rick_p
100 W
A friend gave me a 36 volt battery he was no longer using and thought was in working condition, which is understandable because he was good about topping off the charge every few months and the charge indicator LEDs show a full charge. However, when I tested it at home there was no voltage at the discharge port. The fuse is not accessible from the outside of the battery so I had to open it up and look for the fuse inside. Once inside I found the fuse and it was fine, no signs of overheating at the terminals of the fuse holder, but then I saw this and figured this can't be good.
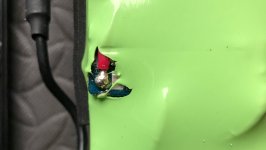
I cut away the shrink wrap to get a better look because clearly that solder connection got very hot at some point. I'm only a novice at best when it comes to battery internals but I know enough to check the basics, most of what I learned I did so on this site, or from watching videos. As you can see in the picture below, the terminal that got hot was the positive supply from the cells (P+) to the BMS. I tested the voltage at P+ and P- and got zero voltage, I got 40 volts at P+ and B- which I believe tells me the cells are fully charged but the BMS has shut down and not allowing the voltage to pass through to the discharge port.
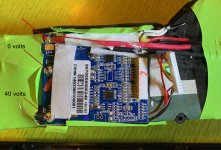
The question I have is, is it safe to assume that the problem is the BMS itself went bad or is it more likely that something else went wrong which caused the heat at the P+ solder connection, and then the BMS just shut down to prevent fireworks, and the BMS is working and just doing what it's supposed to do?
If the BMS went bad, and the battery can be fixed by replacing it, I'm comfortable doing the work, there are videos that show how to do it safely and I have the soldering skills, but I did some shopping for the 10s 36v BMS and I didn't find any with the same wiring configuration. This is where my lack of experience might be an issue. In the photo below you can see that the main harness doesn't have balance wires in every port, is that typical of a 10s 36v battery? Also, none if the BMSs I saw showed terminals to solder the wires to that go to the charge indicator LED circuit board, which is just to the right of the main harness in the picture below. Lastly, there are two white wires soldered to the BMS just to the right of charge indicator wires, which I figured are for a thermal sensor, but if they are, I will need to remove a lot more shrink wrap to trace where they go.
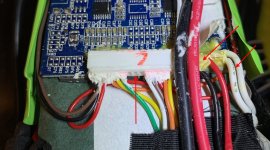
I would love to use this battery, and it seems fixable, but I could use a little guidance here. Thank you
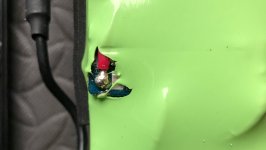
I cut away the shrink wrap to get a better look because clearly that solder connection got very hot at some point. I'm only a novice at best when it comes to battery internals but I know enough to check the basics, most of what I learned I did so on this site, or from watching videos. As you can see in the picture below, the terminal that got hot was the positive supply from the cells (P+) to the BMS. I tested the voltage at P+ and P- and got zero voltage, I got 40 volts at P+ and B- which I believe tells me the cells are fully charged but the BMS has shut down and not allowing the voltage to pass through to the discharge port.
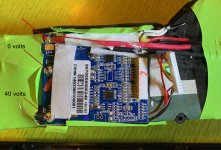
The question I have is, is it safe to assume that the problem is the BMS itself went bad or is it more likely that something else went wrong which caused the heat at the P+ solder connection, and then the BMS just shut down to prevent fireworks, and the BMS is working and just doing what it's supposed to do?
If the BMS went bad, and the battery can be fixed by replacing it, I'm comfortable doing the work, there are videos that show how to do it safely and I have the soldering skills, but I did some shopping for the 10s 36v BMS and I didn't find any with the same wiring configuration. This is where my lack of experience might be an issue. In the photo below you can see that the main harness doesn't have balance wires in every port, is that typical of a 10s 36v battery? Also, none if the BMSs I saw showed terminals to solder the wires to that go to the charge indicator LED circuit board, which is just to the right of the main harness in the picture below. Lastly, there are two white wires soldered to the BMS just to the right of charge indicator wires, which I figured are for a thermal sensor, but if they are, I will need to remove a lot more shrink wrap to trace where they go.
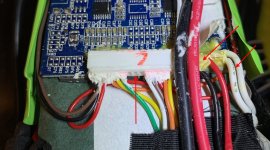
I would love to use this battery, and it seems fixable, but I could use a little guidance here. Thank you