Tetrault
10 mW
Hello, all. Been reading and trying to learn things on the forum for a while but just joining now. I appreciate everyone’s knowledge here, thank you! Have gotten into commuting to work by Ebike. Have a two OEM bikes, but want something a little different. Something fast and stable that can reliably cruise near 30mph (48 kph) for my commute.
A great Ebike starts from a great bike, right? And what better place to find a great bike than people’s trash? This red one should be good.
It sports 26x2 inch tires, a 1 inch threaded fork, single piece crank, rim brakes, super solid rear dropouts. You know, top of the line. Sorry, no pic of it together as I was so excited to get started with this project…
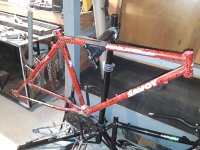
A great Ebike starts from a great bike, right? And what better place to find a great bike than people’s trash? This red one should be good.
It sports 26x2 inch tires, a 1 inch threaded fork, single piece crank, rim brakes, super solid rear dropouts. You know, top of the line. Sorry, no pic of it together as I was so excited to get started with this project…
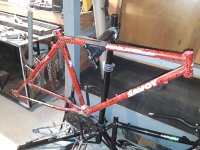
Last edited: