Hi guys! I know this is maybe not the main subject of this forum, but there's a lot of knowledge here, so I thought I should give it a go.
Long story short, I am building a powerwall, and scored a great deal on a 24kwh e-golf pack. I had limited time to do research, and after disassembling the battery, I found it was a little more challenging than I hoped for. The battery modules are welded together with aluminium bus bars, so I need to use them as is. There are 17 4s3p modules and 10 2s3p modules. I am building a 14s battery, so it will be 6 strings like this:

Battery will be connected to a 5kva inverter, so each string will not see much more than an average of ~16A flow. I might get another inverter in the long run, but then I will probably get anoter battery as well. In the original 88s3p configuration the battery dlivers more than 200A, so it will be lazy days for the cells.
My problem are the parallel connections. It is not easy (at least not with any of mine equiment) to solder or weld anything to the bus bars. The original bus bars are conected to some spot welded cable lugs, that I can use for attachment for balance wires. Problem is that in my eyes, this looks so sketchy. The cells are perfectly balanced and in good shape, so I guess that not much current will flow thorough the parallel wires, but still.... Does not look right to me. Am I being overly sceptical?
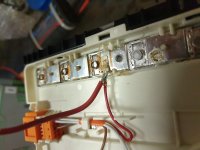
I really wanted to use a batrium BMS instead of the usual Aliexpress smart bms'es I've been using before, but then I will either have to build 6 battery strings or use this solution for parallel wires.... Buying batrium cell monitors for 6 strings ends up costing more than what I paid for the battery, so that is not really an option.
Should I just build 6 strings and attach an ANT BMS to each string? I kind of feel like that is my best option now....
What would you do? I am stuck now and cant decide. I would REALLY appreciate pro's and con's or other solutions now, and det on with the build.
Long story short, I am building a powerwall, and scored a great deal on a 24kwh e-golf pack. I had limited time to do research, and after disassembling the battery, I found it was a little more challenging than I hoped for. The battery modules are welded together with aluminium bus bars, so I need to use them as is. There are 17 4s3p modules and 10 2s3p modules. I am building a 14s battery, so it will be 6 strings like this:

Battery will be connected to a 5kva inverter, so each string will not see much more than an average of ~16A flow. I might get another inverter in the long run, but then I will probably get anoter battery as well. In the original 88s3p configuration the battery dlivers more than 200A, so it will be lazy days for the cells.
My problem are the parallel connections. It is not easy (at least not with any of mine equiment) to solder or weld anything to the bus bars. The original bus bars are conected to some spot welded cable lugs, that I can use for attachment for balance wires. Problem is that in my eyes, this looks so sketchy. The cells are perfectly balanced and in good shape, so I guess that not much current will flow thorough the parallel wires, but still.... Does not look right to me. Am I being overly sceptical?
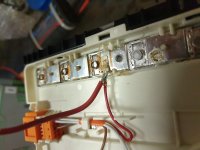
I really wanted to use a batrium BMS instead of the usual Aliexpress smart bms'es I've been using before, but then I will either have to build 6 battery strings or use this solution for parallel wires.... Buying batrium cell monitors for 6 strings ends up costing more than what I paid for the battery, so that is not really an option.
Should I just build 6 strings and attach an ANT BMS to each string? I kind of feel like that is my best option now....
What would you do? I am stuck now and cant decide. I would REALLY appreciate pro's and con's or other solutions now, and det on with the build.