JCG
100 W
- Joined
- Nov 10, 2008
- Messages
- 174
I've spent the last couple of months building a trike that could be considered on some level as a scale model of a series hybrid car - a separate project that I mentioned a few times before. So here's the full build thread, all in one post. I hope this fits without breaking it into smaller pieces.
Ok, the frame for the conversion is a KMX Tornado (~40 lbs, welded steel).
It is a strong frame, has a lot of available space:
and the square-section members are absolutely great for mounting things.
I got the trike from FFR, and I must say it was a great transaction - thanks very much Tom (VRdublove). I highly recommend these guys.
Since this was to be a series hybrid, the first step was to eliminate any direct link from the pedals to the wheel. A great thing about the KMX trike is the solid "bash ring" on the crank. It is of course set up for normal width bike chain:
I put washers in to space the bash ring from the crank sprocket...
And it was ready to accept heavier-duty ANSI 40 roller chain, which has the same half inch pitch (link spacing) as normal bike chain, but is wider.
I mounted a WindBlue permanent magnet alternator to the crank boom, and this will allow pedaling to deliver energy to the electrical storage system.
There is a charge controller as well, which prevents pedaling from overcharging the system. Not that I'm worried about that.
The entire storage system is 12 VDC. This allows for a lot of fun accessories, but most important are lights:
And of course you need GPS.
I also have a voltmeter "fuel gauge" on the front which I can look down to see, and the Cycle Analyst on the left hand steer bar.
Now, about the motor. This is the critical part from a design perspective. Here, you can see I've mounted a 2 hp induction motor (50 lbs) behind the seat. It is rated for 6 ft-lbs of torque and 1740 rpm at 60 Hz operation. It is wired for 230 VAC, 3-phase input.
The electronics for the motor (controller and power supply) are located right behind it. Here, you can see my shunt resistor along with the inverter 12V leads, and the three motor phase wires. It is so nice to not have to deal with hall effect stuff... wiring was simplicity itself.
Here's a better view of those electronics, stored in the rear basket on the driver's left hand side. The light blue plastic box is a Hitachi 3 HP motor controller (capable of up to 10 phase amps at 230 V), and the blue aluminum-cased unit is the 12 VDC to 240 VAC (single phase) power inverter. It is capable of 1500 W continuous. The little black boxes behind there are small 12V AGM batteries (in series). Their only job is to power the Cycle Analyst.
On the right hand side, we have a 12 V AGM battery, 35 Ah. One set of leads goes to the inverter, the other to the 12 V buses.
To multiply the torque to get acceptable acceleration and hill climbing, I placed a 60 tooth sprocket on the freewheel hub. Thanks to DrunkSkunk for that idea.
With an 11 tooth front sprocket,
torque is multiplied by around 5.45. Rated torque is 6 ft-lbs, but 150% (9 ft-lbs) is available at locked-rotor (dead stop):
So I'll get about 9 * 5.45 = 49 ft-lbs at a dead stop, which matches pretty well with my old BLDC hub motor. Top speed suffers, and at 60 Hz my 1740 rpm gets cut to 319 rpm at the wheel, so I extended the controller's frequency range to 100 Hz to boost the top speed from 20 mph to 33. You pay for that speed with some torque loss in the "field weakening" regime of course. I'll keep an eye on the speed with the Cycle Analyst.
I'm sure everyone saw the ANSI 40 chain on the rear two sprockets as well. Here's something I made that I'm kind of proud of - a threaded bolt-adjustable chain tensioner:
It allows me to get the chain tension just right without needing half links or scooting the motor around on its mounts. The terminal block allows you to access the + and - 12V buses as well as the Cycle Analyst electronics. Here, you see 7 +12VDC slots, 6 Cycle Analyst Slots, and 7 -12VDC slots from left to right. The missing two CA ports are for USB data collection. The plugs are for the lights and to disconnect the CA.
I have a (currently) hand-held throttle potentiometer (0 to 10 V signal) to control the motor speed remotely. I may mount this in the future.
Here's the overall product.
Some video: first, a spinup of the motor (effective 0 - 33 mph wheel speed)
[youtube]jPmKgRxWWnA[/youtube]
The same thing with a view of the motor phase current displayed by the controller. There's a decimal point between the digits.
[youtube]pdER4Bg16CA[/youtube]
I think about the present arrangement as the trike's "city mode," with probably lots of range, but relying heavily on the battery. This is the configuration I'm using for initial tests. When it is outfitted in "cross-country mode," imagine the following. First, replace the 12 V battery with three 16 V, 330 F ultracapacitor modules ganged in parallel for a 16 V, 990 F combination, which still fits in the right-hand rear basket:
That will be the electrical storage buffer. I'll have a rear trailer, the same one as the other bike had, to carry a small 900 W generator (25 lbs) and a battery charger, which can send up to 30 A to maintain 13.5 V over the DC storage system.
The generator runs for 12 hours on one quarter load (~225 W) using two thirds of a gallon of gasoline. The entire electronics system is 93% or better efficiency throughout, and the motor has an 84% efficiency at its rated load. If I run 25 mph at that power draw, that's close to 450 mpg. Pedaling could help that number too, I guess.
So, that's it. The AC motor has a lot of advantages; cheap, long life, easy control, good high-speed torque, no power drop at high speed. Thanks to safe for posting this plot in his thread on a separate board (and thanks for the brainstorming, too):
Link to MotoredBikes Thread
If you can handle the additional weight and space for the AC motor, it's a nice option. Safety is nice, too; although this system has some high voltages inside of it, the only voltage a user might possibly touch is 12 VDC. Not bad.
Ok, the frame for the conversion is a KMX Tornado (~40 lbs, welded steel).
