doingresearch
1 mW
hi all!
last year i got my new delfast top3.0i ebike. i use it in winter and few weeks in spring. then on a ordinary charging session the thing broke. smoke came out of motor controller and that was end of story. because i have full waranty i tried to get help from delfast support. did not work as expected. delfast stopped talking to me for no reason.
now i sit here and try to figure out what i need to repair my broken ebike. what i need in first place is a controller, that works like this one -> Brushless DC Controller for eBike
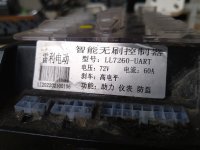
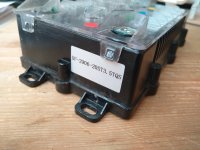
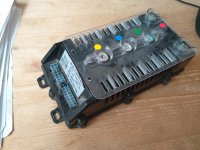
what also broke is the DC-buck converter which brings the voltage from battery (84V) down to 12V. the capacitor in this converter has blown up. by the way. i like to replace the electronics with high quality components only. i'm not intrerested to use 5$ buck-converter in a € 7000,- ebike.
i also checked the battery which is fine and has not been damaged in any way.
it would be very helpful if you can give me some tips where to look for such a controller or maybe i can upgrade to bigger motor/controller combination?
thank you very much
regards from austria!
last year i got my new delfast top3.0i ebike. i use it in winter and few weeks in spring. then on a ordinary charging session the thing broke. smoke came out of motor controller and that was end of story. because i have full waranty i tried to get help from delfast support. did not work as expected. delfast stopped talking to me for no reason.
now i sit here and try to figure out what i need to repair my broken ebike. what i need in first place is a controller, that works like this one -> Brushless DC Controller for eBike
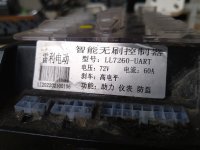
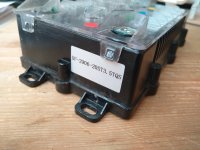
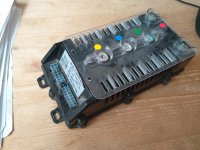
what also broke is the DC-buck converter which brings the voltage from battery (84V) down to 12V. the capacitor in this converter has blown up. by the way. i like to replace the electronics with high quality components only. i'm not intrerested to use 5$ buck-converter in a € 7000,- ebike.
i also checked the battery which is fine and has not been damaged in any way.
it would be very helpful if you can give me some tips where to look for such a controller or maybe i can upgrade to bigger motor/controller combination?
thank you very much
regards from austria!