Some background. I've been wanting to build an EV of some kind for a long time. Rapidly changing technology and a small number of reference builds (in the classes of vehicles that interest me) have made this feel risky.
About a year back, a guy I work with finished this WR250 conversion.
Doug freely admits that there was a lot of "Suck it and see" engineering involved but, it has to be said, he did a really good job on the bike. Every design decision he made ended up with a totally usable outcome and, looking at the bike, you can easily see what you would change and how much you would change it by to get a different kind of machine. In short it's a great bike and an excellent reference point for other builds.
I say it's a great bike, but to be sure, we put road tires on it and rode it to work and back for a week. The idea being to get past the novelty of a new bike and really measure currents and temperatures in my intended use case.
By the end of that week I wasn't shy with the throttle and the QS180 motor wasn't getting more than slightly warm at the end of the freeway leg of the trip delivering 10-12kW continuously. The battery pack was almost big enough for a weeks commuting and the fardriver 96V controller was holding up well. Like I said, it's a great bike!
OK, so now I'm feeling confident.
The plan is a cafe racer style bike.
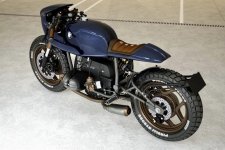
and I like the BMW R's because they have nice big cradle frames, single sided swingarms, and shaft drives...
Time to spend some money!
I bought a 1985 R80 mono,
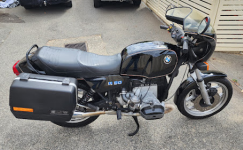
for more $ than I should have spent.
Part of my intention with this project is show what kind of street legal bike can actually be built with the low cost EV hardware that's readilly available.
I rode this bike for a couple of weeks so that I would be able to compare it to the finished article. Sadly, this involved fixing a bunch of stuff.
I confess, at first, I was riding the bike and looking at the retro BMW guys thinking "What are you smoking, these things are crap!"
Then we put it on the dyno and the bike was producing 8kW at 100km/hr. Fixing the carbies got us up to respectable numbers and balancing them got the bike to a point where I was starting to second guess my decision to convert it!
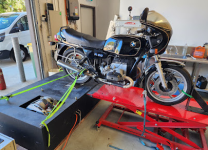
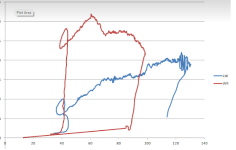
As with all dyno results the absolute numbers are irrelevant, although we checked the calibration of this one. What you see there is the R80 in blue, and some early test data from Doug's WR250 in red. At about this point, my nostalgic affection for the R80 faded.
So I sent off my application to modify the bike
This is a simple online form
And started ordering parts. We buy a lot of stuff out of China, so we're quite familiar with the process. With the exception of Harry, at QS motors who is excellent, the other vendors were disappointing.
So I now have a motor:
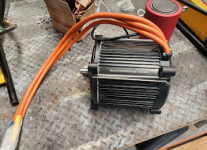
After getting stuffed around and enduring three or 4 vendors doing the bait and switch thing, I finally got hold of Fardriver and they agreed to make me a ND1081800B controller, though they want 2 months to build and ship it???
After only a month of stuffing around, I'm told that a box of Molicell P45B cells will ship today.
I've made some progress on the build, this'll do for an intro post.
About a year back, a guy I work with finished this WR250 conversion.
Doug freely admits that there was a lot of "Suck it and see" engineering involved but, it has to be said, he did a really good job on the bike. Every design decision he made ended up with a totally usable outcome and, looking at the bike, you can easily see what you would change and how much you would change it by to get a different kind of machine. In short it's a great bike and an excellent reference point for other builds.
I say it's a great bike, but to be sure, we put road tires on it and rode it to work and back for a week. The idea being to get past the novelty of a new bike and really measure currents and temperatures in my intended use case.
By the end of that week I wasn't shy with the throttle and the QS180 motor wasn't getting more than slightly warm at the end of the freeway leg of the trip delivering 10-12kW continuously. The battery pack was almost big enough for a weeks commuting and the fardriver 96V controller was holding up well. Like I said, it's a great bike!
OK, so now I'm feeling confident.
The plan is a cafe racer style bike.
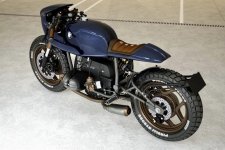
and I like the BMW R's because they have nice big cradle frames, single sided swingarms, and shaft drives...
Time to spend some money!
I bought a 1985 R80 mono,
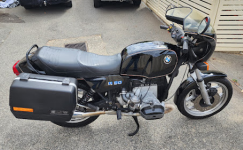
for more $ than I should have spent.
Part of my intention with this project is show what kind of street legal bike can actually be built with the low cost EV hardware that's readilly available.
I rode this bike for a couple of weeks so that I would be able to compare it to the finished article. Sadly, this involved fixing a bunch of stuff.
I confess, at first, I was riding the bike and looking at the retro BMW guys thinking "What are you smoking, these things are crap!"
Then we put it on the dyno and the bike was producing 8kW at 100km/hr. Fixing the carbies got us up to respectable numbers and balancing them got the bike to a point where I was starting to second guess my decision to convert it!
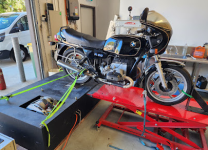
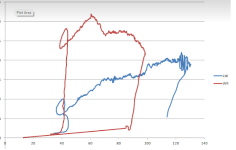
As with all dyno results the absolute numbers are irrelevant, although we checked the calibration of this one. What you see there is the R80 in blue, and some early test data from Doug's WR250 in red. At about this point, my nostalgic affection for the R80 faded.
So I sent off my application to modify the bike
This is a simple online form
And started ordering parts. We buy a lot of stuff out of China, so we're quite familiar with the process. With the exception of Harry, at QS motors who is excellent, the other vendors were disappointing.
So I now have a motor:
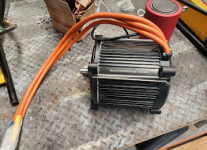
After getting stuffed around and enduring three or 4 vendors doing the bait and switch thing, I finally got hold of Fardriver and they agreed to make me a ND1081800B controller, though they want 2 months to build and ship it???
After only a month of stuffing around, I'm told that a box of Molicell P45B cells will ship today.
I've made some progress on the build, this'll do for an intro post.