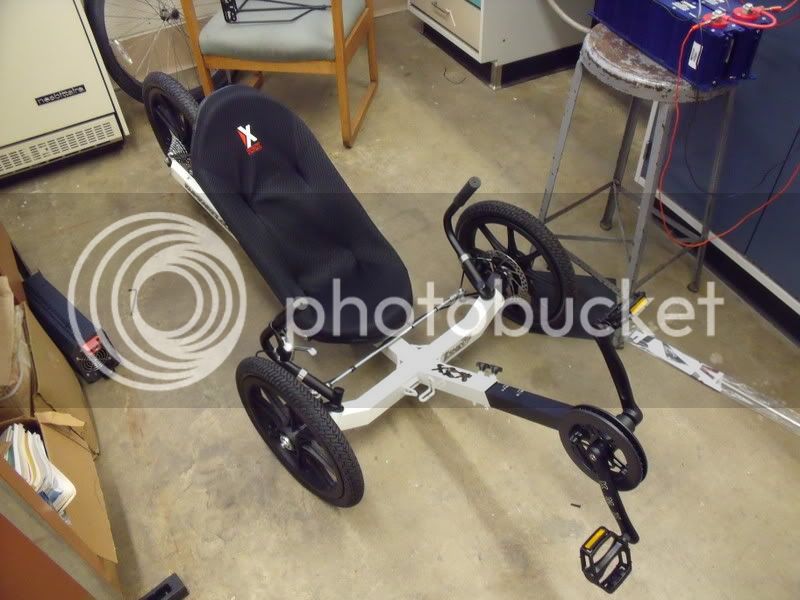
It is a strong frame, has a lot of available space:
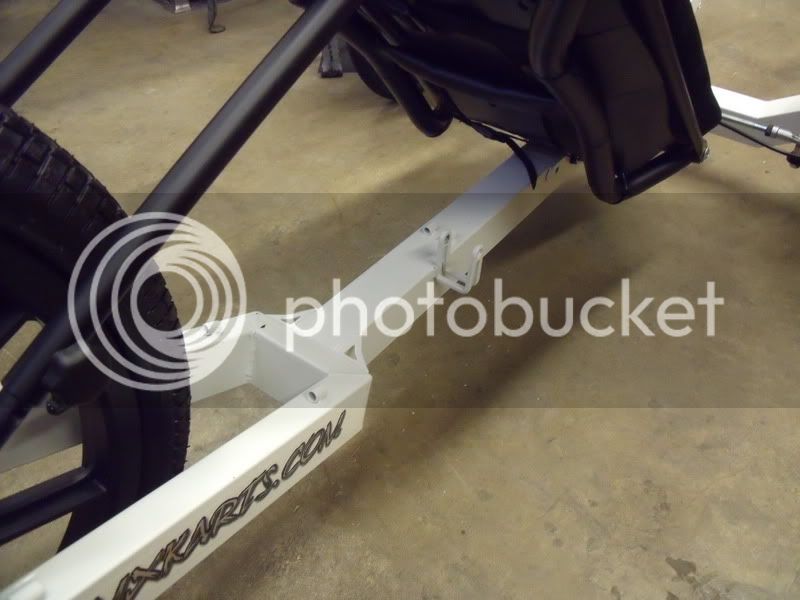
and the square-section members are absolutely great for mounting things.
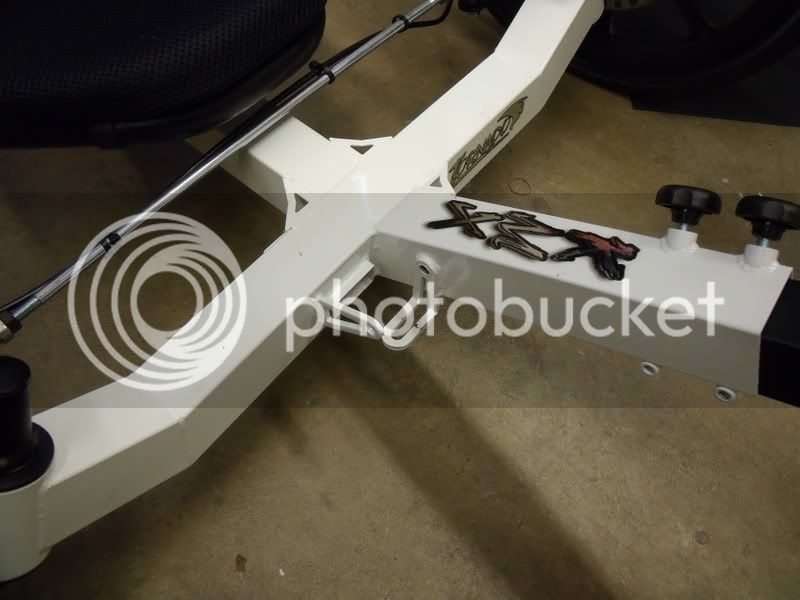
I got the trike from FFR, and I must say it was a great transaction - thanks very much Tom (VRdublove). I highly recommend these guys.
Since this was to be a series hybrid, the first step was to eliminate any direct link from the pedals to the wheel. A great thing about the KMX trike is the solid "bash ring" on the crank. It is of course set up for normal width bike chain:
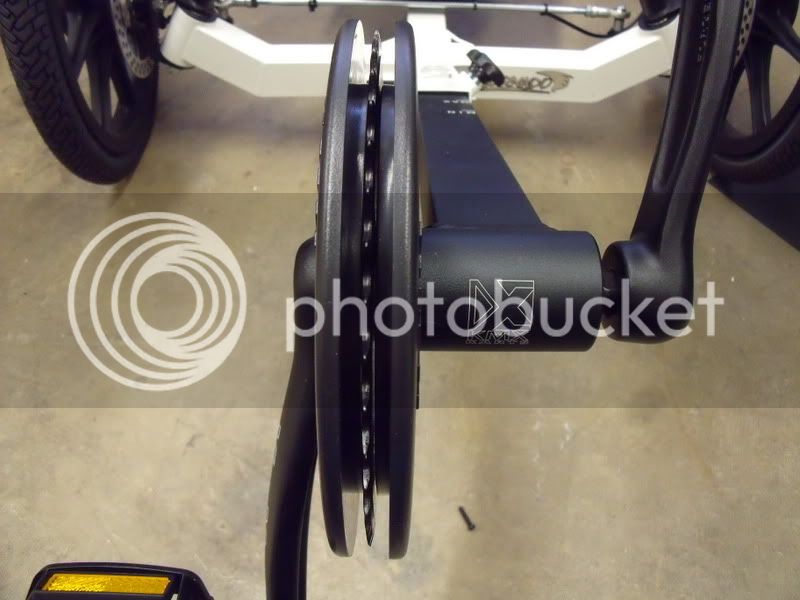
I put washers in to space the bash ring from the crank sprocket...
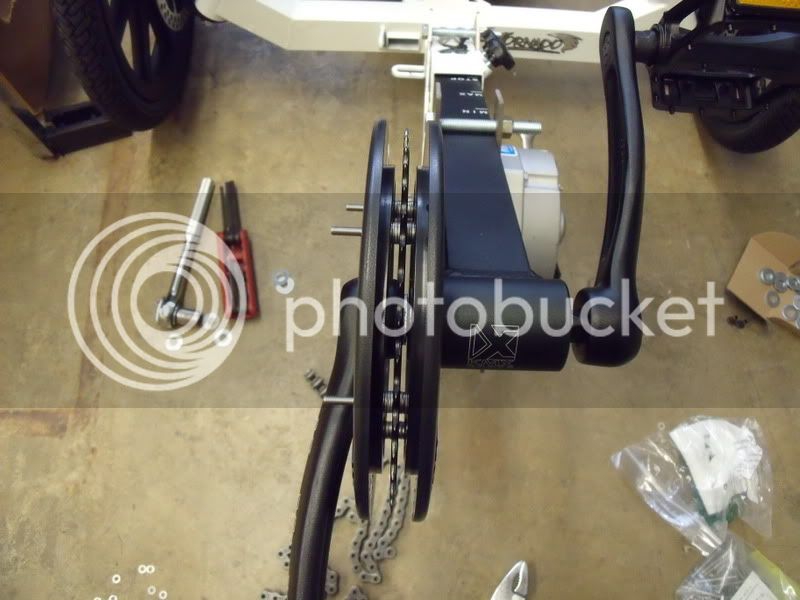
And it was ready to accept heavier-duty ANSI 40 roller chain, which has the same half inch pitch (link spacing) as normal bike chain, but is wider.
