wb9k
10 kW
Hi all,
After a month or two of improvements and tweaks, I'm finally getting around to posting about the motorcycle I recently picked up. The bike is a 1984 Honda VF500F Interceptor that was converted initially two owners ago, and taken to functional completion by the guy I got the bike from. Setup is basically a series-wound forklift motor driven by a Curtis 36-48V, 300A controller. Batteries were 48V/35Ah of lead when I got it. Here are a couple of photos of the bike as-received:
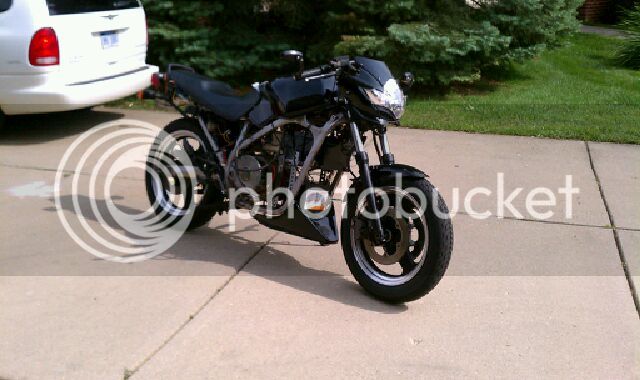

Performance with lead was pretty abysmal. A test ride with fully-charged batteries made it clear the bike had decent performance potential (good enough to meet my present needs/desires), but range was 8 miles at best, and after the first mile or so, voltage drop was bad enough to cause the controller to start dropping out, resulting in a chattering chain and obvious loss of power. Top speed was about 45 mph. The lead didn't last the first night in my garage.
After some experiments with an undersized A123 pack (26650's in 16S, 11P), I decided it would be fairly simple to mount four 60Ah A123 starter battery modules, Amp 20 pouch cells in 16S 3P. This gives us a safe amount of overvoltage with 52.8V nominal from the pack. The install is coming along gradually as I continue to ride the bike to work and around town. I've also painted and remounted some of the original plastic, upgraded the contactor, precharge resistor, and cleaned up the harnessing significantly. Also removed the DC/DC that was sourcing 12V before and replaced it with a small 12V battery. This enabled me to float the 48V pack off the chassis--it had been grounded to the frame, a configuration forced by using the 48V battery to drive the 12V DC/DC. I also added a fuse (rated 250 Amps) at the center of the 48V pack. Here are some pics of the bike as it sits today:




You can see my mobile charging arrangement in some of these pics. I'm using a DC supply (24V mobile, 35V at home) to drive a DC/DC converter to 57.3V. Each battery module has balancing provided by the usual electronics used in the native application, not fully exploited here.
At this point I am hesitant to invest much more time in improving this present iteration, though the control electronics and styling leave much to be desired. Performance is now what I consider "usable" but not yet all I would like. Range is around 30 miles on a charge. Top speed is ~60 mph, holding 55 mph is no problem in real-world traffic. Acceleration is pretty strong above 20 mph or so, a bit on the sluggish side below that--surely due mostly to the controller. For next season I want to take the bike to another level. I'm contemplating a hub motor along the lines of the Cromotor Mammoth. This would open up space on the frame for two more battery modules, taking me over 80V nominal and 60 Ah. I expect this would easily achieve highway speeds and maybe 40-50 miles of range if the hub motor is much more efficient than my present motor. I would also like more acceleration out of the hole. I have no idea what controller I might want to use when changing the motor. I'm reading and learning a lot about motors right now and matching controllers to them. Can anyone give feedback on the direction I have proposed here?
I'll get more pics with the (used to be) gas tank and seat removed posted soon.
After a month or two of improvements and tweaks, I'm finally getting around to posting about the motorcycle I recently picked up. The bike is a 1984 Honda VF500F Interceptor that was converted initially two owners ago, and taken to functional completion by the guy I got the bike from. Setup is basically a series-wound forklift motor driven by a Curtis 36-48V, 300A controller. Batteries were 48V/35Ah of lead when I got it. Here are a couple of photos of the bike as-received:
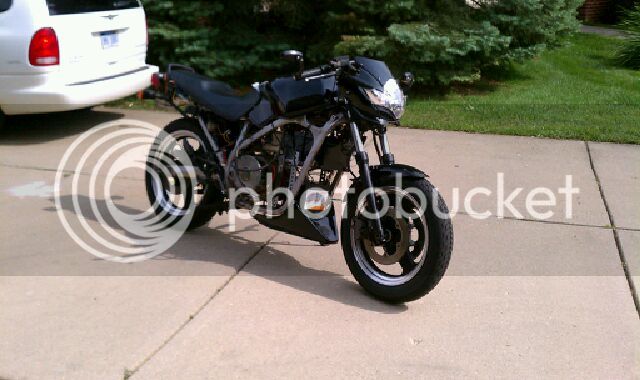

Performance with lead was pretty abysmal. A test ride with fully-charged batteries made it clear the bike had decent performance potential (good enough to meet my present needs/desires), but range was 8 miles at best, and after the first mile or so, voltage drop was bad enough to cause the controller to start dropping out, resulting in a chattering chain and obvious loss of power. Top speed was about 45 mph. The lead didn't last the first night in my garage.
After some experiments with an undersized A123 pack (26650's in 16S, 11P), I decided it would be fairly simple to mount four 60Ah A123 starter battery modules, Amp 20 pouch cells in 16S 3P. This gives us a safe amount of overvoltage with 52.8V nominal from the pack. The install is coming along gradually as I continue to ride the bike to work and around town. I've also painted and remounted some of the original plastic, upgraded the contactor, precharge resistor, and cleaned up the harnessing significantly. Also removed the DC/DC that was sourcing 12V before and replaced it with a small 12V battery. This enabled me to float the 48V pack off the chassis--it had been grounded to the frame, a configuration forced by using the 48V battery to drive the 12V DC/DC. I also added a fuse (rated 250 Amps) at the center of the 48V pack. Here are some pics of the bike as it sits today:




You can see my mobile charging arrangement in some of these pics. I'm using a DC supply (24V mobile, 35V at home) to drive a DC/DC converter to 57.3V. Each battery module has balancing provided by the usual electronics used in the native application, not fully exploited here.
At this point I am hesitant to invest much more time in improving this present iteration, though the control electronics and styling leave much to be desired. Performance is now what I consider "usable" but not yet all I would like. Range is around 30 miles on a charge. Top speed is ~60 mph, holding 55 mph is no problem in real-world traffic. Acceleration is pretty strong above 20 mph or so, a bit on the sluggish side below that--surely due mostly to the controller. For next season I want to take the bike to another level. I'm contemplating a hub motor along the lines of the Cromotor Mammoth. This would open up space on the frame for two more battery modules, taking me over 80V nominal and 60 Ah. I expect this would easily achieve highway speeds and maybe 40-50 miles of range if the hub motor is much more efficient than my present motor. I would also like more acceleration out of the hole. I have no idea what controller I might want to use when changing the motor. I'm reading and learning a lot about motors right now and matching controllers to them. Can anyone give feedback on the direction I have proposed here?
I'll get more pics with the (used to be) gas tank and seat removed posted soon.