NeilP
1 GW
Yep welding an option too, but then you get the usual heat stresses if you are not careful. So then you are into heat treating/de stressing etc..all psosible of course
here is what I was thinking
just a quick rough paper sketch, totally not to scale
cable goes in from LHS thought 8mm cross bore drilling, 9 or 10 mm still gives good amount of meat on shaft if LHS axle nut is 30mm
..but witha huge torque plate like this, as long as it is secured to frame well enough, then axle nuts almost become an irrelevance. So dispense with the nut and use the start of the cross drilling, tapped to take a set screw and big flat washer or plat, and the end of the axle is then flush o the side of the frame...clamping dropouts required of course, clamping up from underneath
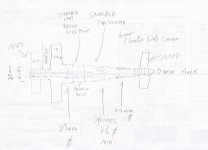
here is what I was thinking
just a quick rough paper sketch, totally not to scale
cable goes in from LHS thought 8mm cross bore drilling, 9 or 10 mm still gives good amount of meat on shaft if LHS axle nut is 30mm

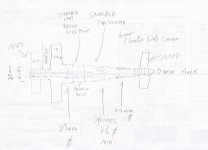