electroneg
10 µW
- Joined
- Aug 16, 2021
- Messages
- 5
Hi All,
Great forum you have here, I've been reading through a number of threads on here and seems a great source of information and help.
My name is Dale and I live in a small country in the UK called Wales.
I'm an Electronics/Industrial electrical engineer by trade.
I've just started using LiFePo4 batteries and would like to find out more about them and how to make sure I'm getting the most out of them and interested in charging and testing in detail.
My use case for them is a bit mixed, I'm a Radio Amateur so I like to operate my equipment portable. That varies so I take different size batteries with me depending on what I'm doing. From being near the car to being at the top of a mountain.
We are also avid campers so enjoy breaks away in the tent and ideally like to go to quieter more remote locations that tend not to have mains hookup so planning on taking some LiFePo4 batteries with us.
So far I've bought a number of batteries with built in BMS's and I also have some cells I've salvaged from jump starter packs.
Out of the 4x "12.8V" Batteries I've bought with built in BMS unit's I've noticed something happening with them all fresh out of the box.
3x Of these batteries are the same, "12.8V"/ 8Ah and another is a different brand and capacity, that is a "12.8V" / 22Ah (24Ah Nominal)
With the 3x identical batteries I charged each one individually using one of my Bench Power Supplies, I set the current limit to 2A and Voltage to 14.6V
everything seems good through the CC bulk phase, but as soon as the current goes down and it starts approaching 14.6V in CV mode the BMS will disconnect the cells, so one or more cells are hitting the limit causing the BMS to disconnect. This has varied between 14.4V - 14.6V between these batteries.
So I'm only getting seconds on the CV stage before the BMS disconnects the cells which I'm not fond of.
I discharged all 3 of the batteries, left them for a while and recharged them using one of my Bench PSU's, this time I set the Voltage to 14.4V and the Current limiting to 2A and charged them all individually again (I have 5 or more CC/CV PSUs here) again they went through the bulk stage no problem and then the current started tapering off nicely as they approached 14.4V and at 14.4V there was a current draw of approx 80mA, so gradually I increased the voltage on the bench PSU up by .5V at a time watching the current rise then settle to 80mA and so on. I carried on doing this on all 3 batteries till I got to 14.6V and now the BMS is not disconnecting the batteries and will sit there indefinitely (Only left so far for an hour or so to check) and eventually drop to 20-40mA (I assume this is the quiescent current of the BMS?) I pushed the PSU up to 14.62 and it's fine there as well so a little bit of headroom before the BMS disconnects (I took the PSU up a bit higher momentarily to see if the HV disconnect is working and it does disconnect at a higher voltage)
So far so good I'm thinking, 2 of those batteries I've discharged to a safe limit then recharged with the PSU at 14.6V 2A and the BMS has stopped disconnecting, so I'm wondering if by doing that step in the previous charge by gradually increasing the current has allowed the cells to balance somewhat?
Now on to the 4th battery, the "12.8V" 22Ah (24Ah Nominal)
This came supplied with a 14.6V / 3A "LiFePo4" CC/CV charger so I thought let's just use this charger and see how it goes!
I checked the voltage on the battery to see the SOC that it arrived with and I can't quite remember the actual voltage but I think it was around 13.4V or 13.5V
I connected checked the output of the PSU with a multimeter and it is 14.61V exactly. I connected the charger to the battery and had the multimeter connected at the battery terminals to watch the charge voltage and monitor it's progress.
With this charger it states the LED is Red when current is >200mA (CC Mode) and Green when <200mA.
After a few hours, the LED went Green and the Multimeter was showing 14.61V with both the battery and the charger connected.
Great I thought, lets leave it a few more minutes and see if the supplied charger has a shut off and I should see the voltage on the multimeter drop to the SOC Voltage of the battery.
While I was watching I did notice after a few minutes the voltage dropped on the multimer to just below 14V, but it was not the charger switching off, it was the BMS reconnecting the cells as the LED on the charger went Red again and after about 30 seconds turn green.
I got some more test equipment out and could see it was exactly what I thought was happening, if left the BMS would disconnect and then reconnect as the voltage has dropped on one of the cells. I'm not sure whether this would sort itself out or not eventually but I didn't like it.
