Finally got a new TSDZ2 motor casing in the mail a few days ago. I've set up a work space next to my computer so I can reference videos and photos to help me put this thing back together. Glad I brought the casing to a LBS with a bearing press this morning to install the new needle bearing.
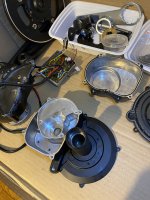
At 2:40 and 6:53 of this video there are 2 brass shims which my motor does not have. Are there different versions of this motor where some have these washers and others not?
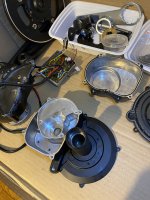
At 2:40 and 6:53 of this video there are 2 brass shims which my motor does not have. Are there different versions of this motor where some have these washers and others not?