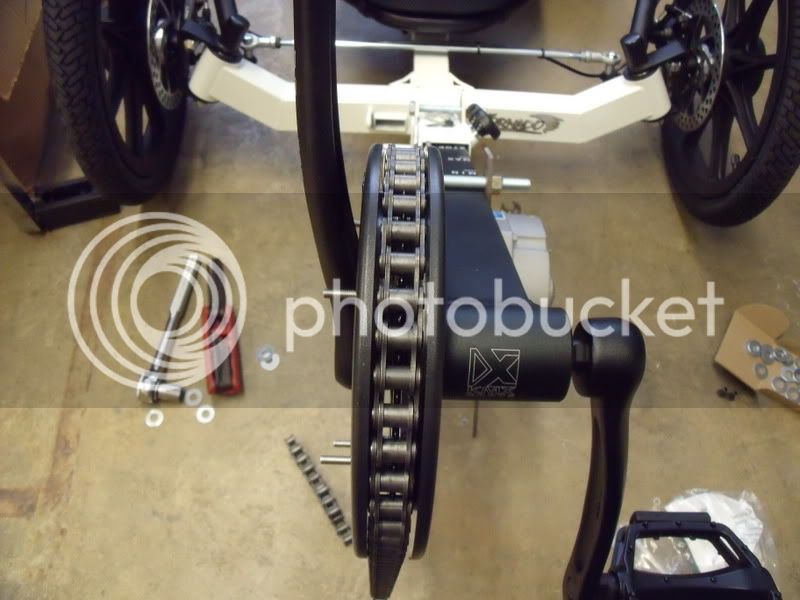
I mounted a WindBlue permanent magnet alternator to the crank boom, and this will allow pedaling to deliver energy to the electrical storage system.
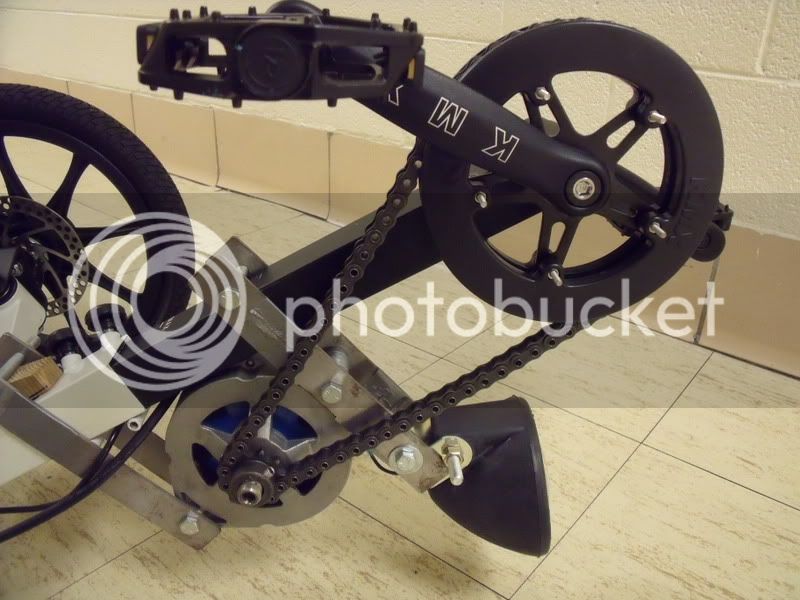
There is a charge controller as well, which prevents pedaling from overcharging the system. Not that I'm worried about that.

The entire storage system is 12 VDC. This allows for a lot of fun accessories, but most important are lights:
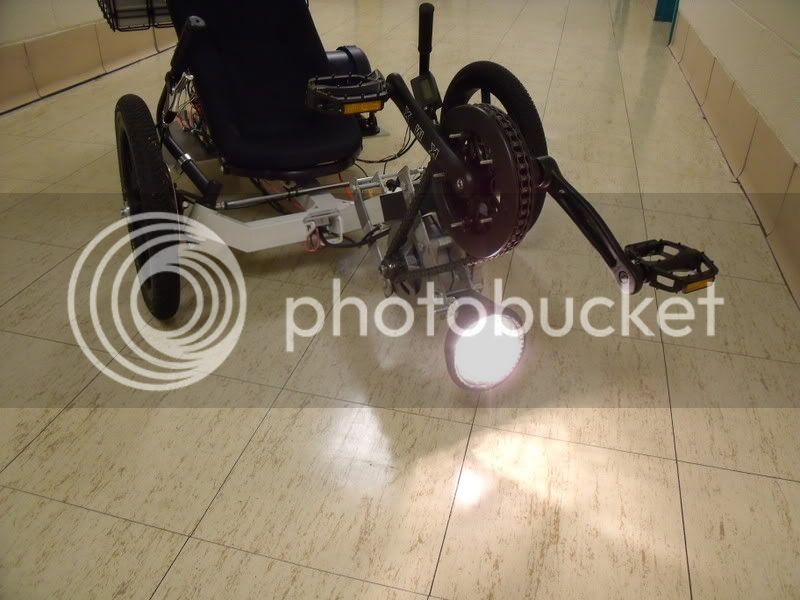
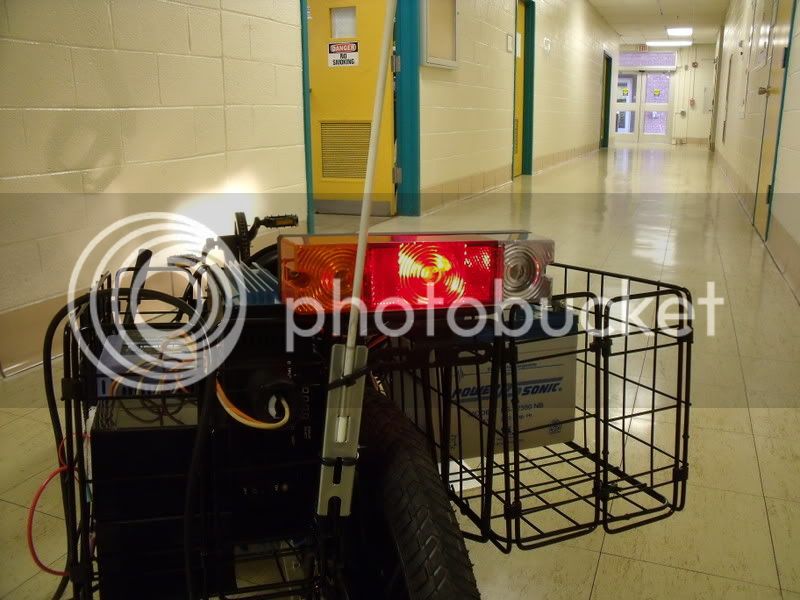
And of course you need GPS.
