Hi All,
I just built an electric mountain board but am having some problems in the power or torque or gearing of my rig. I listed out the components/specs below and had thought that I had somewhat over built this system but I cannot seem to any get good inital speed. I am using a sensorless brushless motor with an ESC that came with a sensor cable(but I dont think that matters right?) do certain ESCs required sensored motors?
Basically, as I attempt to throttle up it seems like the motor does not have the power to turn. I can see it struggling to turn, it makes a chuck chuck chuck type sound and it will move forward(at less than a few feet a sec) but it is laboring bad and cannot get up to speed. Even when I try to give it a bit of a push before throttle I cannot seem to avoid this, perhaps if I got to speed this would go away but I am not sure as I cant get there.
I can see that the belt is not skipping and I have tried numerous timing changes(up and down) soft start, and load changes on the ESC with no major change. I also rewired the ESC to directly connect the motor contacts in case there was a connection issue to no avail. I have wired the batteries in series to get 12s with my setup and I do see that people warn against long power wires to the ESC, which I do have. I understand that this could cause premature ESC failure but could this cause my motor struggling issue as well?
Could this be a bad motor? should the motor be able to easily overcome my grip and take my weight for the start? Any input is greatly appreciated!
I attached a couple pics of my first prototype(it is a little more robust now) 3d-print motor mount for your entertainment. Unfortunately, I tore the whole board down today but if we can get the thing moving I will post more as it comes back together.
specs:
-Turnigy Aerodrive SK3 - 6374-149kv Brushless Outrunner
-TURNIGY K-Force 120A-HV OPTO V2 5-12S
-17 tooth pully 5mm HTD
-62 tooth wheel cog 5MM HTD
-80 tooth belt 5MM HTD
-2 x 6s 5.0A 20s lipo
-SBEC Hobbyking YEP 20A HV (for receiver)
-frysky receiver
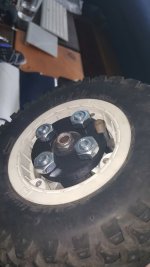
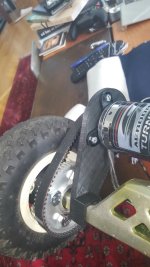
I just built an electric mountain board but am having some problems in the power or torque or gearing of my rig. I listed out the components/specs below and had thought that I had somewhat over built this system but I cannot seem to any get good inital speed. I am using a sensorless brushless motor with an ESC that came with a sensor cable(but I dont think that matters right?) do certain ESCs required sensored motors?
Basically, as I attempt to throttle up it seems like the motor does not have the power to turn. I can see it struggling to turn, it makes a chuck chuck chuck type sound and it will move forward(at less than a few feet a sec) but it is laboring bad and cannot get up to speed. Even when I try to give it a bit of a push before throttle I cannot seem to avoid this, perhaps if I got to speed this would go away but I am not sure as I cant get there.
I can see that the belt is not skipping and I have tried numerous timing changes(up and down) soft start, and load changes on the ESC with no major change. I also rewired the ESC to directly connect the motor contacts in case there was a connection issue to no avail. I have wired the batteries in series to get 12s with my setup and I do see that people warn against long power wires to the ESC, which I do have. I understand that this could cause premature ESC failure but could this cause my motor struggling issue as well?
Could this be a bad motor? should the motor be able to easily overcome my grip and take my weight for the start? Any input is greatly appreciated!
I attached a couple pics of my first prototype(it is a little more robust now) 3d-print motor mount for your entertainment. Unfortunately, I tore the whole board down today but if we can get the thing moving I will post more as it comes back together.
specs:
-Turnigy Aerodrive SK3 - 6374-149kv Brushless Outrunner
-TURNIGY K-Force 120A-HV OPTO V2 5-12S
-17 tooth pully 5mm HTD
-62 tooth wheel cog 5MM HTD
-80 tooth belt 5MM HTD
-2 x 6s 5.0A 20s lipo
-SBEC Hobbyking YEP 20A HV (for receiver)
-frysky receiver
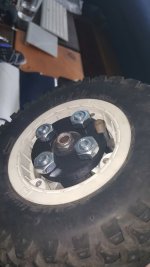
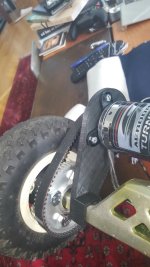