I took the battery off charge left it for a while then discharged it to start again, this time I put it on my ISDT Q8 so I could get a rough idea of how much current approximately the battery had taken (I know this is very approximate) but I wanted a rough idea to see whether it would take the full 22Ah and would be concerned if that figure was a lot less than that. The ISDT Q8 was set to 4S LiFePo4 (3.65V) 3A Unbalanced as I was just using the battery terminals.
I let that run for some time and kept popping in to monitor it's progress, it did the bulk charge and said the battery had taken about 23.2Ah, so that was partially reassuring. As mentioned if it had taken a less or a lot less I'd be quite concerned.
Then the ISDT Q8 switched over the CV mode as the current had dropped off and the battery was very near 14.6V, then I heard a beep and it had stopped, it was only in this mode for 30 seconds or so, just like it did on the supplied charger.
I then noticed the 23.2Ah measurement had disappeared off the Q8 LCD, which means one thing. The BMS had disconnected and not the Q8 terminating the charge.
So I let things settle for a while and checked the battery resting SOC which was around 13.6-13.7V
I put the battery on my TTI TSX3510 PSU and set the voltage to 14.6V 3A and waited to see what happened. The BMS disconnected the cells, I worked backwards to see where it was disconnecting and it seemed to be around 14.5V. So leaving things settle again for a while I started off at 14.4V waited for the current to drop, then increased it by .5V then worked my way up to 14.6V as the current dropped on each increment, it now went up to 14.6V without the BMS disconnecting the cells. I took it up a little higher and all was fine and the HV disconnect was working correctly.
I discharged the battery a bit and left it, then put it back on the supplied charger and that BMS disconnecting loop has stopped.
I left it there for some time with a pair of multimeters monitoring current and voltage for about an hour, I've just switched it off now as I didn't want to leave it too long, the current draw was 60mA and voltage was 14.61V - I'm honestly not sure how long you should leave a LiFePo4 battery with a BMS at that voltage (or any voltage) with a very small current draw. Is this safe to leave or will that cause damage when there is only 20-60mA current being drawn as the batteries are being held at 3.65V/Cell? I know some/all of that current will be the BMS I'm assuming.
My concern are 2 things, the BMS disconnect loop (I hope this has stopped for good now, but I will discharge and re-charge to check) is this something anyone else has come across and does it just sort itself out if left? And this supplied charger will sit there in CV mode indefinitely, is this <60mA current draw and batteries being held at 14.6V harmful at all? One of the reasons for buying this battery was the supplied charger that I can use for my other batteries. I just wanted to make it easier to put a battery on charge without cluttering my workbench, overnight charge or if I'm out. I assumed (Maybe wrongly) that it will turn off when the current draw was at a certain level.
Obviously It's the same situation if I use one of my lab CC/CV power supplies, any of the batteries will sit there indefinitely with a very low current draw of <30mA @ 14.6V and I'm not sure if it's doing any harm to them.
Being an electronics engineer I'm really curious about how this all works and find it fascinating, I'm not one to just plug something in and forget about it so I like to check things over and also build my own equipment. We are also moving house and I will be putting all my radio equipment in an outbuilding and want to build a battery bank to harvest some energy. Not to mention hopefully building a camper van and plan on putting some batteries in there too.
Just for some clarity, all the equipment here is calibrated, the power supplies and multimeters etc. So there is no discrepancy regarding measurements that I have mentioned between any of the equipment I have been using.
I'm going to buy an Electronic load with Ah/Wh etc so I can get a rough idea of the total capacity of my batteries from a discharge, probably one of those generic 150w/180w units that seem quite popular.
I do have an electronic load that I use for repairing and testing power supplies, but that has no form of accumulated energy/power reading. It just a simple FET based load with V/A meters.
Apologies for the essay, lots to ask and write about and I really do appreciate you taking your time to read this and look forward to reading your replies.
Sorry more questions, what is a healthy ideal 100% SOC Resting Voltage range for a "12.8V" LiFePo4 Pack as I keep finding conflicting information?
And when does a BMS start balancing?
Attached are some pictures of the 22aH battery with the 2 multimeters with the charger sat there at 14.6V and batteries taking ~70mA.
Also a picture of my messy workbench with a small selection of some of my CC/CV Lab PSU's
Dale
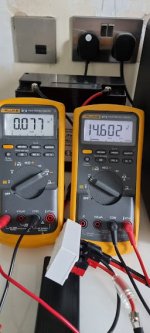
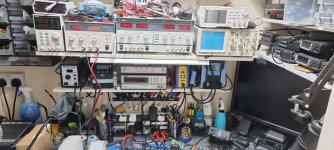
Great forum you have here, I've been reading through a number of threads on here and seems a great source of information and help.