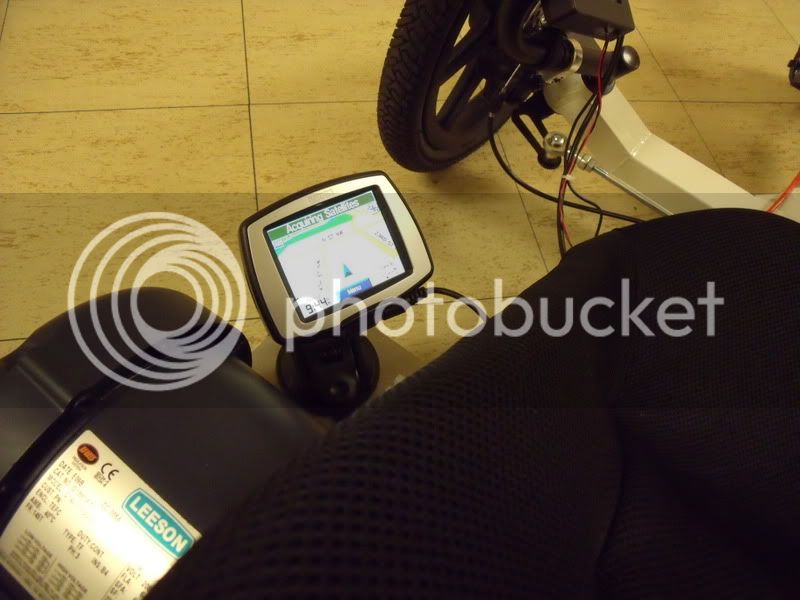
I also have a voltmeter "fuel gauge" on the front which I can look down to see, and the Cycle Analyst on the left hand steer bar.
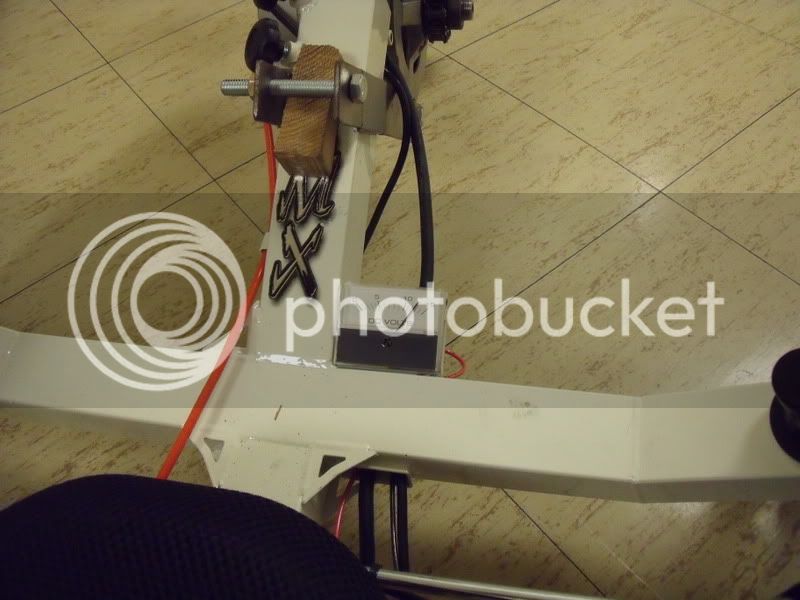
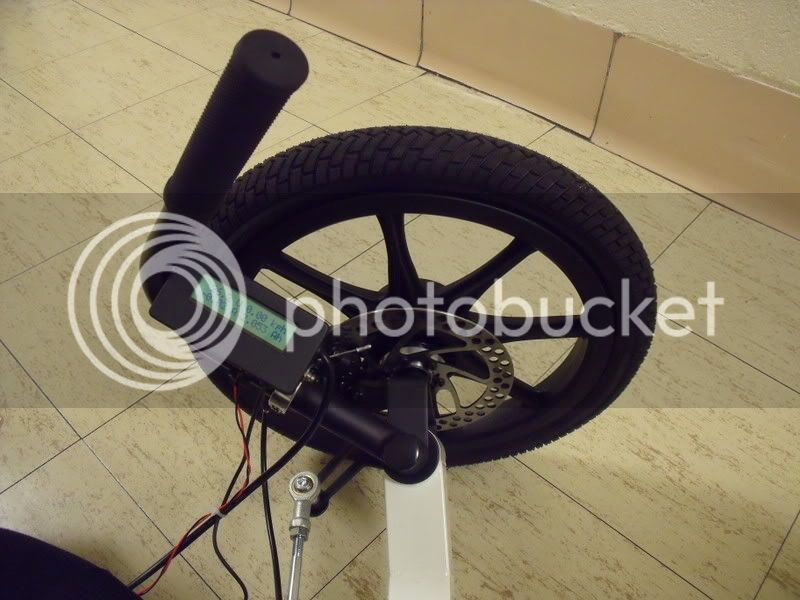
Now, about the motor. This is the critical part from a design perspective. Here, you can see I've mounted a 2 hp induction motor (50 lbs) behind the seat. It is rated for 6 ft-lbs of torque and 1740 rpm at 60 Hz operation. It is wired for 230 VAC, 3-phase input.
