spaceship
1 W
As the title says, I built a battery pack 13s5p using LG MH1 cells salvaged from scooter batteries. I tested each cell on a Opus battery charger (on the 1A discharge setting) and they were all showing around the 3200mAh they are rated at, so it should be a 48V 16Ah battery. I built it to run a smaller bike with a 500watt geared front hub for a friend to ride and it worked well, although we never pushed it to its limit. I recently swapped my 1500w rear hub to a full suspension bike where there is no room to mount the big 52v20Ah battery I was using before, so I decided to give this battery a try.
What I am finding though is that I am getting far less range than with my bigger battery, like less than half the range, when this battery has 3/4 the Wh. (1040wh with the 52V triangle battery vs 768 Wh with this battery). The controller starts cutting out when the battery is still showing a resting voltage of 47v, according to this chart I found there should still be some capacity left.
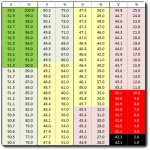
From what I understand it is voltage sag when load is applied that is causing the battery voltage to momentarily drop below my controllers low voltage cut-off, and so it shuts down. The battery is built using a 35A BMS. The MH1 cells are rated to 10A max drain, so at 35A that would be no more than 7A per cell. I tested all the salvaged cells and they all showed 95-100% their rated capacity using 1A discharge. My question is, is it just a limitation of the cells or could it be something in how I built that battery that can be improved upon (bms, nickel strip, spot welds, etc). From what I've heard these are quality cells and suitable for ebike/scooter batteries, and I dont think I am trying to pull an unreasonable amount of power from them. So is there anything I can change to get the most out of this battery?
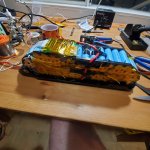
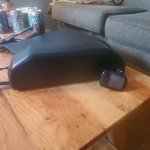
What I am finding though is that I am getting far less range than with my bigger battery, like less than half the range, when this battery has 3/4 the Wh. (1040wh with the 52V triangle battery vs 768 Wh with this battery). The controller starts cutting out when the battery is still showing a resting voltage of 47v, according to this chart I found there should still be some capacity left.
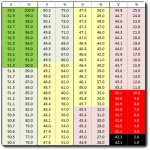
From what I understand it is voltage sag when load is applied that is causing the battery voltage to momentarily drop below my controllers low voltage cut-off, and so it shuts down. The battery is built using a 35A BMS. The MH1 cells are rated to 10A max drain, so at 35A that would be no more than 7A per cell. I tested all the salvaged cells and they all showed 95-100% their rated capacity using 1A discharge. My question is, is it just a limitation of the cells or could it be something in how I built that battery that can be improved upon (bms, nickel strip, spot welds, etc). From what I've heard these are quality cells and suitable for ebike/scooter batteries, and I dont think I am trying to pull an unreasonable amount of power from them. So is there anything I can change to get the most out of this battery?
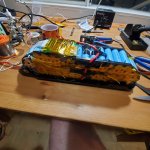
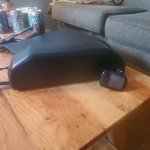