Eastwood
100 kW
- Joined
- Jan 13, 2021
- Messages
- 1,479
you want nickel plated stuff when any moisture is present.
Yes I agree. I typically always use marine grade/tinned copper wires and lugs. Although this time my busbars are bare copper no nickel coating. Then also, the terminals on my 3Shul controller are non tinned Cooper. So I figured would just stick with bare copper wire, since nothing else has protection. Nothing will come in direct contact with Water.
Talking about wicking moisture after you crimp your 4/0 wire into a lug wouldn't you solder the copper wire ends at the end that points out the end of the lug so moisture doesn't weep in ?
Solder on the ends? These lugs only have one hole so once it’s crimped, it’s sealed with heat strink.
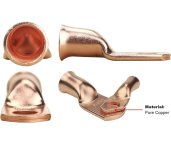
Plus how's that new spot welder of yours working. What do you find most useful the two pens the one handed handle or it looks like you put the machine on its end and plug in the lever activated spot welder attachment.
I was hoping just to get away with the handheld pens but I'm doing 120 cells so. ? Thanks
Haven’t tested the spot welder yet, will soon though!
Still have been ordering materials for this battery build but think of got everything on order now and the battery assembly will start soon. Ordered the BMS today, the 380a continuous 950peak version. Went with the 2.4” display.