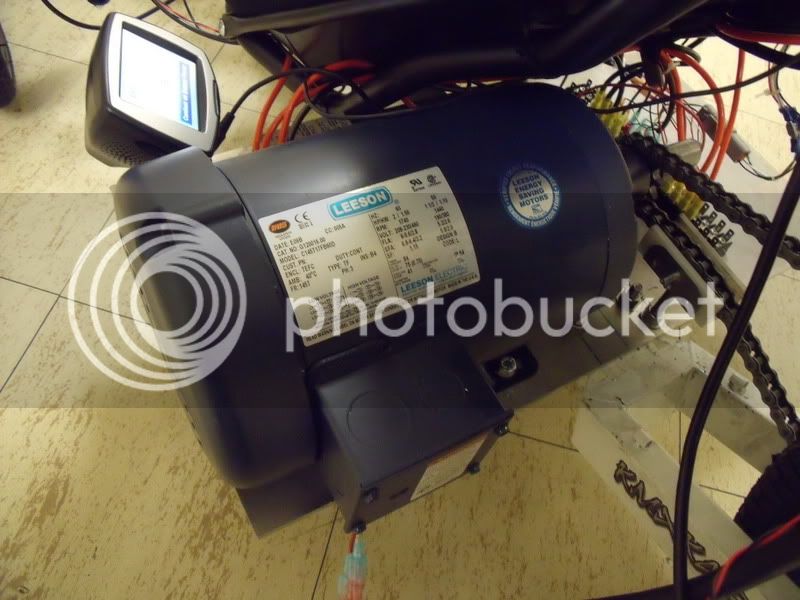
The electronics for the motor (controller and power supply) are located right behind it. Here, you can see my shunt resistor along with the inverter 12V leads, and the three motor phase wires. It is so nice to not have to deal with hall effect stuff... wiring was simplicity itself.
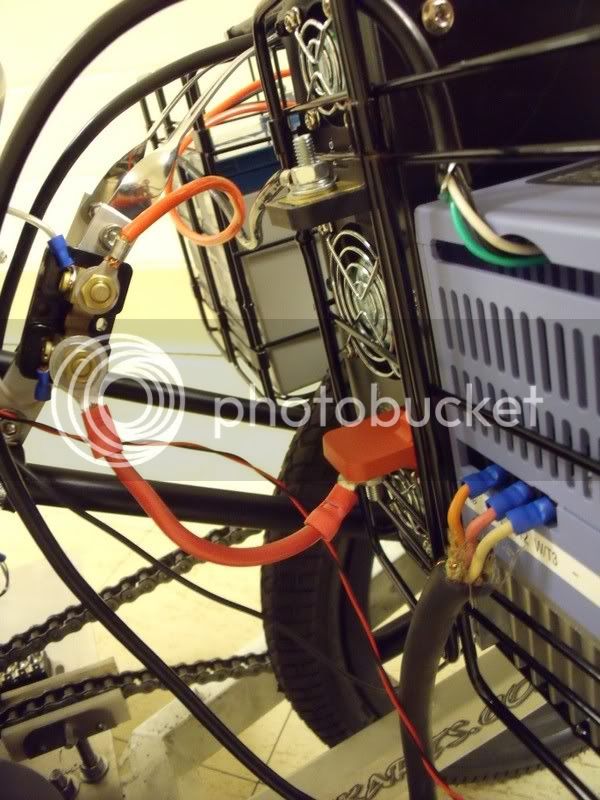
Here's a better view of those electronics, stored in the rear basket on the driver's left hand side. The light blue plastic box is a Hitachi 3 HP motor controller (capable of up to 10 phase amps at 230 V), and the blue aluminum-cased unit is the 12 VDC to 240 VAC (single phase) power inverter. It is capable of 1500 W continuous. The little black boxes behind there are small 12V AGM batteries (in series). Their only job is to power the Cycle Analyst.
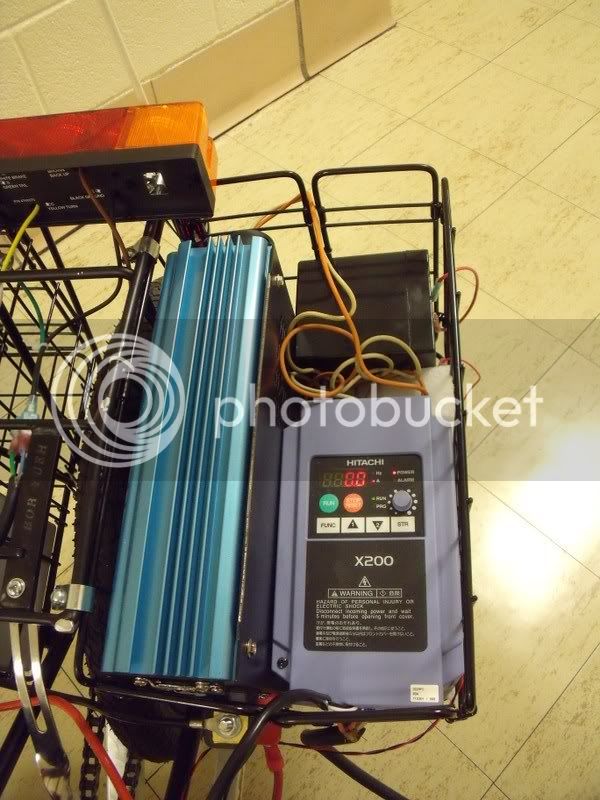
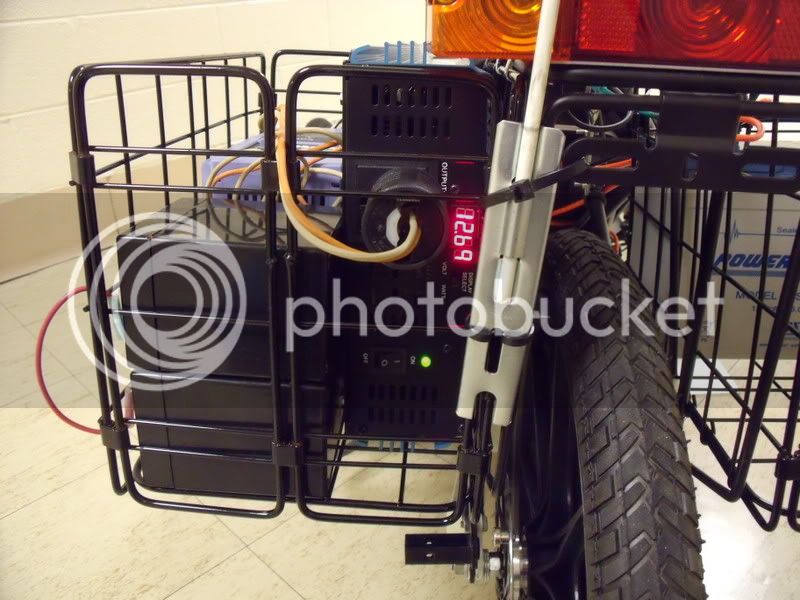
On the right hand side, we have a 12 V AGM battery, 35 Ah. One set of leads goes to the inverter, the other to the 12 V buses.
