acuteaero
100 W
So I went back and read hundreds of pages of ES threads about running double freewheels on the right hand side of hubs for "parallel" drive-
http://www.endless-sphere.com/forums/viewtopic.php?f=28&t=12449
http://www.endless-sphere.com/forums/viewtopic.php?f=28&t=13532
http://www.endless-sphere.com/forums/viewtopic.php?f=28&t=12267
I understand the reasons that cutting splines inside the BMX freewheels and putting them on a freehub has been used and seems to be the de-facto solution- I have been thinking of an alternate option- making up a hub with stepped threads- a 1.375" thread for an ENO freewheel, likely the sick-bike-parts flanged unit, and a M30 thread for a <=15t BMX freewheel to use for the pedaling chain.
I understand that the splined freewheel on freehub solution works well- but it's always seemed a bit odd to me to put the double freewheels in parallel in series with the freewheel in the freehub--- I have never seen an explanation if this is a desirable feature- it seems to me that it is less than ideal-
Without further ado- here are the pictures I've made. The hub design is based strongly off the hub I removed from a 17" moped wheel I got from Stevil_Knevil. http://www.endless-sphere.com/forums/viewtopic.php?t=35066 . The design uses the same sized bearings and spoke flanges.
I realize that a fundamental issue is that the 28mm OD bearing won't fit through the M30 thread. Both bearings have to come in from the other side. This makes some kind of goofy compromises, and makes the assembly naturally not axially constrained. That's why I added the large retaining snap ring. I also assume the bearings would be press fit into the hub bore, or loctited in, either way. Other potential issues- the bearing on the threaded side has to be pretty far away from the dropout- that's why I enlarged the axle to the 15mm bearing ID size all the way to the dropout. With a cro-moly axle it'd probably be OK---. I also switched from external M10 threads on the end of the axle to internal M8 threads into a 10mm boss- this is a bit easier to machine than the external threads... One other odd aspect is that the M30 freewheel ends up threading against the removal dog flange on the white freewheel- I think there's just enough engagement there to prevent disaster, a thin steel washer could also be made.
Shown with a SBP Eno and crossfire 13t freewheel.
The chain-line to the flanged freewheel looks pretty good with a hookworm-wide tire on the wheel.
What do you think? If you don't persuade me it's a bad idea I'll make a couple up next weekend, or maybe the weekend after that.
-H
http://www.endless-sphere.com/forums/viewtopic.php?f=28&t=12449
http://www.endless-sphere.com/forums/viewtopic.php?f=28&t=13532
http://www.endless-sphere.com/forums/viewtopic.php?f=28&t=12267
I understand the reasons that cutting splines inside the BMX freewheels and putting them on a freehub has been used and seems to be the de-facto solution- I have been thinking of an alternate option- making up a hub with stepped threads- a 1.375" thread for an ENO freewheel, likely the sick-bike-parts flanged unit, and a M30 thread for a <=15t BMX freewheel to use for the pedaling chain.
I understand that the splined freewheel on freehub solution works well- but it's always seemed a bit odd to me to put the double freewheels in parallel in series with the freewheel in the freehub--- I have never seen an explanation if this is a desirable feature- it seems to me that it is less than ideal-
Without further ado- here are the pictures I've made. The hub design is based strongly off the hub I removed from a 17" moped wheel I got from Stevil_Knevil. http://www.endless-sphere.com/forums/viewtopic.php?t=35066 . The design uses the same sized bearings and spoke flanges.
I realize that a fundamental issue is that the 28mm OD bearing won't fit through the M30 thread. Both bearings have to come in from the other side. This makes some kind of goofy compromises, and makes the assembly naturally not axially constrained. That's why I added the large retaining snap ring. I also assume the bearings would be press fit into the hub bore, or loctited in, either way. Other potential issues- the bearing on the threaded side has to be pretty far away from the dropout- that's why I enlarged the axle to the 15mm bearing ID size all the way to the dropout. With a cro-moly axle it'd probably be OK---. I also switched from external M10 threads on the end of the axle to internal M8 threads into a 10mm boss- this is a bit easier to machine than the external threads... One other odd aspect is that the M30 freewheel ends up threading against the removal dog flange on the white freewheel- I think there's just enough engagement there to prevent disaster, a thin steel washer could also be made.
Shown with a SBP Eno and crossfire 13t freewheel.
