I posted this in your other thread, but since you made a whole new one for this question I'll just copy it here, too.
Disabling LVC might be possible, but is not generally a good idea (see the post below the first quote below for battery specific reasons).
It's not just there to protect the battery, but also the controller. If battery drops too far, the LVPS in the controller may not be able to convert battery voltage to the correct voltages to run the rest of the controller properly, or it may stress the parts in the LVPS depending on it's design.
If it's low enough, it also can't generate the full voltage to drive the FET gate drivers, so the FETs aren't being fully turned on or off, and/or not as fast as they should, so they heat up and can fail.
Anyway, got
this controller in the meantime since it was locally available while I find a "perfect" controller. It's XLD Brainpower LSD149. If anyone have any tips for those, they are of course welcome.
There are some threads for XunLida / Brainpower controllers with some info, if you poke around.
Seems like it should be fine out of the box but one thing I'm worried about is Low Voltage Cutout. It's written as 42V for 48V on the controller. I have 50E cells which have 2.5 voltage cutout, I wouldn't go that low but they are fine up to about 2.8 volts which is 36.4 v so I would be leaving quite a bit of capacity on the table.
Ideally I would remove LVC all together but apparently this will affect regen.
You don't really want to run cells down that far, if you want to keep the battery unstressed and long-lasting. 3.0-3.2v / cell is the lowest I would use for a controller LVC--they're set this way to prevent potential cell damage...especially since almost no ebike battery is made of matched cells, so they don't stay balanced, and you can have some cells that are much lower than others. If you use a controller LVC (that can't actually know how low the cells are) that's at or near the actual per-cell-level LVC, then you can damage cells that are below that average voltage. Such damage is cumulative, will shorten the pack life, and if severe enough can create a fire risk.
If you are running a typical BMS on the pack, then that will help do cell-level protection, but the BMS LVC is an emergency shutdown, cutting all power to save the cells from damage. You don't use that for everyday protection, so the controller LVC is set higher on purpose, to use as everyday protection. If there is no BMS, then the controller LVC is your only protection, so setting it higher is even more important.
So for a 13s pack (48v) you'd usually use a 41-43v controller LVC. For a 14s pack (52v) a 44-46v LVC.
There is not all that much actual capacity in most cells below 3v, and some not even below 3.2v at higher currents. See the testing charts here for this cell:
for some info on that; first chart copied below:
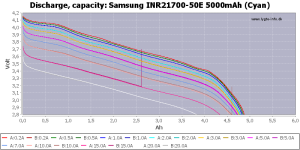