karma said:i was thinking on doing that, what are the fets rated at? Doesn't the + out run threw the fets?
Right, the current still goes through the FETs so you don't want to exceed their rating. If the Ping BMS was rated for 40 amps, then use a 40 amp fuse. A fuse will allow a higher current for a very short time.
phenomatuan said:Hi Guys,
Yes, I intend to run the packs in series and I've got a cycle analyst. I'm getting 2 schools of thought in regards to protection: using diodes (as in Schottky Diodes?) vs. LVC Boards. I really dont know the advantage of one over the other.
If you're using the stock BMS, then it already has a LVC built in. You just need diodes.
The diodes are only there to protect the BMS against overvoltage if the other one trips.
The diodes can be regular diodes, but need to handle the full amp and volt rating of the battery. The diodes go across the wires coming out of the BMS (to controller).
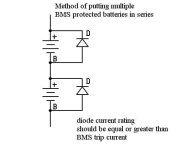