My name is Dale and I live in a small country in the UK called Wales.
I'm an Electronics/Industrial electrical engineer by trade.
I've just started using LiFePo4 batteries and would like to find out more about them and how to make sure I'm getting the most out of them and interested in charging and testing in detail.
My use case for them is a bit mixed, I'm a Radio Amateur so I like to operate my equipment portable. That varies so I take different size batteries with me depending on what I'm doing. From being near the car to being at the top of a mountain.
We are also avid campers so enjoy breaks away in the tent and ideally like to go to quieter more remote locations that tend not to have mains hookup so planning on taking some LiFePo4 batteries with us.
So far I've bought a number of batteries with built in BMS's and I also have some cells I've salvaged from jump starter packs.
Out of the 4x "12.8V" Batteries I've bought with built in BMS unit's I've noticed something happening with them all fresh out of the box.
3x Of these batteries are the same, "12.8V"/ 8Ah and another is a different brand and capacity, that is a "12.8V" / 22Ah (24Ah Nominal)
With the 3x identical batteries I charged each one individually using one of my Bench Power Supplies, I set the current limit to 2A and Voltage to 14.6V
everything seems good through the CC bulk phase, but as soon as the current goes down and it starts approaching 14.6V in CV mode the BMS will disconnect the cells, so one or more cells are hitting the limit causing the BMS to disconnect. This has varied between 14.4V - 14.6V between these batteries.
So I'm only getting seconds on the CV stage before the BMS disconnects the cells which I'm not fond of.
I discharged all 3 of the batteries, left them for a while and recharged them using one of my Bench PSU's, this time I set the Voltage to 14.4V and the Current limiting to 2A and charged them all individually again (I have 5 or more CC/CV PSUs here) again they went through the bulk stage no problem and then the current started tapering off nicely as they approached 14.4V and at 14.4V there was a current draw of approx 80mA, so gradually I increased the voltage on the bench PSU up by .5V at a time watching the current rise then settle to 80mA and so on. I carried on doing this on all 3 batteries till I got to 14.6V and now the BMS is not disconnecting the batteries and will sit there indefinitely (Only left so far for an hour or so to check) and eventually drop to 20-40mA (I assume this is the quiescent current of the BMS?) I pushed the PSU up to 14.62 and it's fine there as well so a little bit of headroom before the BMS disconnects (I took the PSU up a bit higher momentarily to see if the HV disconnect is working and it does disconnect at a higher voltage)
So far so good I'm thinking, 2 of those batteries I've discharged to a safe limit then recharged with the PSU at 14.6V 2A and the BMS has stopped disconnecting, so I'm wondering if by doing that step in the previous charge by gradually increasing the current has allowed the cells to balance somewhat?
Now on to the 4th battery, the "12.8V" 22Ah (24Ah Nominal)
This came supplied with a 14.6V / 3A "LiFePo4" CC/CV charger so I thought let's just use this charger and see how it goes!
I checked the voltage on the battery to see the SOC that it arrived with and I can't quite remember the actual voltage but I think it was around 13.4V or 13.5V
I connected checked the output of the PSU with a multimeter and it is 14.61V exactly. I connected the charger to the battery and had the multimeter connected at the battery terminals to watch the charge voltage and monitor it's progress.
With this charger it states the LED is Red when current is >200mA (CC Mode) and Green when <200mA.
After a few hours, the LED went Green and the Multimeter was showing 14.61V with both the battery and the charger connected.
Great I thought, lets leave it a few more minutes and see if the supplied charger has a shut off and I should see the voltage on the multimeter drop to the SOC Voltage of the battery.
While I was watching I did notice after a few minutes the voltage dropped on the multimer to just below 14V, but it was not the charger switching off, it was the BMS reconnecting the cells as the LED on the charger went Red again and after about 30 seconds turn green.
I got some more test equipment out and could see it was exactly what I thought was happening, if left the BMS would disconnect and then reconnect as the voltage has dropped on one of the cells. I'm not sure whether this would sort itself out or not eventually but I didn't like it.
I took the battery off charge left it for a while then discharged it to start again, this time I put it on my ISDT Q8 so I could get a rough idea of how much current approximately the battery had taken (I know this is very approximate) but I wanted a rough idea to see whether it would take the full 22Ah and would be concerned if that figure was a lot less than that. The ISDT Q8 was set to 4S LiFePo4 (3.65V) 3A Unbalanced as I was just using the battery terminals.
