Cookie Monster
1 mW
I'm close to finished with a wood battery frame case, more pictures to come. My goal was to have a more secure waterproof case than the standard frame bag. Plus I wanted to fit the controller inside for a cleaner look. It will be stained black and some waterproofing sealent added.
But I'm worried about heat the controller will give off on the cedar wood. These are early pictures and don't show the air flow holes I put in the box. Two 1" holes in the front for air intake and one 1" hole in the back by the controller for air flow exit. I am also using these holes for controls and motor wires. This open side will be covered with a wood and will have a small door that opens to get in for charging.
My question, do you think the air flow through would be sufficient to keep the controller from getting too hot? I guess testing will be the only true tell (it's kind of a tight fit). I am thinking about cutting out a section on the top, above the controller, for a heatsink but would rather not if it's not needed.
10t mac 500w
52v 18ah cellman triangle battery
12fet
Pushing a max of 1100 peak watts, sustained out put is around 400w.
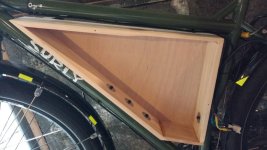
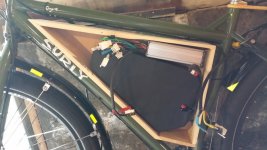
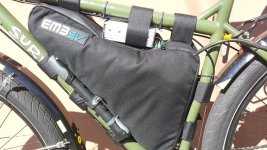
But I'm worried about heat the controller will give off on the cedar wood. These are early pictures and don't show the air flow holes I put in the box. Two 1" holes in the front for air intake and one 1" hole in the back by the controller for air flow exit. I am also using these holes for controls and motor wires. This open side will be covered with a wood and will have a small door that opens to get in for charging.
My question, do you think the air flow through would be sufficient to keep the controller from getting too hot? I guess testing will be the only true tell (it's kind of a tight fit). I am thinking about cutting out a section on the top, above the controller, for a heatsink but would rather not if it's not needed.
10t mac 500w
52v 18ah cellman triangle battery
12fet
Pushing a max of 1100 peak watts, sustained out put is around 400w.
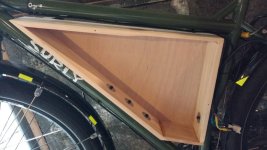
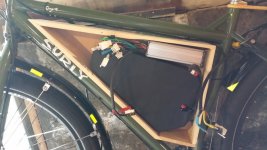
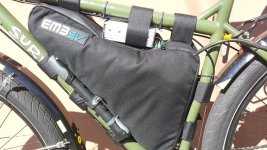