harrisonpatm
10 kW
- Joined
- Aug 8, 2022
- Messages
- 824
I am looking to do a small moped conversion as a second vehicle to my larger e-moto. I would like to use a 2400w BLDC that I was able to acquire at the scrapyard for $6. Today I picked up a Trac moped from 1986 that could be a good base, it weighs less than 100 pounds and the motor mounting points look close enough that I could probably fab a motor mount myself without too much difficulty.
The issue is fitting a sprocket. I have never done this before, so I have little to know experience regarding the parts available and how to properly secure sprockets. So before I dive into the project, can someone with more experience tell me if this is at all possible? If not, that's fine, I can ditch the parts and look elsewhere. Just want to know if this is going to become too large of a bottleneck for the project to complete itself.
My goals are around 35mph top speed, it's going to be a neighborhood commuter. Rear wheel is approx 20 inches diameter. Omnicalculator tells me the rear wheel will need to spin at 588 rpm to achieve that speed, so lets call it 600. Rear sprocket is 42t. My motor's specs are hard to track down for sure, but it looks like I can expect a top rpm, loaded, of about 4000 @72v. That's top speed, meaning that I may need to find a rear sprocket with more teeth. But I've already found a few.
My question is, to the experts here, will I be able to fit a 13t or similar sprocket onto my motor shaft? Shaft is 5/8", with the top 1/2" as a 1/2" thread.
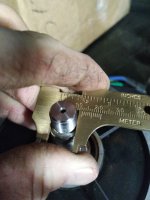
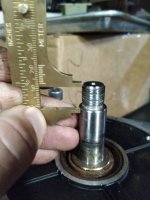
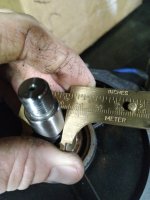
I do realize I need to figure out the correct rear sprocket size in order to not burn out my motor. But if I could get someone to chime in and tell me that it's not going to be at all possible to put a sprocket on my motor's shaft, then I don't need to waste my time with the rest of the project. I just don't even know enough about what types of sprockets are available in order for me to search for them.
Current rear sprocket, in case it helps:
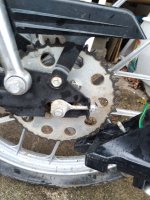
Thanks!
The issue is fitting a sprocket. I have never done this before, so I have little to know experience regarding the parts available and how to properly secure sprockets. So before I dive into the project, can someone with more experience tell me if this is at all possible? If not, that's fine, I can ditch the parts and look elsewhere. Just want to know if this is going to become too large of a bottleneck for the project to complete itself.
My goals are around 35mph top speed, it's going to be a neighborhood commuter. Rear wheel is approx 20 inches diameter. Omnicalculator tells me the rear wheel will need to spin at 588 rpm to achieve that speed, so lets call it 600. Rear sprocket is 42t. My motor's specs are hard to track down for sure, but it looks like I can expect a top rpm, loaded, of about 4000 @72v. That's top speed, meaning that I may need to find a rear sprocket with more teeth. But I've already found a few.
My question is, to the experts here, will I be able to fit a 13t or similar sprocket onto my motor shaft? Shaft is 5/8", with the top 1/2" as a 1/2" thread.
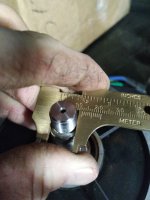
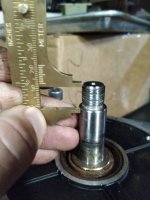
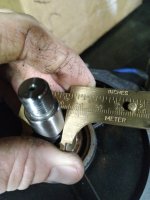
I do realize I need to figure out the correct rear sprocket size in order to not burn out my motor. But if I could get someone to chime in and tell me that it's not going to be at all possible to put a sprocket on my motor's shaft, then I don't need to waste my time with the rest of the project. I just don't even know enough about what types of sprockets are available in order for me to search for them.
Current rear sprocket, in case it helps:
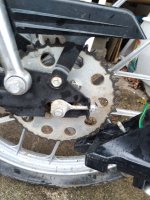
Thanks!