Article posted August 1`09, sub-titled "Exploring some potential ultra light-weight vehicle building materials" here:
http://www.autospeed.com/cms/A_111401/article.html
Executive summary:
In AutoSpeed we've recently covered a couple of techniques for building ultra light-weight vehicles.
...composite fibreglass and aluminium honeycomb panels to form the monocoque...
...chassis...covered in expanded polystyrene modelling foam, carved to shape...covered in fibreglass cloth and resin.
also
...high strength chrome-moly steel tube, nickel-bronze brazed together.
...are there any alternatives?
Yes, there's a composite material that is very cheap, widely available in flat sheets, can be easily worked, has available excellent glues...
It's wood...
...composite wood sandwich construction...
Another wood-based material worth investigating is paper honeycomb paneling.
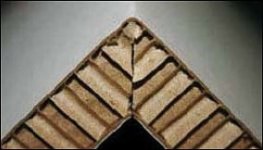
...and:
Conclusion
It may sound a bit down-market over the use of exotic materials like carbon fibre or Kevlar, but naturally occurring cellular composites (ie wood!) in either laminated, shaped form or as honeycomb panels, are cheaper, more easily worked, less energy intensive in production, and can be later recycled. As history shows, if it is used correctly, it can also be surprisingly strong and light.
If you're building an ultra light-weight vehicle, wood is definitely a material to investigate.