hydro-one
10 kW
Im thinking this thread could be for complaining of a technical nature.
I'll start!!
Due to the HT35 not having hall sensors as a factory option at the time, I had to cut my axle slot up with a di-grinder, so the wires (10g teflon, and 28g teflon hall wires), would pass undamaged. I guess i went abit far (i didnt think at the time)and now my axle is broken!!! (afr 6 months hard use, including doing a drop that broke 12 spoke, hiting a curb that broke 7 spokes, i could go on and on). So its broke, Im going to order 5 axles from max and keep them onhand for anyone that wants them can contact me via pm!! Unless farfle or someone knows a custom solution, i would be very interested in that......!!
Not really crystalyes fault, but still caused me ALOT of headaches/work . the axle isnt real strong to begin with!! and the design sucks! edit the first one with three wires had a hole in it out of the box, so it actually is thier fault edit and had loose nuts on the bolts that hold the two plates that form the center of the motor. they would have fallen off immediatly and probably ruined the stator. good thing i caught that one. plus the wheels sucked, i could on and on but ill let someone else pick it up!!!!!
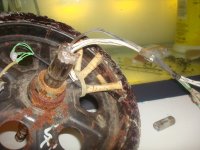
I'll start!!
Due to the HT35 not having hall sensors as a factory option at the time, I had to cut my axle slot up with a di-grinder, so the wires (10g teflon, and 28g teflon hall wires), would pass undamaged. I guess i went abit far (i didnt think at the time)and now my axle is broken!!! (afr 6 months hard use, including doing a drop that broke 12 spoke, hiting a curb that broke 7 spokes, i could go on and on). So its broke, Im going to order 5 axles from max and keep them onhand for anyone that wants them can contact me via pm!! Unless farfle or someone knows a custom solution, i would be very interested in that......!!
Not really crystalyes fault, but still caused me ALOT of headaches/work . the axle isnt real strong to begin with!! and the design sucks! edit the first one with three wires had a hole in it out of the box, so it actually is thier fault edit and had loose nuts on the bolts that hold the two plates that form the center of the motor. they would have fallen off immediatly and probably ruined the stator. good thing i caught that one. plus the wheels sucked, i could on and on but ill let someone else pick it up!!!!!
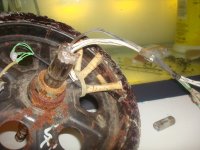