fourbanger
100 W
Thought I'd try something different here and ask for a bit of advice... HA!
Basically I'd like to keep both the battery and motor, maybe controller (as much stuff as I can, really) INSIDE the triangle. To accommodate this (and because I like the way they look) I'll be using an old school diamond frame MTB. I want to stick with a single stage reduction ratio for the sake of simplicity and cost, and I'm keen on driving the left side of the wheel. What else....? I'd like to keep the cost of the entire drive train (incl. motor) to under $400 CAD which is about 320 USD or so. Yeah, I know, but this is just a commuter. Speaking of which I really can't see the need for more than about 1750 peak watts, though more is always nice, less than 1200 would be a bit on the puny side for my taste. Oh yeah, regen. Love regen. Oh and one more thing; I really really don't want to piss around with finding wider BBs to accommodate all this, which basically means around 120mm OLD if it's a hub motor, or something like 5 1/2 inches wide all in.
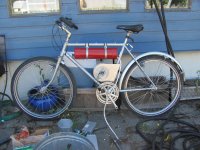
Ok, so what am I looking at again?
- motor mounted low and inside the triangle w/ enough room for battery
- single stage reduction (preferably driving LHS)
- not less than 1200W peak power
- fit between standard MTB crank arms
- regen
- no more than $320 US for motor + drivetrain
Is this all asking for a lot? Maybe. Too much? I don't really think so. Some options I've been looking at so far have been:
Soooo, yeah. That's pretty much what I've been looking at so far. One freaky alternative is that I've got an eZee front hub motor here (MAC/BMC as far as I can tell) with mushed planetaries to play with. If I were to dispense with the gears entirely and somehow affix the magnet bowl to the motor case I could get her to spin up nice and fast, then give it some (maybe) appropriate reduction ration from the outside. An even FREAKIER option would be to Crossbreak this motor in such a way that the axle spins at the full RPM of the magnet bowl and, again, do the gearing externally.
What else can I say? Grin tech. sells 16t disc mount cogs down the street for $5 CAD so that's a handy resource to exploit. Pretty sure two 3/32 cogs side by each work out to 3/16 which is what the width between internal plates of #415 chain is which, in turn, are what motorized bicycles sprockets are made at and those are cheap like borscht. Hell, maybe I could even splooge on one of those Manic Mechanic hub clamp adapter thingies to avoid the whole pineapple/rag joint thing for just that added touch of class.
Right now I'm leaning towards the scooter hub motor concept, if nothing else because of the wide variety of options out there, but I could probably be swayed in pretty much any direction. I don't know guys, that's why I'm asking. Looking forward to any questions, comments, concerns, ridicule, lore, sexual innuendos, WHATEVER YOU'VE GOT I'll take it.
Many gracious thanks, as always.
P.S.
I'll try to keep the double/triple posting to a minimum on this one, but I promise nothing.
Basically I'd like to keep both the battery and motor, maybe controller (as much stuff as I can, really) INSIDE the triangle. To accommodate this (and because I like the way they look) I'll be using an old school diamond frame MTB. I want to stick with a single stage reduction ratio for the sake of simplicity and cost, and I'm keen on driving the left side of the wheel. What else....? I'd like to keep the cost of the entire drive train (incl. motor) to under $400 CAD which is about 320 USD or so. Yeah, I know, but this is just a commuter. Speaking of which I really can't see the need for more than about 1750 peak watts, though more is always nice, less than 1200 would be a bit on the puny side for my taste. Oh yeah, regen. Love regen. Oh and one more thing; I really really don't want to piss around with finding wider BBs to accommodate all this, which basically means around 120mm OLD if it's a hub motor, or something like 5 1/2 inches wide all in.
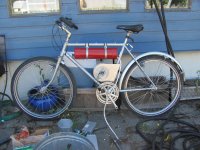
Ok, so what am I looking at again?
- motor mounted low and inside the triangle w/ enough room for battery
- single stage reduction (preferably driving LHS)
- not less than 1200W peak power
- fit between standard MTB crank arms
- regen
- no more than $320 US for motor + drivetrain
Is this all asking for a lot? Maybe. Too much? I don't really think so. Some options I've been looking at so far have been:
- GNG type motor with #25 chain to the rear wheel.
- They make something similar with a foot tacked on for easy(er) mounting, which would be nice.
- Not so sure about how to mount a #25 sprocket to the wheel (esp. LHS) but I'm pretty sure I can figure something out
- Bafang BPM or similar front wheel motor with 1:1 ratio using 16t disc mount cogs
- Requires disc hub wheel not found on the type of bicycle I'm using
- Requires welding the clutch
- Using this option it'd be really nice if I could get the wiring to exit the side of the axle... somehow
- Mini Conhis front hub motor w/ 1.75:1 reduction to LHS
- re-terminate motor winding to delta for 48v OR run at 72v (not really a huge fan of either option, really)
- 16t disc cog to 28t rag-joint sprocket
- will need venting/ferro fluid and even then I might be pushing my luck a bit far...
- Scooter hub motor w/ 16t disc cog to 44(ish?) rag joint sprocket
- most of these motors have 15 pole pairs which (according to someone somewhere) means peak eff. at 1000 or so RPM
- ummm. I think that's about it for this option. Again with wiring out the side of axle. Again with the maybe...
Soooo, yeah. That's pretty much what I've been looking at so far. One freaky alternative is that I've got an eZee front hub motor here (MAC/BMC as far as I can tell) with mushed planetaries to play with. If I were to dispense with the gears entirely and somehow affix the magnet bowl to the motor case I could get her to spin up nice and fast, then give it some (maybe) appropriate reduction ration from the outside. An even FREAKIER option would be to Crossbreak this motor in such a way that the axle spins at the full RPM of the magnet bowl and, again, do the gearing externally.
What else can I say? Grin tech. sells 16t disc mount cogs down the street for $5 CAD so that's a handy resource to exploit. Pretty sure two 3/32 cogs side by each work out to 3/16 which is what the width between internal plates of #415 chain is which, in turn, are what motorized bicycles sprockets are made at and those are cheap like borscht. Hell, maybe I could even splooge on one of those Manic Mechanic hub clamp adapter thingies to avoid the whole pineapple/rag joint thing for just that added touch of class.
Right now I'm leaning towards the scooter hub motor concept, if nothing else because of the wide variety of options out there, but I could probably be swayed in pretty much any direction. I don't know guys, that's why I'm asking. Looking forward to any questions, comments, concerns, ridicule, lore, sexual innuendos, WHATEVER YOU'VE GOT I'll take it.
Many gracious thanks, as always.
P.S.
I'll try to keep the double/triple posting to a minimum on this one, but I promise nothing.