jonescg
100 MW
Hi Guys,
Can you please check something? The new TTXGP rules state that when the emergency stop button is hit, the high voltage system (i.e. the battery pack) should be completely isolated from the rest of the bike. Leaving a precharge resistor permanently wired across the main contactor terminals isn't good enough - it has to be disconnected too. So this means a N.O. relay will have to be used to close the precharge resistor circuit. Not sure what voltage these SPST relays are rated to, but 110 V might be pushing it, even with a big 200 ohm resistor.
I figure the first stop on my ignition key switch is good for this. BUT, how do I stop myself from belting right through to ON when the capacitors in the controller haven't charged up yet? I found a simple delay circuit which activates a SPST relay after about 7 seconds. I can then use the 12 V supplied to the delay circuit to run the main contactor circuit.
Finally, when the bike is switched off again, both the main contactor will go open circuit, and the precharge resistor circuit will go open circuit as I click right back to the OFF position. This leaves the capacitors in the controller still fully charged, but if I were to use the other pole of a SPST relay to run the same precharge resistor across the B+ and B- of the controller, it should discharge them.
Most importanly, can anyone see a glaring error in my schematic? Like 110 V worth of battery connection going through a tiny relay? Do you think the delay circuit will even work?
CHRIS
Can you please check something? The new TTXGP rules state that when the emergency stop button is hit, the high voltage system (i.e. the battery pack) should be completely isolated from the rest of the bike. Leaving a precharge resistor permanently wired across the main contactor terminals isn't good enough - it has to be disconnected too. So this means a N.O. relay will have to be used to close the precharge resistor circuit. Not sure what voltage these SPST relays are rated to, but 110 V might be pushing it, even with a big 200 ohm resistor.
I figure the first stop on my ignition key switch is good for this. BUT, how do I stop myself from belting right through to ON when the capacitors in the controller haven't charged up yet? I found a simple delay circuit which activates a SPST relay after about 7 seconds. I can then use the 12 V supplied to the delay circuit to run the main contactor circuit.
Finally, when the bike is switched off again, both the main contactor will go open circuit, and the precharge resistor circuit will go open circuit as I click right back to the OFF position. This leaves the capacitors in the controller still fully charged, but if I were to use the other pole of a SPST relay to run the same precharge resistor across the B+ and B- of the controller, it should discharge them.
Most importanly, can anyone see a glaring error in my schematic? Like 110 V worth of battery connection going through a tiny relay? Do you think the delay circuit will even work?
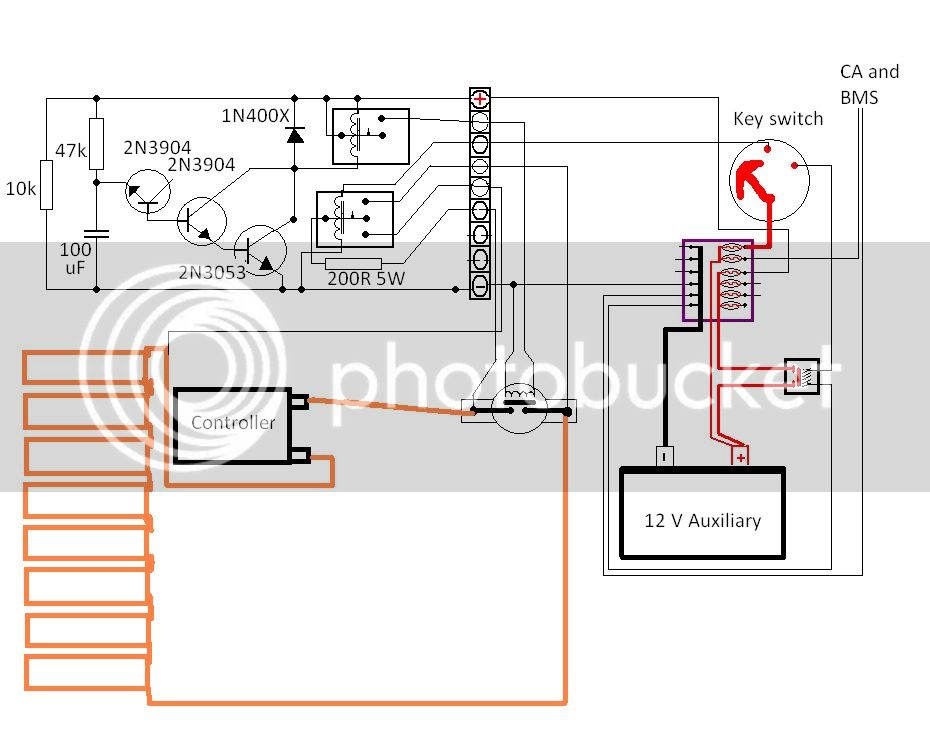