Alan B said:
In DC converter designs the buck-boost designs have lower efficiency and increased complexity and cost, they are generally not used much except when really needed, and usually not at high power.
I appreciate the detailed reply. Thanks.
My estimate (comparing watt meter output to watt meter input) is that this booster operates right around 95% efficiency. My (admittedly over-the-top) headlight consumes more power. The booster runs cool. The fan never kicks on and it never seems any warmer to the touch than the ambient temperature. My watt-hour/mile rates seem to be pretty typical. If anything, a bit better than average for a conventional upright bike. So for my commuter uses, a 5% loss is insignificant. I might care more for longer distance touring. But I'd save more by getting a less powerful headlight.
Alan B said:
If you want to turn a boost converter off it could be done with a diode from battery to output and SPST switch on the converter input which may be safer. When the converter is boosting the diode will be reverse biased and won't conduct, and when the input power to the converter is removed the current will flow around the booster. The booster circuits generally contain a diode already that will block current flow back into the converter.
You've lost me on the bit about turning the booster off. I pretty much want it on all the time. The quiescent current is 15ma. These days I leave the battery constantly hooked up to the watt meter, booster and motor controller. The drain is too small for the watt meter to register. Though after 12 hours I can see a very slight voltage drop. The only reason I had it disconnected before the booster died was because I had the bike parked and locked in a public place.
The booster inputs are protected from shorts and reverses. It is unclear what the output protection is. It seems tolerant of whatever the DD motor sends back when coasting. However, it complained and shut itself down when I enabled the e-brake/regen function which presumably sent a lot more current back toward the booster. For all I know, that little experiment damaged it. Though I did that last winter and have put about 2000 miles on the bike since then.
Alan B said:
The cheap converters are often data-sheet example designs and they rarely have the correct components and adequate safety deratings and may be lacking in components that are generally added to real designs. Apply your own deratings and run well below stated maximums for reliability. Checking the specs on the parts before using the unit may reveal incorrect voltage ratings, we've seen that, I think it was in a discussion here on battery charging with them and the diodes were not up to the required ratings. They don't always use good parts, and may have counterfeit parts in them as well. Also make sure to avoid exceeding every spec, it is easy to miss one and stress the components in some way.
I'm not sure about all the parts, but the capacitors are nichicon which appear to be in the top-tier category. I run well within the input and output voltage specs, but I am running at maximum current output have for the 3000 miles I've run it. Of course it isn't pulling that current all the time. I run PAS about 90% of the time now and that limits current to about 17 of the 25 amps allowed per spec. Typical draws are in the 7-12 amp range I think. About 1/3 to 1/2 of the booster's limit. But I do use full throttle every now and then as a "boost" which is puts the booster at the spec limit of 25 amps while in the 31-60 volt input range. When below 31v, the spec is 30 amps. But even when pulling full power going up a hill, the booster's cooling fan never turns on and the heatsink never gets even warm to the touch. So if I was stressing anything, it seems unlikely that it was a heat stress.
Alan B said:
An intermittent output connection when outputting current can cause incredibly high voltage spikes to be generated from stored energy in the inductor, enough to blow components, especially the semiconductors. So the loose connector may have blown the converter.
The disconnection was on the input, not the output side. When I removed the failed booster the output connections were still solid. And the input wasn't loose, it was simply partially engaged and completing the circuit through the pre-charge resistor in the XT90 connector. My guess now is that the booster had already failed and the fact that the current was flowing only through the pre-charge resistor is what kept the booster's fuses from blowing right away.
Alan B said:
A quality controller with field weakening is probably be a better way of solving this problem. It is similar to boost conversion, but it occurs in the motor and controllers set up for it are likely to have the proper design as well as not introducing additional loss items to the power path. The LVC will be handled better and it won't add another item that has to be mounted, cooled, and sealed from the weather.
Sure. That is clearly the better way. It is also clearly the much more expensive way. Keep in mind that this is a first e-bike built with economy as a major consideration. And while I find the notion of getting a PhaseRunner to be very attractive, that also means I would need to get a CA as well. In the long run, that's probably $450 well spent. But in the short run it isn't necessary ... yet. The trick here is to be careful of how more money I sink into the current scheme if I figure I'm going to end up with a PhaseRunner and CA in the long run.
I'm attaching photos of front and back of the failed booster. I noticed that the back of the PCB had picked up some crud. I'm wondering if that combined with a bit of condensed moisture might have caused a short with possibly cascading failures resulting? Note especially the three pronged component (resistor or diode?) at the top. BTW, I put a conformal coating on the watt meter circuit board and will be doing that with the new booster this weekend ... just in case.
Oh - almost forgot. I tested the output capacitors for shorts and found none. The capacitors seems to act normally in that they showed an initial resistance of about 1kohm that progressively increased as I left the meter connected - presumably because the capacitors were storing charge and hence increasing resistance.
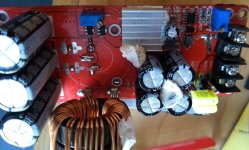