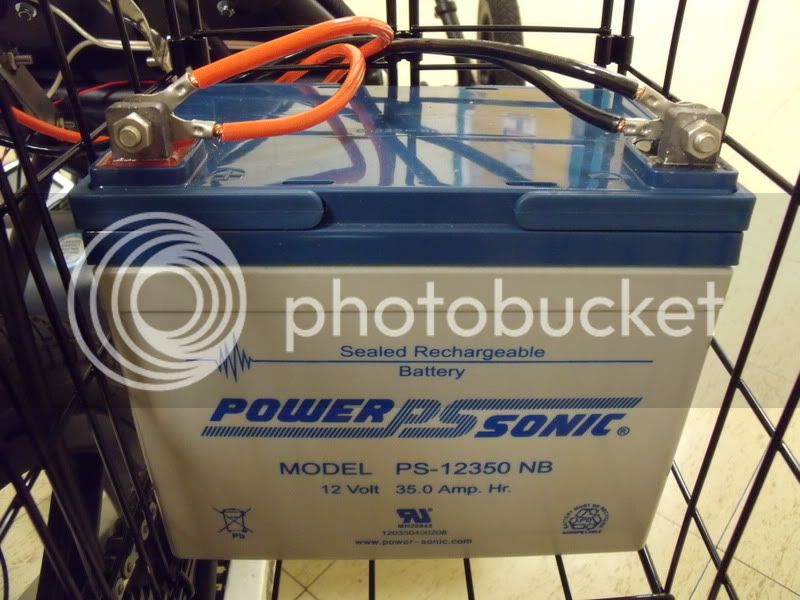
To multiply the torque to get acceptable acceleration and hill climbing, I placed a 60 tooth sprocket on the freewheel hub. Thanks to DrunkSkunk for that idea.
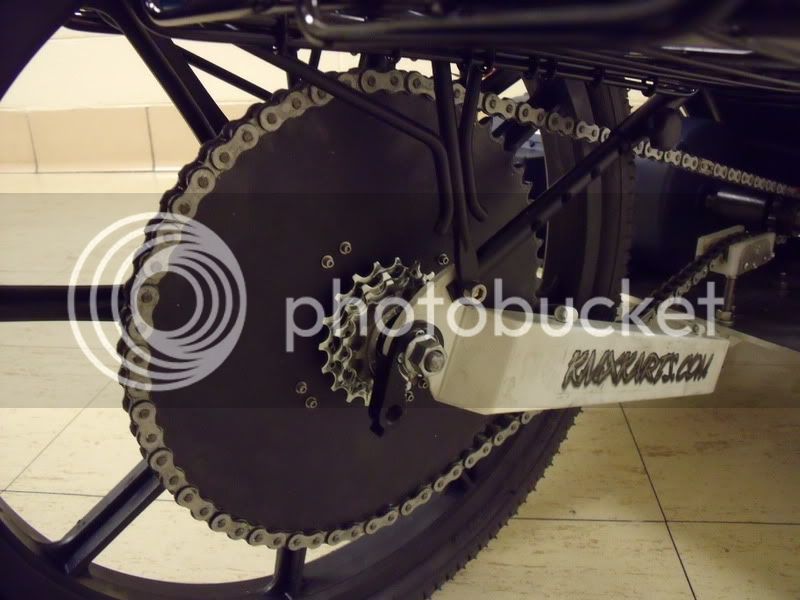
With an 11 tooth front sprocket,
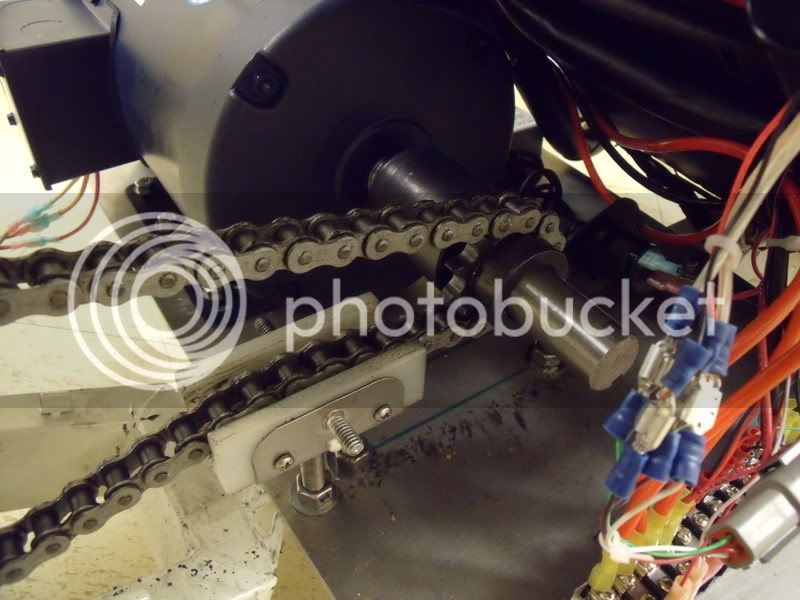
torque is multiplied by around 5.45. Rated torque is 6 ft-lbs, but 150% (9 ft-lbs) is available at locked-rotor (dead stop):

So I'll get about 9 * 5.45 = 49 ft-lbs at a dead stop, which matches pretty well with my old BLDC hub motor. Top speed suffers, and at 60 Hz my 1740 rpm gets cut to 319 rpm at the wheel, so I extended the controller's frequency range to 100 Hz to boost the top speed from 20 mph to 33. You pay for that speed with some torque loss in the "field weakening" regime of course. I'll keep an eye on the speed with the Cycle Analyst.
