire inductance is not really a problem as it would be smoothed out by each battery (although that is not really possible if the BMS does not allow the batteries to be charged through the discharge leads...). However, with the diodes, current cannot flow back to the batteries so would that create a voltage spike between the controller and the ideal diodes, possibly leading to premature failure of any of these?? If so, is there anything to prevent such voltage spike from happening, i.e. by using a flyback diode somewhere in the circuit? I'm mostly concerned by the inductance in the positive fat wire (between controller and diodes) seen on the image below.
Would such a system be reasonably safe? I'd possibly be adding additional fuses next to each battery but I'm not sure this would add much since the discharge has to handle 20A max while each battery is supposed to be charged at 4A max (so e.g. a 25A fuse suitable for discharge would not really protect anything in case one of the diode fails as the charging current would likely but much higher than 4A without the fuse blowing...)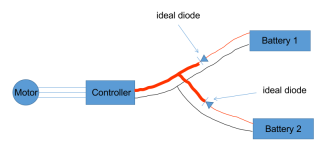
I'm interesting in connecting 2 36V Li-ion ebike batteries in parallel using ideal diodes (e.g. mosfets) for reverse current protection. I know that (in principle) ideal diodes are not needed if the two batteries are connected with the same state of charge. However I have to use diodes in my application because each battery is protected with its own BMS and both BMS don't let any charging current run from the discharge wires. Additionally, I'd like to use the batteries with slightly different state of charges so (ideal) diodes are required.
My question regards what happens in terms of inductance in the wiring when the motor is stopped and each battery is protected with its own ideal diode? My understanding is that, without the diodes, wire inductance is not really a problem as it would be smoothed out by each battery (although that is not really possible if the BMS does not allow the batteries to be charged through the discharge leads...). However, with the diodes, current cannot flow back to the batteries so would that create a voltage spike between the controller and the ideal diodes, possibly leading to premature failure of any of these?? If so, is there anything to prevent such voltage spike from happening, i.e. by using a flyback diode somewhere in the circuit? I'm mostly concerned by the inductance in the positive fat wire (between controller and diodes) seen on the image below.
Would such a system be reasonably safe? I'd possibly be adding additional fuses next to each battery but I'm not sure this would add much since the discharge has to handle 20A max while each battery is supposed to be charged at 4A max (so e.g. a 25A fuse suitable for discharge would not really protect anything in case one of the diode fails as the charging current would likely but much higher than 4A without the fuse blowing...)
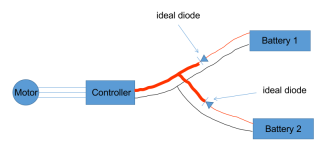