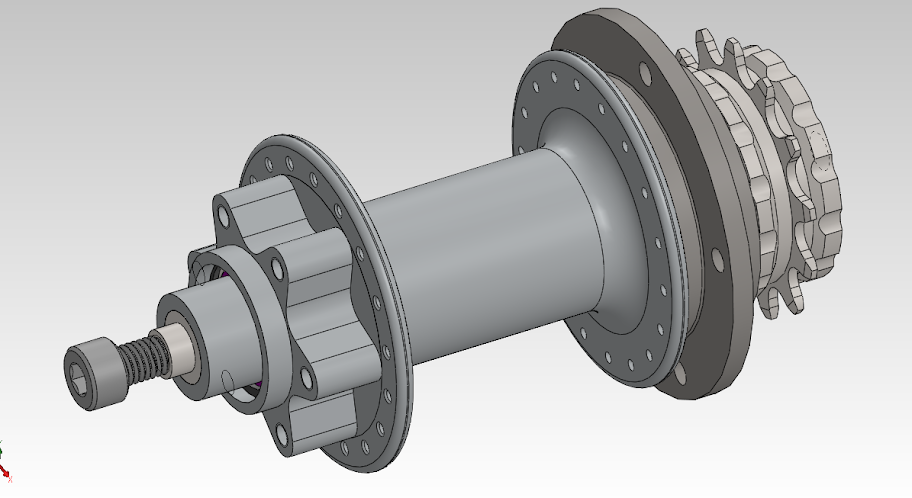
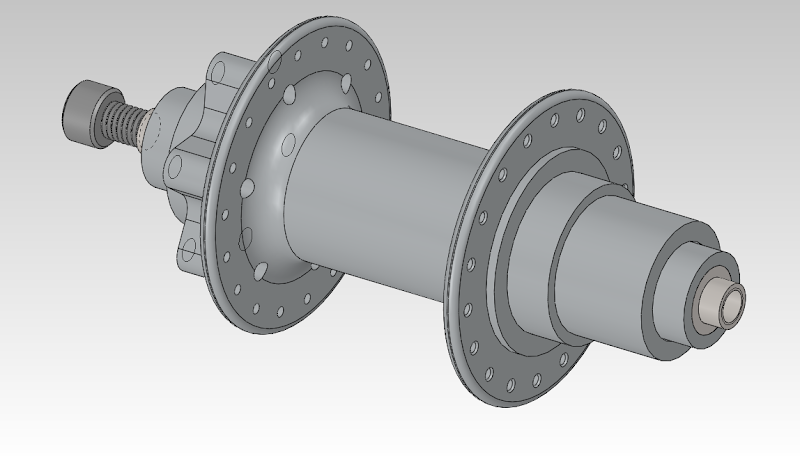
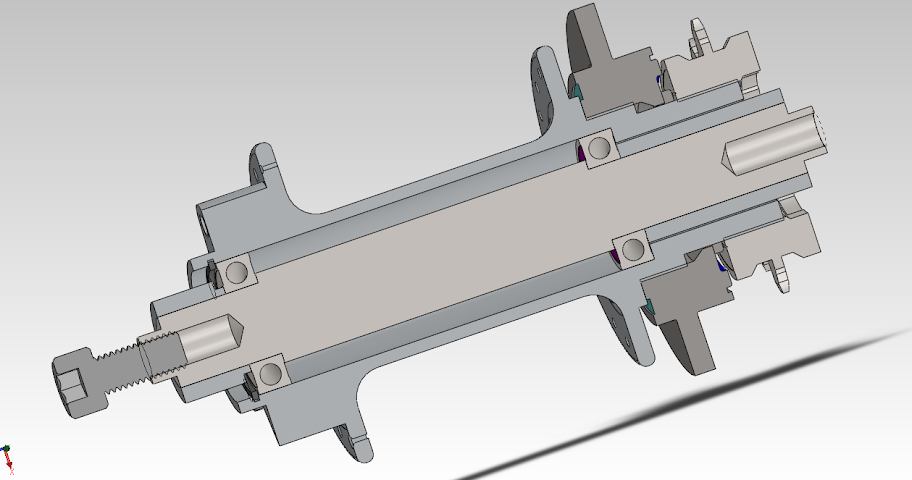
The chain-line to the flanged freewheel looks pretty good with a hookworm-wide tire on the wheel.
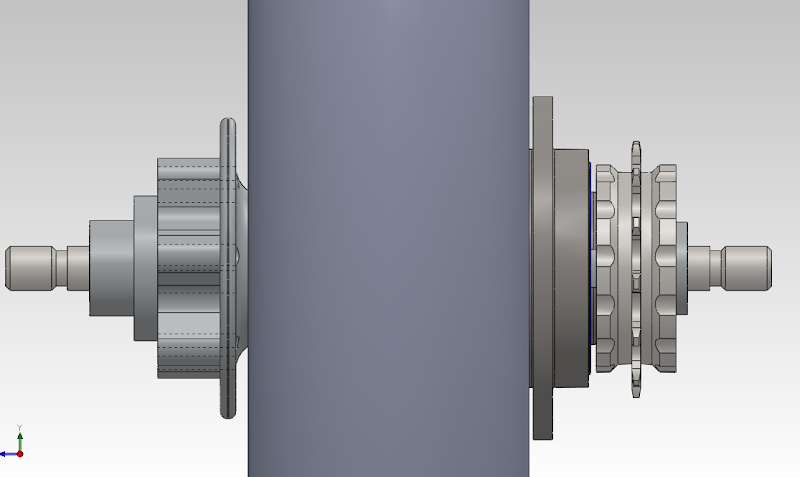
What do you think? If you don't persuade me it's a bad idea I'll make a couple up next weekend, or maybe the weekend after that.
-H