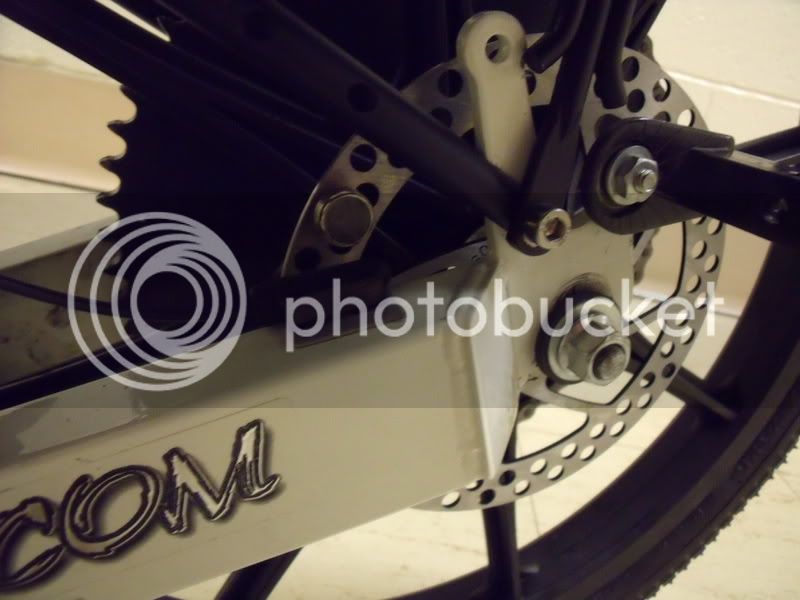
I'm sure everyone saw the ANSI 40 chain on the rear two sprockets as well. Here's something I made that I'm kind of proud of - a threaded bolt-adjustable chain tensioner:
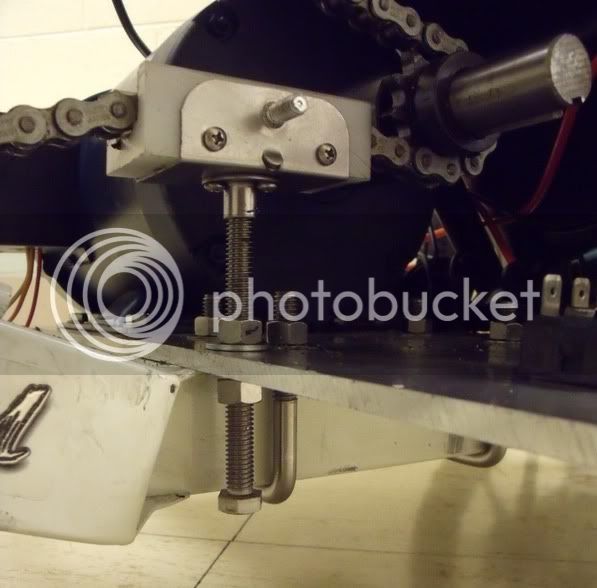
It allows me to get the chain tension just right without needing half links or scooting the motor around on its mounts. The terminal block allows you to access the + and - 12V buses as well as the Cycle Analyst electronics. Here, you see 7 +12VDC slots, 6 Cycle Analyst Slots, and 7 -12VDC slots from left to right. The missing two CA ports are for USB data collection. The plugs are for the lights and to disconnect the CA.
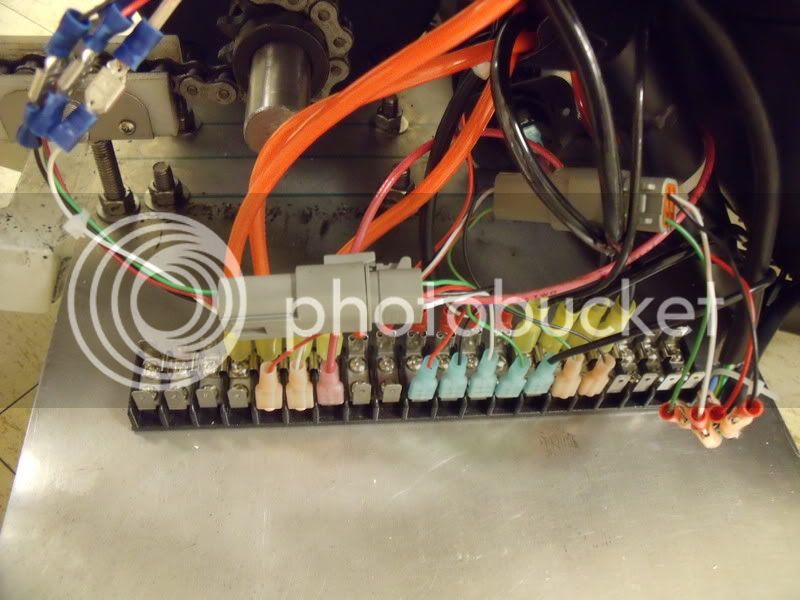
I have a (currently) hand-held throttle potentiometer (0 to 10 V signal) to control the motor speed remotely. I may mount this in the future.
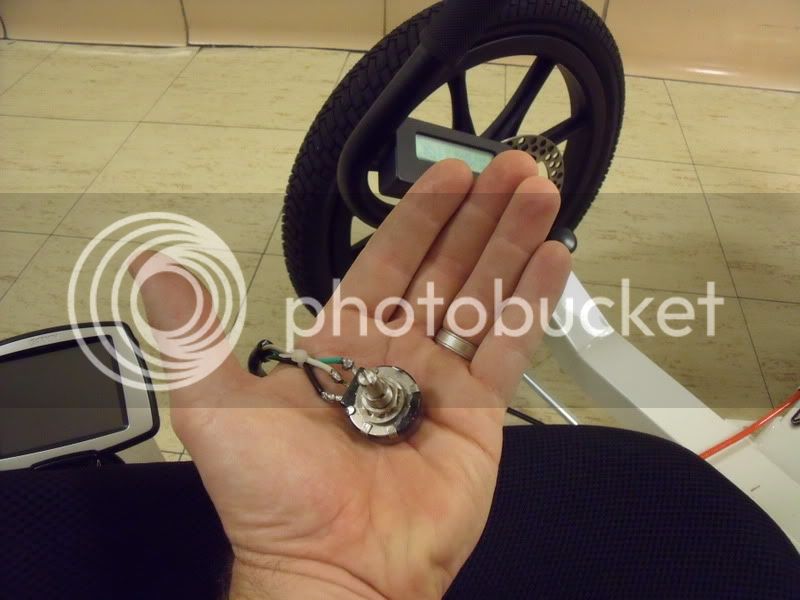
Here's the overall product.
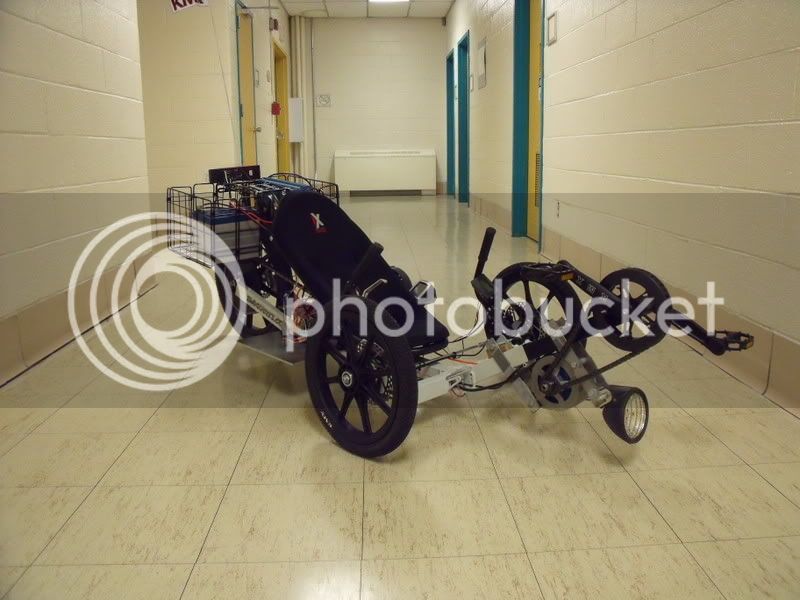
Some video: first, a spinup of the motor (effective 0 - 33 mph wheel speed)
[youtube]jPmKgRxWWnA[/youtube]
The same thing with a view of the motor phase current displayed by the controller. There's a decimal point between the digits.
