HalbachHero
100 W
- Joined
- Apr 5, 2021
- Messages
- 228
So I picked up the epoxy and finished the new stator. But again there are some issues. This one did not seem to break any wires which is great, however the angles of the pins and the extra length added to the inner and outer diameter pins made this quite a bit bigger, and will not fit in the rotor.
This time I removed the pins in the center before I glued it. This allowed me to flatten the inner diameter as much as the outer, but the wires wanted to go everywhere once I pulled the pins out. So I only did this to the inner diameter. This makes me think that the only reason its thicker is because I didnt properly press it in those spots on the first version of this that I tried.
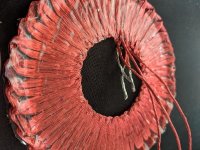
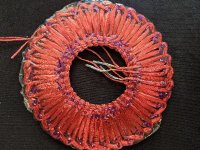
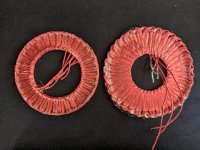
I am going to try this again, and I will make a jig/press that will allow me to hold the stator in place while I remove the pins, then I can add parts for the inner and outer diameter and press those parts too. I assume the wires will find a place to sit. It might be a bit larger in diameter still, but hopefully a lot less because ill remove the extra set of pins on the inner and outer. this should make it easier to wind as well.
I do worry about the rigidity of all of this. the Epoxy alone does not make it stiff. the stator has the feel of hard rubber. you can deform it pretty easily. I purchased some fiberglass sheet that I was hoping might help if I incorporate it on the top and bottom face, but I still think it will be too flexible. The fiberglass around the inner/outer edge might be needed. But since I got it so thin with the same number of turns. I think I have a little wiggle room for extra material
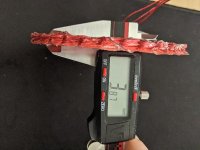
This time I removed the pins in the center before I glued it. This allowed me to flatten the inner diameter as much as the outer, but the wires wanted to go everywhere once I pulled the pins out. So I only did this to the inner diameter. This makes me think that the only reason its thicker is because I didnt properly press it in those spots on the first version of this that I tried.
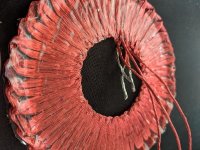
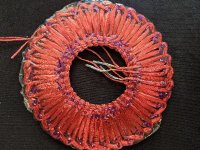
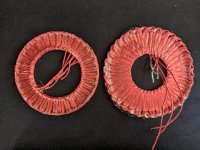
I am going to try this again, and I will make a jig/press that will allow me to hold the stator in place while I remove the pins, then I can add parts for the inner and outer diameter and press those parts too. I assume the wires will find a place to sit. It might be a bit larger in diameter still, but hopefully a lot less because ill remove the extra set of pins on the inner and outer. this should make it easier to wind as well.
I do worry about the rigidity of all of this. the Epoxy alone does not make it stiff. the stator has the feel of hard rubber. you can deform it pretty easily. I purchased some fiberglass sheet that I was hoping might help if I incorporate it on the top and bottom face, but I still think it will be too flexible. The fiberglass around the inner/outer edge might be needed. But since I got it so thin with the same number of turns. I think I have a little wiggle room for extra material
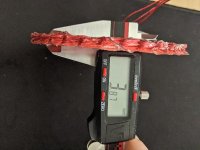