I let that run for some time and kept popping in to monitor it's progress, it did the bulk charge and said the battery had taken about 23.2Ah, so that was partially reassuring. As mentioned if it had taken a less or a lot less I'd be quite concerned.
Then the ISDT Q8 switched over the CV mode as the current had dropped off and the battery was very near 14.6V, then I heard a beep and it had stopped, it was only in this mode for 30 seconds or so, just like it did on the supplied charger.
I then noticed the 23.2Ah measurement had disappeared off the Q8 LCD, which means one thing. The BMS had disconnected and not the Q8 terminating the charge.
So I let things settle for a while and checked the battery resting SOC which was around 13.6-13.7V
I put the battery on my TTI TSX3510 PSU and set the voltage to 14.6V 3A and waited to see what happened. The BMS disconnected the cells, I worked backwards to see where it was disconnecting and it seemed to be around 14.5V. So leaving things settle again for a while I started off at 14.4V waited for the current to drop, then increased it by .5V then worked my way up to 14.6V as the current dropped on each increment, it now went up to 14.6V without the BMS disconnecting the cells. I took it up a little higher and all was fine and the HV disconnect was working correctly.
I discharged the battery a bit and left it, then put it back on the supplied charger and that BMS disconnecting loop has stopped.
I left it there for some time with a pair of multimeters monitoring current and voltage for about an hour, I've just switched it off now as I didn't want to leave it too long, the current draw was 60mA and voltage was 14.61V - I'm honestly not sure how long you should leave a LiFePo4 battery with a BMS at that voltage (or any voltage) with a very small current draw. Is this safe to leave or will that cause damage when there is only 20-60mA current being drawn as the batteries are being held at 3.65V/Cell? I know some/all of that current will be the BMS I'm assuming.
My concern are 2 things, the BMS disconnect loop (I hope this has stopped for good now, but I will discharge and re-charge to check) is this something anyone else has come across and does it just sort itself out if left? And this supplied charger will sit there in CV mode indefinitely, is this <60mA current draw and batteries being held at 14.6V harmful at all? One of the reasons for buying this battery was the supplied charger that I can use for my other batteries. I just wanted to make it easier to put a battery on charge without cluttering my workbench, overnight charge or if I'm out. I assumed (Maybe wrongly) that it will turn off when the current draw was at a certain level.
Obviously It's the same situation if I use one of my lab CC/CV power supplies, any of the batteries will sit there indefinitely with a very low current draw of <30mA @ 14.6V and I'm not sure if it's doing any harm to them.
Being an electronics engineer I'm really curious about how this all works and find it fascinating, I'm not one to just plug something in and forget about it so I like to check things over and also build my own equipment. We are also moving house and I will be putting all my radio equipment in an outbuilding and want to build a battery bank to harvest some energy. Not to mention hopefully building a camper van and plan on putting some batteries in there too.
Just for some clarity, all the equipment here is calibrated, the power supplies and multimeters etc. So there is no discrepancy regarding measurements that I have mentioned between any of the equipment I have been using.
I'm going to buy an Electronic load with Ah/Wh etc so I can get a rough idea of the total capacity of my batteries from a discharge, probably one of those generic 150w/180w units that seem quite popular.
I do have an electronic load that I use for repairing and testing power supplies, but that has no form of accumulated energy/power reading. It just a simple FET based load with V/A meters.
Apologies for the essay, lots to ask and write about and I really do appreciate you taking your time to read this and look forward to reading your replies.
Sorry more questions, what is a healthy ideal 100% SOC Resting Voltage range for a "12.8V" LiFePo4 Pack as I keep finding conflicting information?
And when does a BMS start balancing?
Attached are some pictures of the 22aH battery with the 2 multimeters with the charger sat there at 14.6V and batteries taking ~70mA.
Also a picture of my messy workbench with a small selection of some of my CC/CV Lab PSU's
Dale
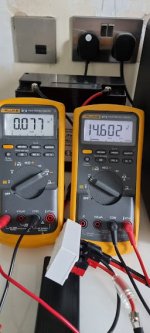
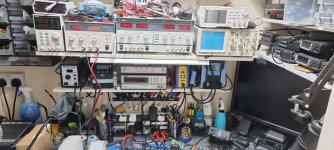