[youtube]pdER4Bg16CA[/youtube]
I think about the present arrangement as the trike's "city mode," with probably lots of range, but relying heavily on the battery. This is the configuration I'm using for initial tests. When it is outfitted in "cross-country mode," imagine the following. First, replace the 12 V battery with three 16 V, 330 F ultracapacitor modules ganged in parallel for a 16 V, 990 F combination, which still fits in the right-hand rear basket:
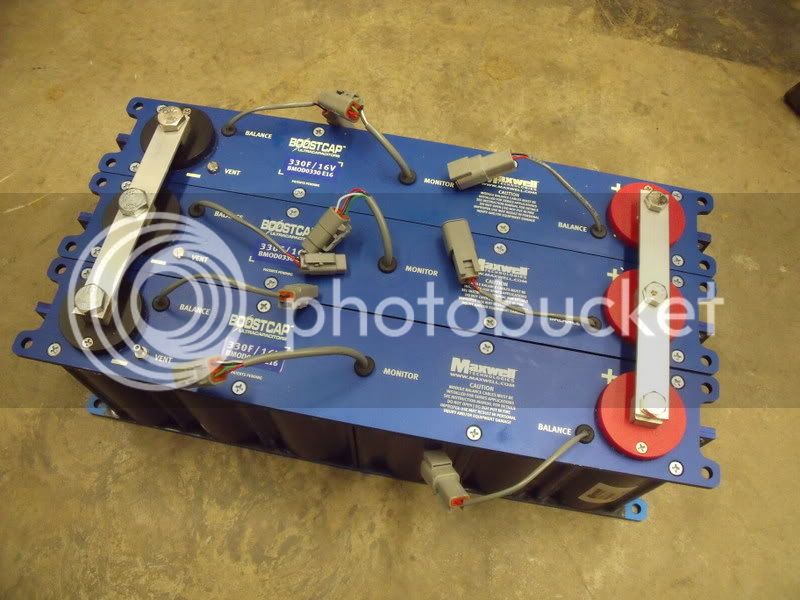
That will be the electrical storage buffer. I'll have a rear trailer, the same one as the other bike had, to carry a small 900 W generator (25 lbs) and a battery charger, which can send up to 30 A to maintain 13.5 V over the DC storage system.
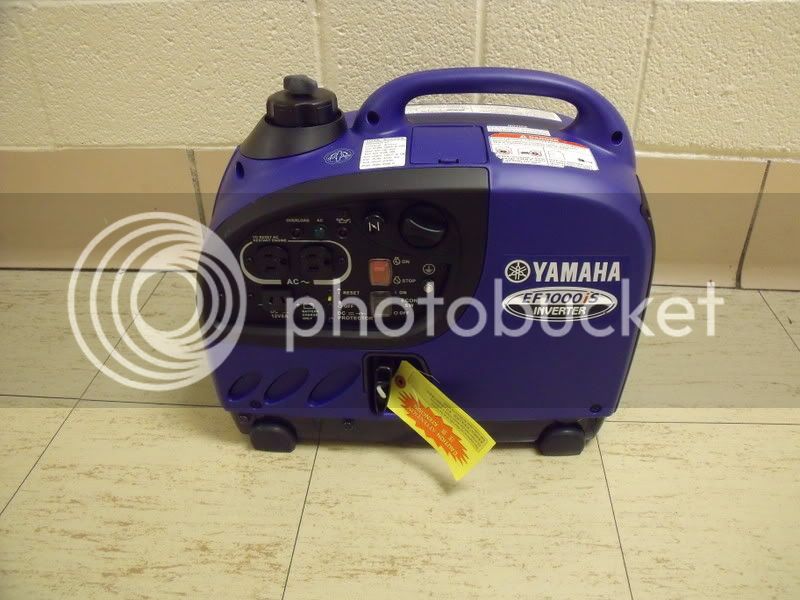
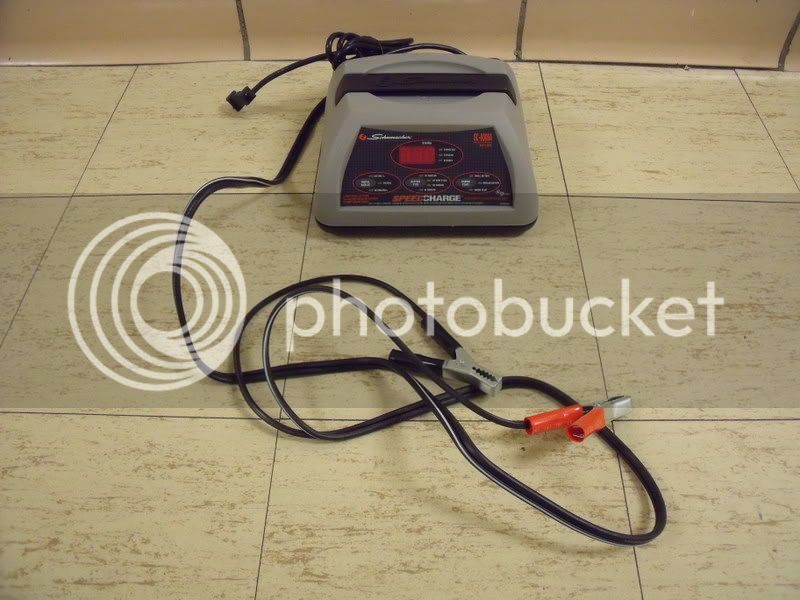
The generator runs for 12 hours on one quarter load (~225 W) using two thirds of a gallon of gasoline. The entire electronics system is 93% or better efficiency throughout, and the motor has an 84% efficiency at its rated load. If I run 25 mph at that power draw, that's close to 450 mpg. Pedaling could help that number too, I guess.
So, that's it. The AC motor has a lot of advantages; cheap, long life, easy control, good high-speed torque, no power drop at high speed. Thanks to safe for posting this plot in his thread on a separate board (and thanks for the brainstorming, too):
Link to MotoredBikes Thread
If you can handle the additional weight and space for the AC motor, it's a nice option. Safety is nice, too; although this system has some high voltages inside of it, the only voltage a user might possibly touch is 12 VDC. Not bad.