I've basically determined that I'll be using my QS273 8000w hub motor for this build, the one that I'm currently riding on. Since that's decided, I can get to work on modifying the swingarm to accept a hub motor. Which means torque arms! I'm not even going to mention how embarrassed I am of my current build and how the motor is secured, I have learned a lot in 2 years and I'll be going with something more secure this time around.
The EX500 swingarm has nice square recesses around the axle holes, like many other Japanese motorcycles I've seen from this era. Keeping it simple and straightforward then, with minimal cutting and drilling to the steel: I need a square chunk of metal to fit into that recess from which I can fashion clamping style dropouts.
Started with a 3D printed stencil of my plan:
I'll just need to open up the back of the swingarm to slide in the hub motor, and a single drilled M8 hole through the flat face to keep it from sliding out the back. My prototype is also incorporating those stock torque arms that QSMotor sends you, the ones that are far too loose to work as a torque arm on their own, but still function well enough as a washer, spacer, and/or added insurance against the motor slipping off the swingarm.
I got real lucky on my trip to the scrapyard today and found some 20mm thick aluminum scraps that must have been off cuts or discards from a machine shop.
Because you see that the scraps already have several holes tapped with M8x1.25, exactly centered. Thanks for doing half of the work for me, scrapyard fairy! I just need to line up my stencil to incorporate the already-tapped holes:
And got to work with a hacksaw, angle grinder, drill press, ect.
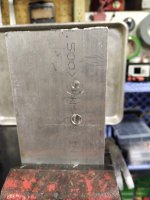
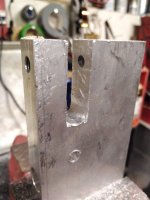
Not pretty, but it should do the job quite well, I kept the tolerances as close as I could to minimize wiggle. I'm still riding on the motor, but I 3d printed a copy of the axle to test fitment (which is M18 flatted to 14mm on two sides, for anyone who needs the info). That way I can get the swingarm all ready for the motor, so when it comes time to swap the parts over, I shouldn't have to waste too much time fabricating.
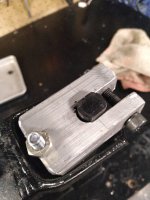
So the torque arms are held in place by the M8 bolt hole going through the stock QS torque arms, then the swing arm, then the toque arm. As well as being held in place vertically by the top and bottom pieces of metal from the swingarm. And of course the axle's nut on top of everything (not pictured cuz it's just a printed mockup for now). The axle will have 20mm of metal clamping it down. I know it's aluminum, but it's 20mm, and I can always find a local machinist later who might be willing to remake them for me out of mild steel. But it's certainly way better than what I'm riding on now!
One question. I've browsed the torque arm picture thread. Do I need to cut a stress relief line?
Like on the bottom. I've seen it on some, but not all of the DIY torque arms I've seen. Which is going to be better? I don't mind remaking another one, I still have plenty extra metal that I can use if I need to.