seba240698
100 mW
- Joined
- May 10, 2019
- Messages
- 42
Hi all.
I'm new member.
Pardon me if I post in a wrong section, I was contemplating to post in "General Discussion" section or this section.
I bought an used e-bike about 4 months back and it was working fine about 1 month, then came plenty of problems, plenty of downtime and disappointment.
Problems like rear tyre punctured, drive side crankarm stuck in frame, rear freewheel hub worn, chain worn, bottom bracket came loose, rear derailleur hanger broke, motor power cut off intermittently , battery connectors came loose etc, all of which I managed to resolve and repair them satisfactorily, at least based on my standard. I consulted You-tube and relevant bike forums to get the solutions.
To cut the long story short, I have new problems which I am lost for a solution for almost 2 weeks with my e bike, I hope to get some expert advice from here.
I replaced my controller and LCD display recently after the old LCD display showed no sign of power after a heavy rain. I waited for the parts for 2 weeks from China and installed in my e-bike. Alas, the LCD display lights up BUT the motor now runs at less than 10% of power (based on my experience when my e bike was working fine). My LCD display and controller photos are shown. The sticker on the rear hub motor reads 36V and manufacturer from China.
My diagnosis so far :
1) I suspected the Hall sensor, but when I disconnected the Hall sensors, I started the motor running by pedal assist (throttle is not allowed in my country), there was no difference in performance, motor still ran at less than 10% of power,
2) I checked the battery voltage with a multimeter, it showed 40V for a 36V rated battery, when the motor was not running,
Both controller and LCD display are brand new, bought online.
3) I measured the voltage between the 2 phase wires of the motor, it varied from 10 V to 29 V ac (I switched my multimeter to measure Vac) and the current in the phase wire to motor was from 3A to 13A ac, my motor is rated at 250 W but controller is rated 250 W to 350W.
4) my next step is to measure battery's voltage when motor is running and to measure the hall sensors voltage when motor is running,
My question is, what is damaged? LCD display (unlikely as it is new), Hall sensors (which is redundant as not connecting them doesn't seem to make a difference) or motor (my worst fear as it will cost me about $300 and 3 weeks waiting).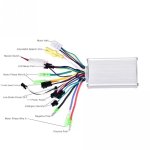
I'm new member.
Pardon me if I post in a wrong section, I was contemplating to post in "General Discussion" section or this section.
I bought an used e-bike about 4 months back and it was working fine about 1 month, then came plenty of problems, plenty of downtime and disappointment.
Problems like rear tyre punctured, drive side crankarm stuck in frame, rear freewheel hub worn, chain worn, bottom bracket came loose, rear derailleur hanger broke, motor power cut off intermittently , battery connectors came loose etc, all of which I managed to resolve and repair them satisfactorily, at least based on my standard. I consulted You-tube and relevant bike forums to get the solutions.
To cut the long story short, I have new problems which I am lost for a solution for almost 2 weeks with my e bike, I hope to get some expert advice from here.
I replaced my controller and LCD display recently after the old LCD display showed no sign of power after a heavy rain. I waited for the parts for 2 weeks from China and installed in my e-bike. Alas, the LCD display lights up BUT the motor now runs at less than 10% of power (based on my experience when my e bike was working fine). My LCD display and controller photos are shown. The sticker on the rear hub motor reads 36V and manufacturer from China.
My diagnosis so far :
1) I suspected the Hall sensor, but when I disconnected the Hall sensors, I started the motor running by pedal assist (throttle is not allowed in my country), there was no difference in performance, motor still ran at less than 10% of power,
2) I checked the battery voltage with a multimeter, it showed 40V for a 36V rated battery, when the motor was not running,
Both controller and LCD display are brand new, bought online.
3) I measured the voltage between the 2 phase wires of the motor, it varied from 10 V to 29 V ac (I switched my multimeter to measure Vac) and the current in the phase wire to motor was from 3A to 13A ac, my motor is rated at 250 W but controller is rated 250 W to 350W.
4) my next step is to measure battery's voltage when motor is running and to measure the hall sensors voltage when motor is running,
My question is, what is damaged? LCD display (unlikely as it is new), Hall sensors (which is redundant as not connecting them doesn't seem to make a difference) or motor (my worst fear as it will cost me about $300 and 3 weeks waiting).
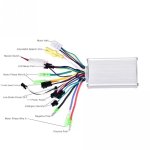